Wooden Patterns and Core Boxes
We make wooden patterns that are in line with the needs of our customers by the combination of the traditional manual technique which we have cultivated over 70 years since we were founded and the latest technology. We use tools such as chisel and plane as well as 3D CAD/CAM/CAE and digital technical skills at machining centers.
Our achievements: Cylinder head, Cylinder blocks, Transmission cases, EV motor cases, Medium and large subframe, etc.
STEP1
Designing Patterns
Create casting plan such as runners required for casting. Develop into a sand mold. Confirm that there is no problem in fluidity and solidification analysis(CAE).
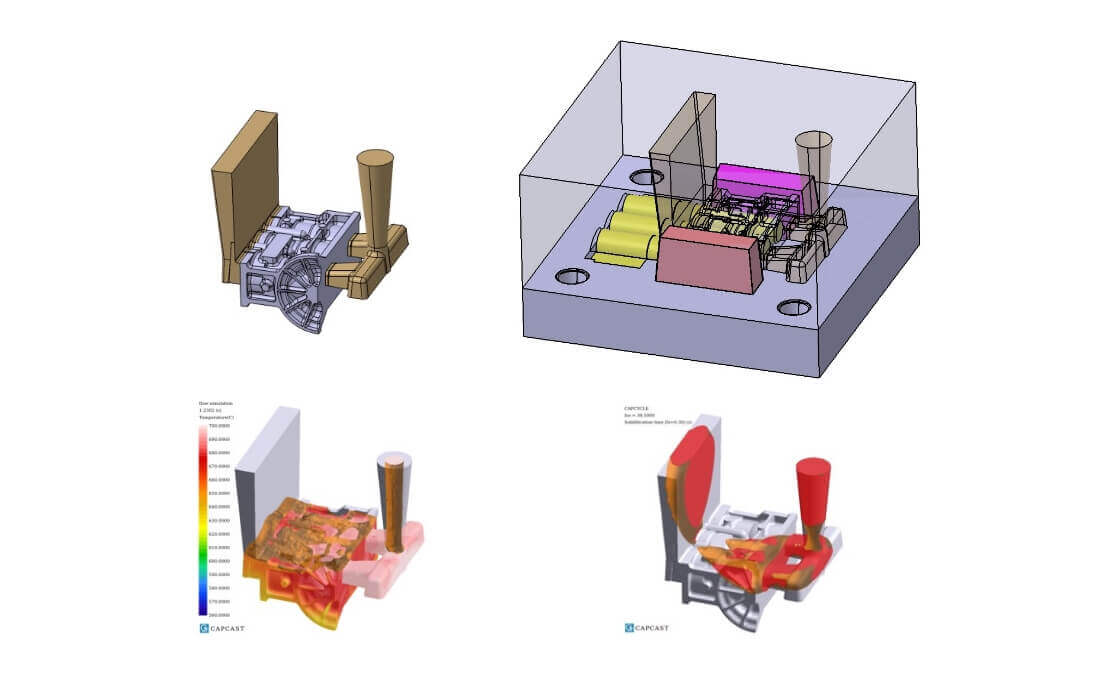
STEP2
Creating Processing Data
Create an NC machining program from a 3D model.
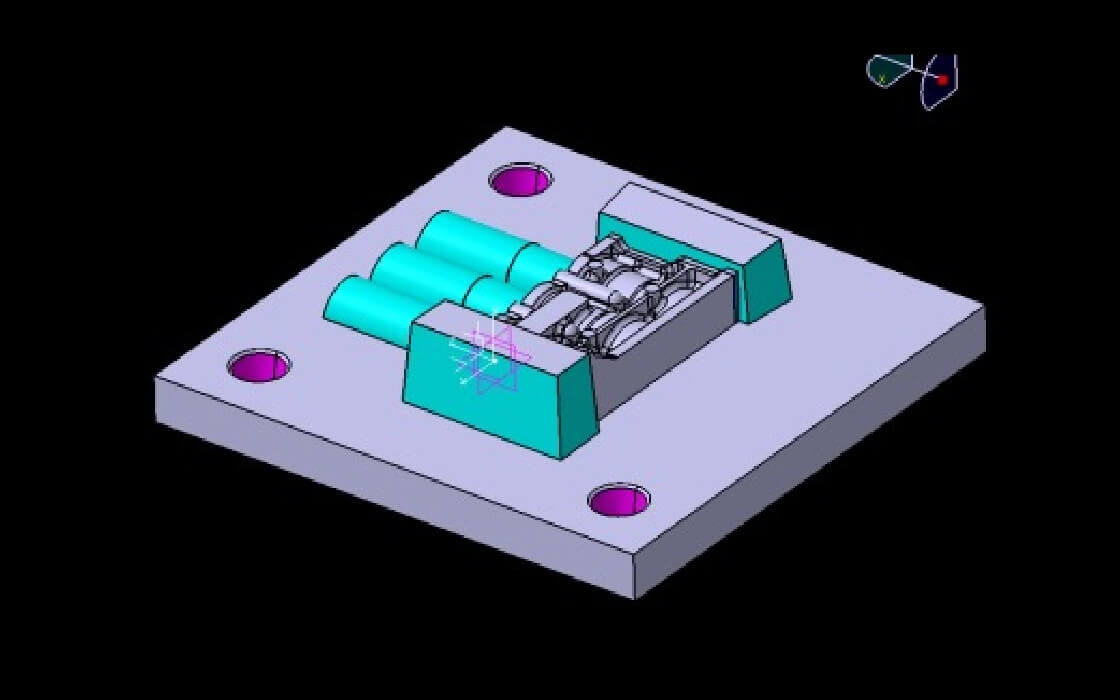
STEP3
Machining
Process with an NC machine.
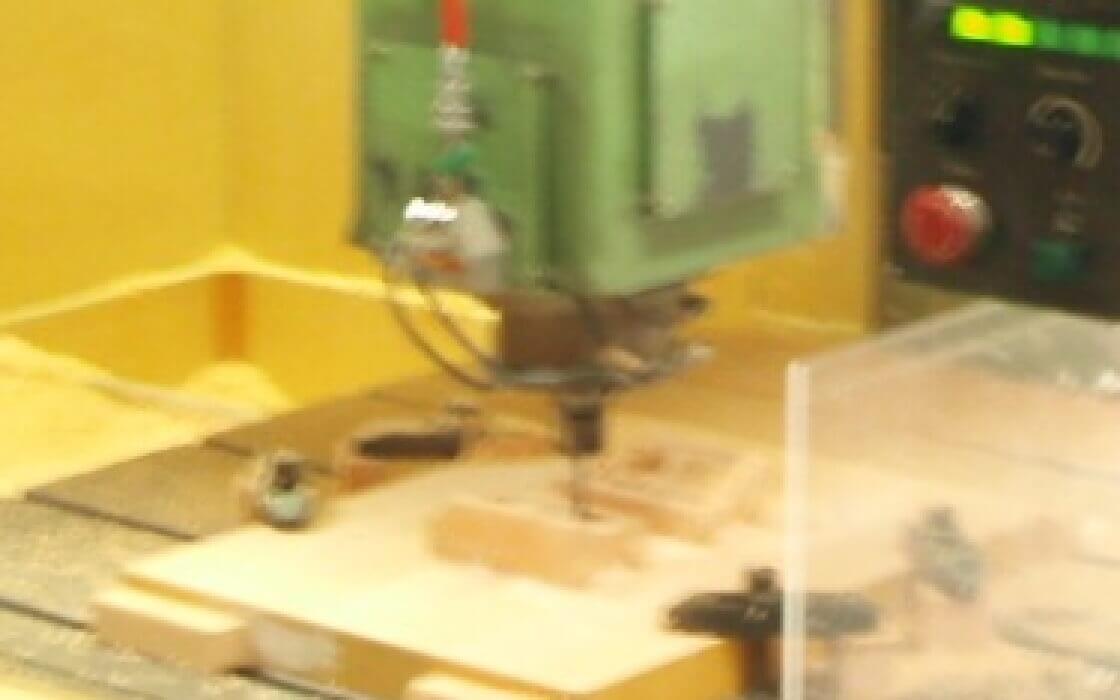
STEP4
Finishing and Assembling
Add a frame, runners, risers etc.
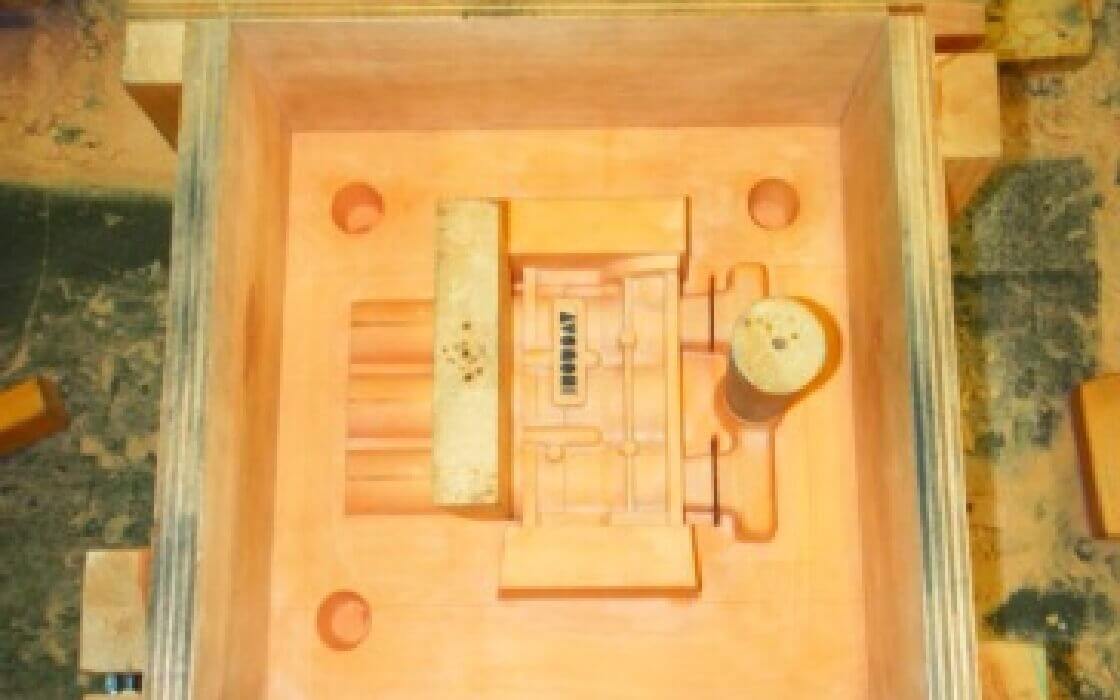
STEP5
Inspection
Visualize and evaluate the difference between 3D CAD data and the wooden pattern using 3D scanning measuring devices.
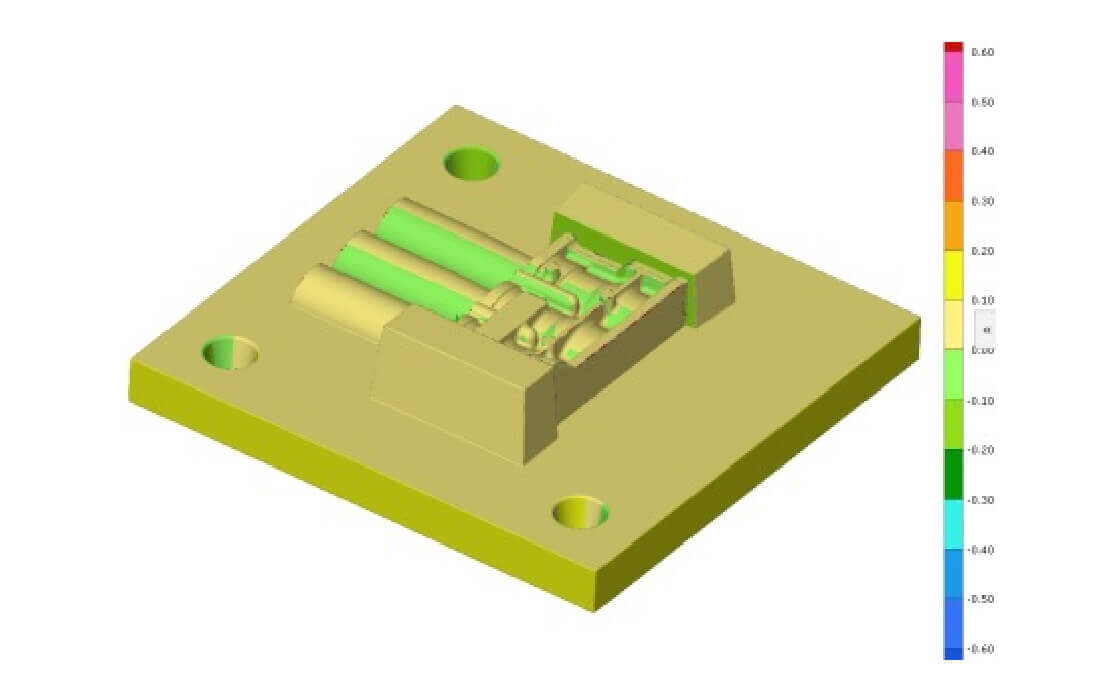
Metallic Patterns and Core Boxes
Our achievements: Metallic patterns for mass production of sand castings, Lost-wax patterns for gas turbines, Metallic patterns for low pressure die-casting, Metallic patterns for gravity die casting, etc.
We are able to make high quality metallic patterns in a short period of time by using 3D design and the latest 5-axis MC.
We have a non-contact 3D measuring machine (ATOS) and a contact type coordinate Measuring Machine to support and guarantee our inspection.
STEP1
Designing Patterns
We design 3D models by using 2D / 3D properly according to customer needs. If necessary, we also analyze the temperature distribution of the metallic pattern.
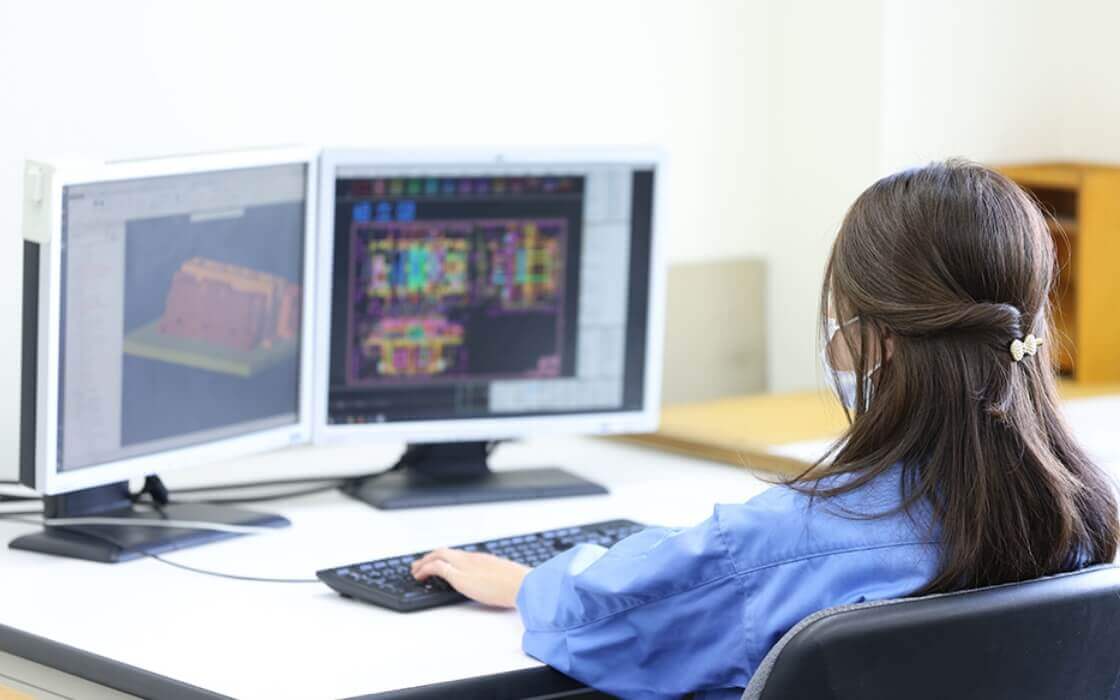
STEP2
Creating Processing Data
Create an NC machining program from a 3D model.
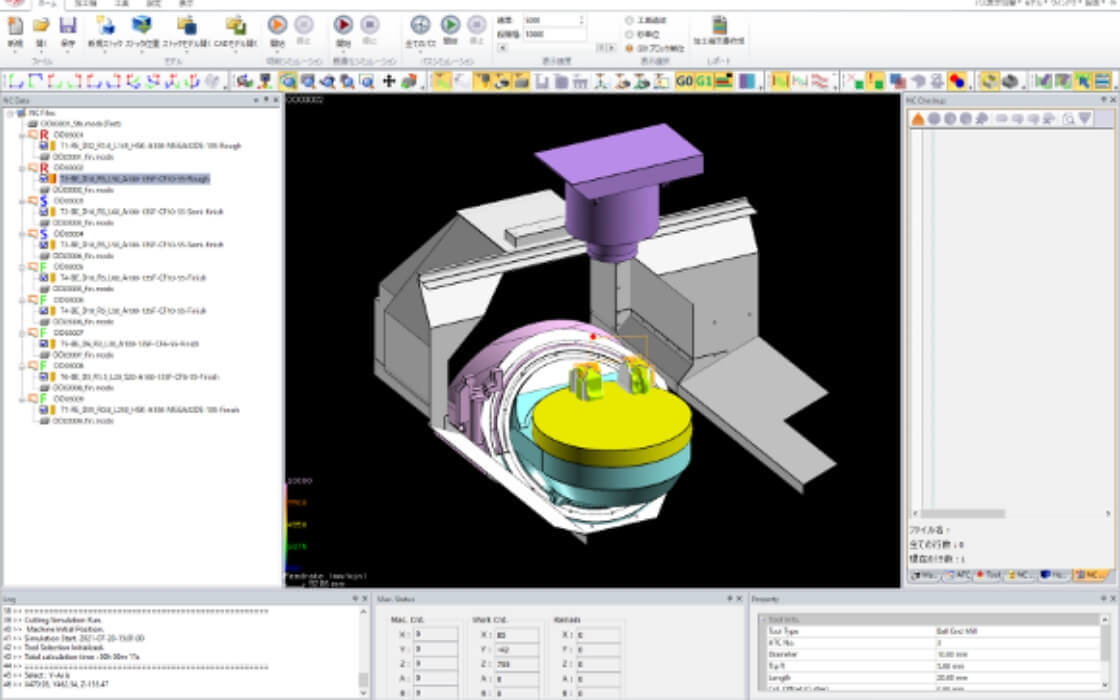
STEP3
Machining
Make full use of our processing machines to perform high-speed, high-precision processing.
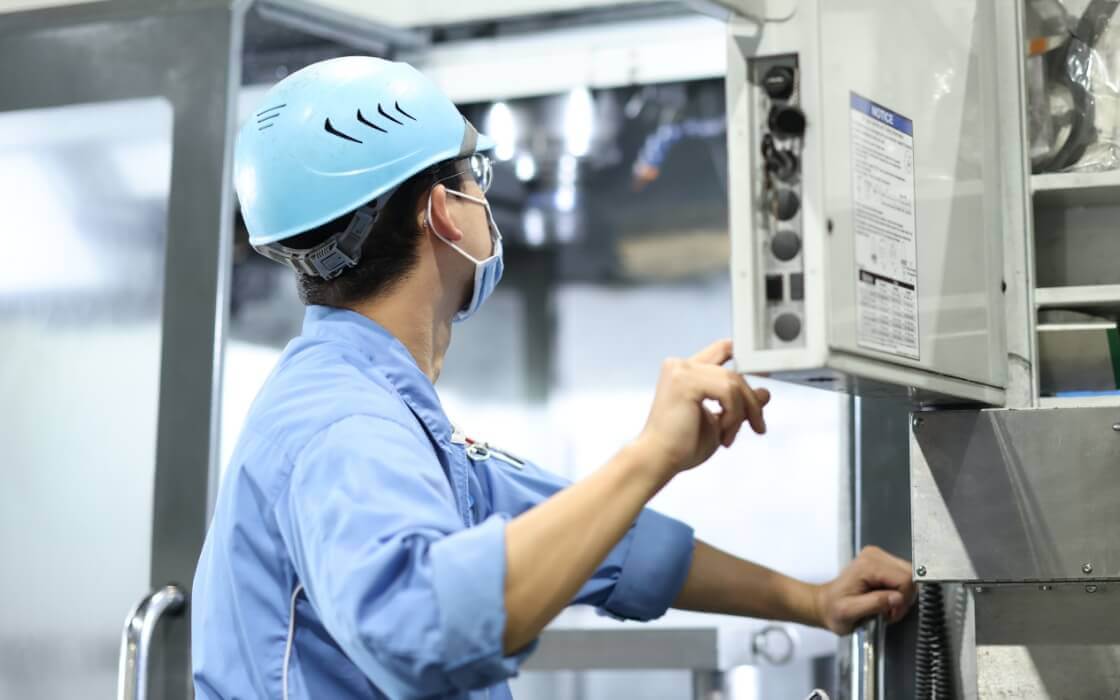
STEP4
Finishing and Assembling
Parts that have been processed and inspected are manually assembled into one metallic pattern.
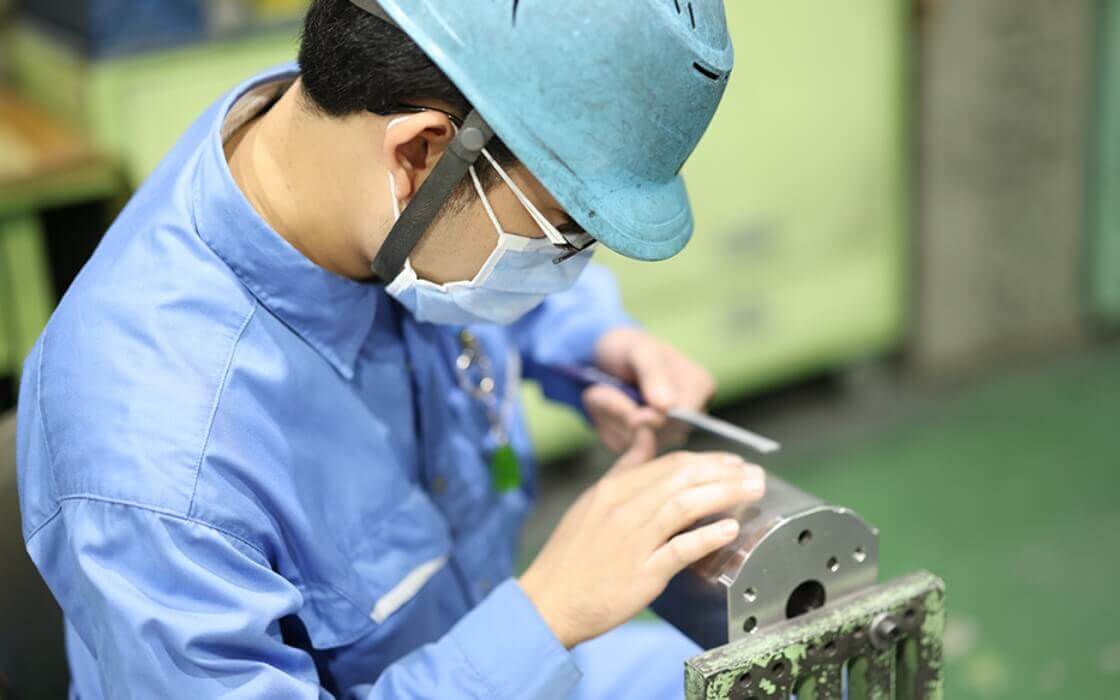
STEP5
Inspection
We guarantee high-precision dimensions by using contact-type and non-contact-type measuring machines properly.
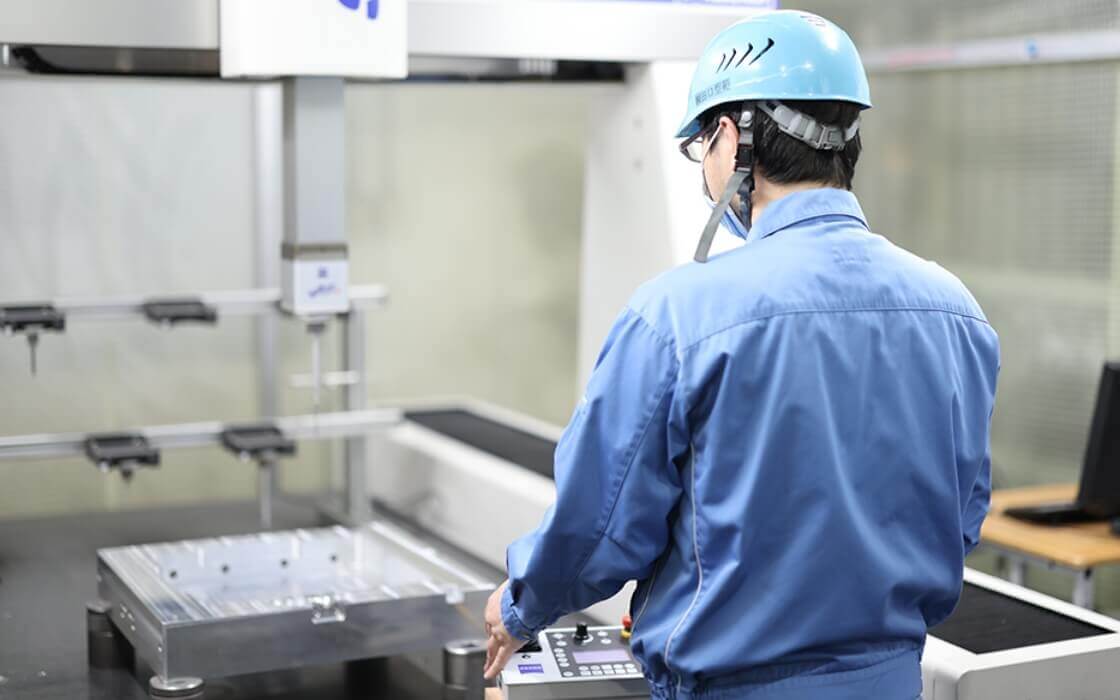
STEP6
Delivery
Deliver our products safely and reliably by our own truck service.
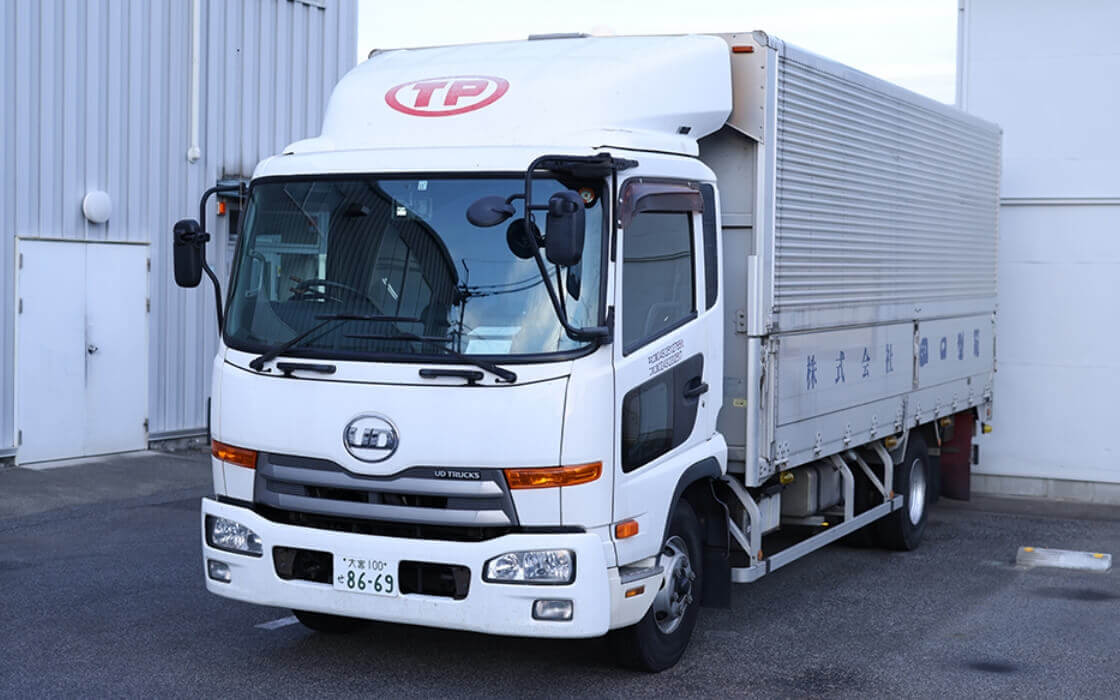
Prototype Castings
We run the whole following production process in our facilities. Designing / Molding / Casting (outsourcing) / Finishing / Machining / Inspection.
With the solidification analysis, casting defects can be eliminated and we provide our prototype castings in a short period of time. Furthermore, we own a sand 3D printer produced by ExOne thus we are able to produce castings with quick turnaround without wooden patterns.
STEP1
Designing Patterns
Create casting plan such as runners required for casting. Develop into a sand mold. Confirm that there is no problem in fluidity and solidification analysis(CAE).
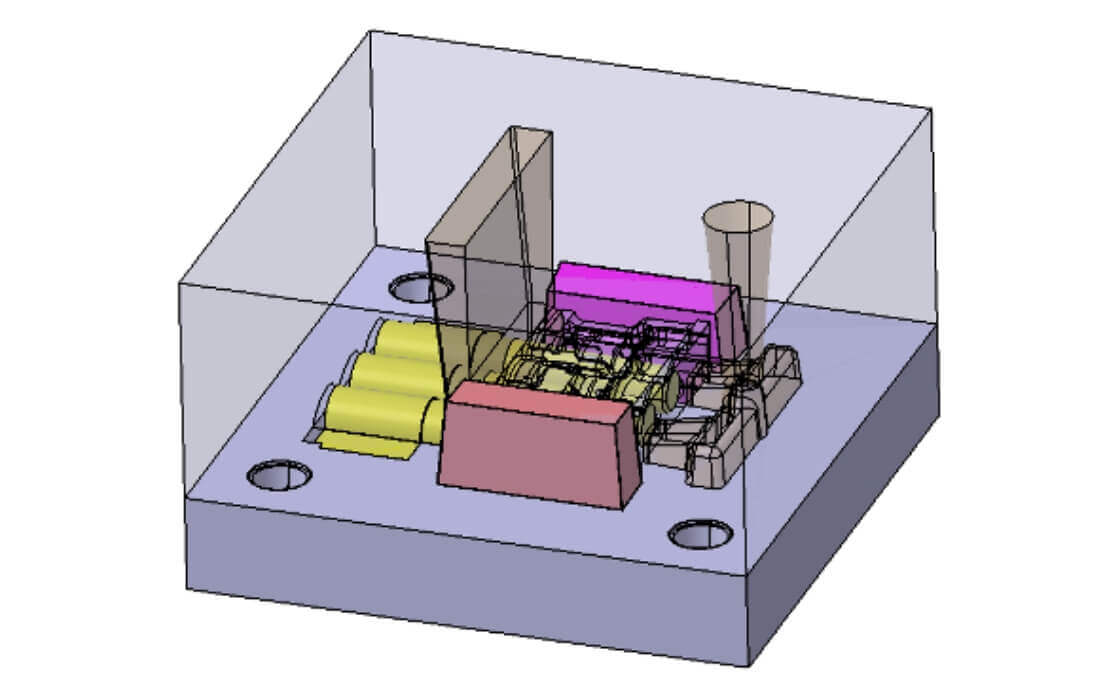
STEP2
Making Patterns
Make patterns for sand molds.
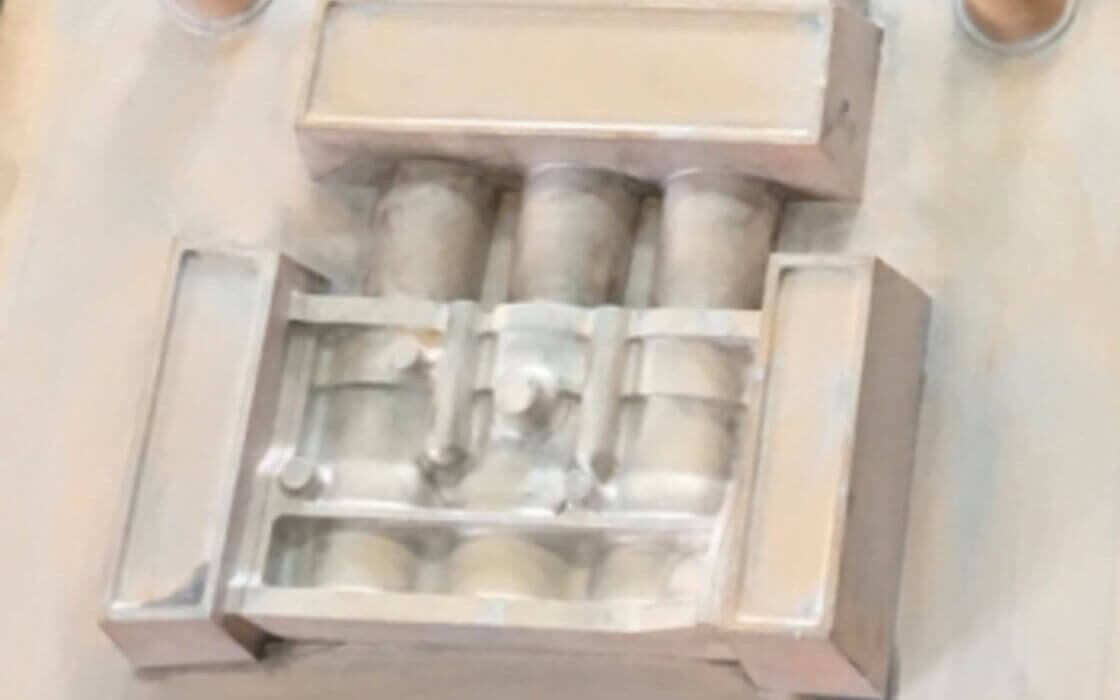
STEP3
Casting
Assemble the sand molds and pour the molten metal. When it gets cold, take it out from the sand mold and remove the excessive portions.
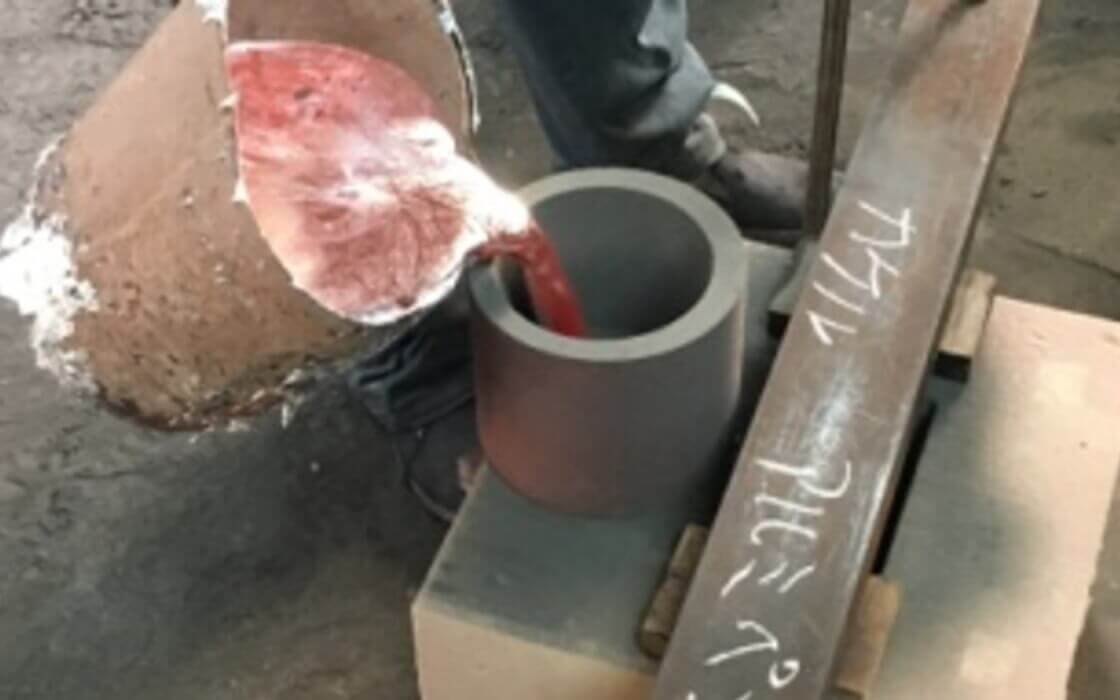
STEP4
Inspection
Visualize and evaluate the difference between the 3D CAD data and the casting by using 3D scanning.
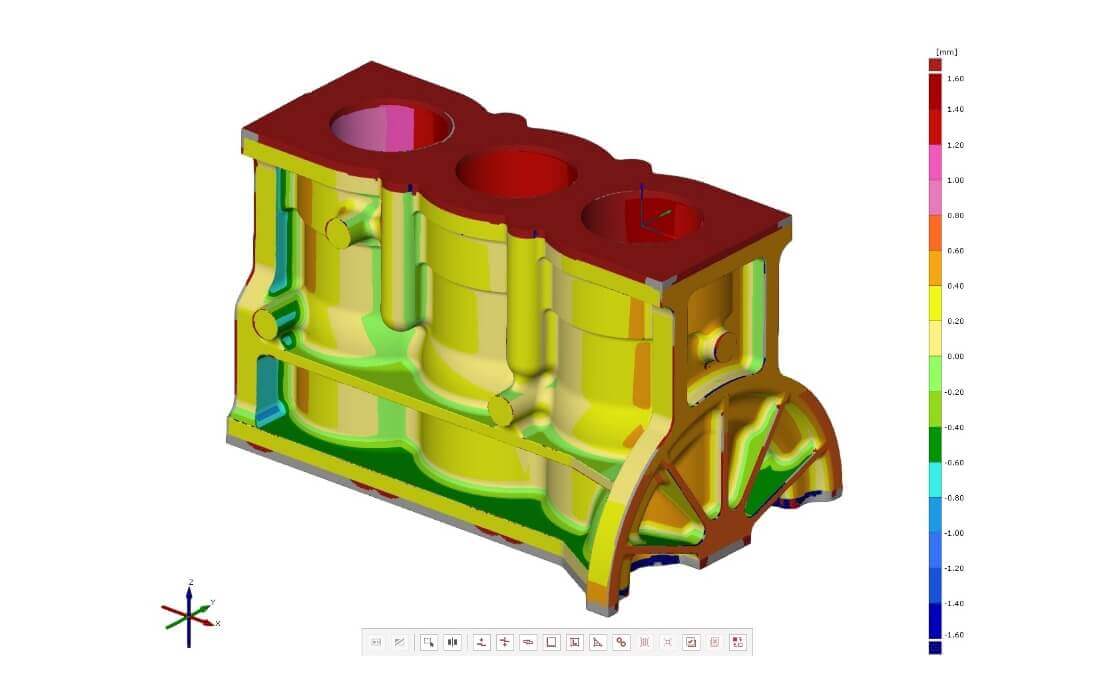
STEP5
Processing
Machining according to the design dimension.
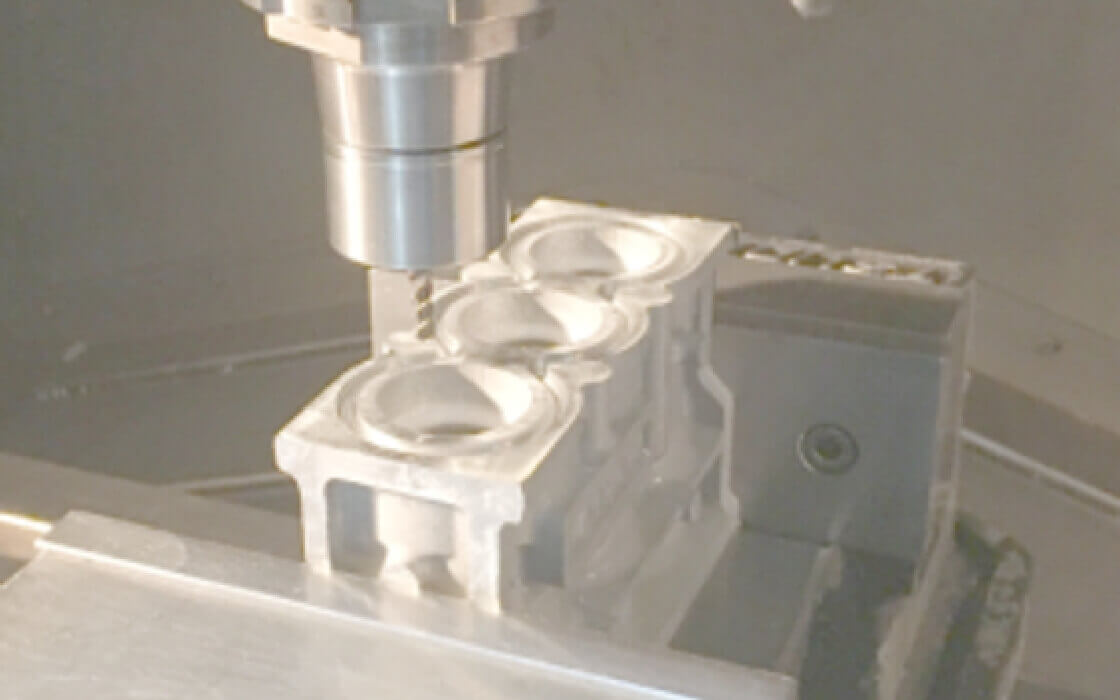
STEP6
Inspection
Inspect with a measuring machine whether the processing dimensions are within the tolerance of the drawing, etc.
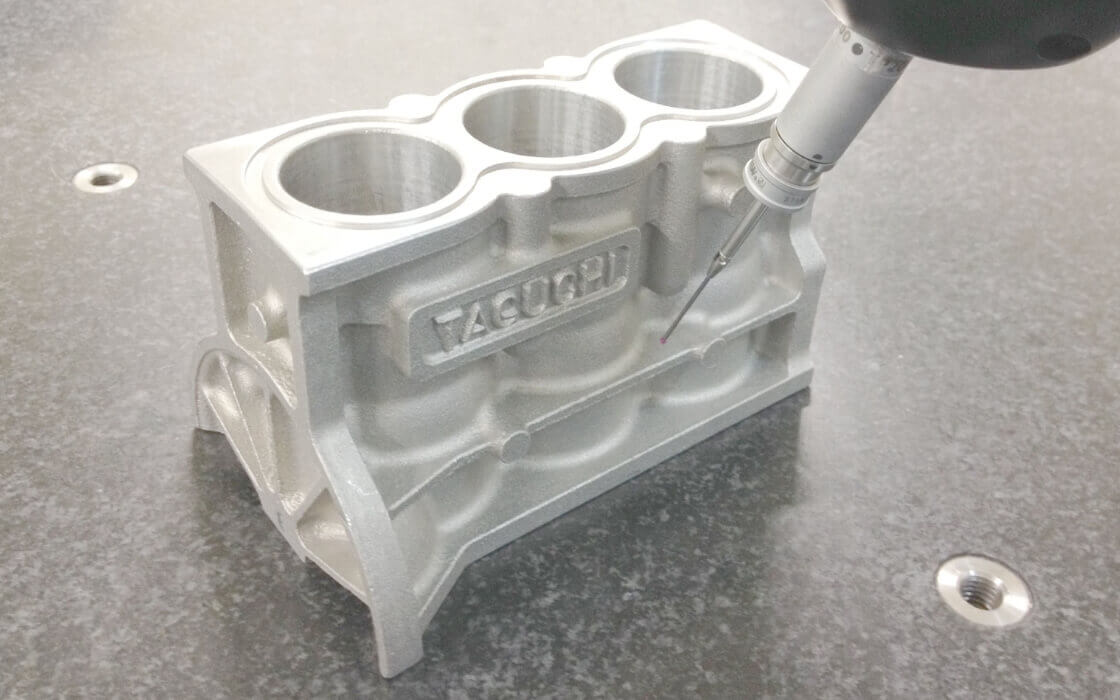
Wooden Patterns and Core Boxes
We make wooden patterns that are in line with the needs of our customers by the combination of the traditional manual technique which we have cultivated over 70 years since we were founded and the latest technology. We use tools such as chisel and plane as well as 3D CAD/CAM/CAE and digital technical skills at machining centers.
Our achievements: Cylinder head, Cylinder blocks, Transmission cases, EV motor cases, Medium and large subframe, etc.
STEP1
Designing Patterns
Create casting plan such as runners required for casting. Develop into a sand mold. Confirm that there is no problem in fluidity and solidification analysis(CAE).
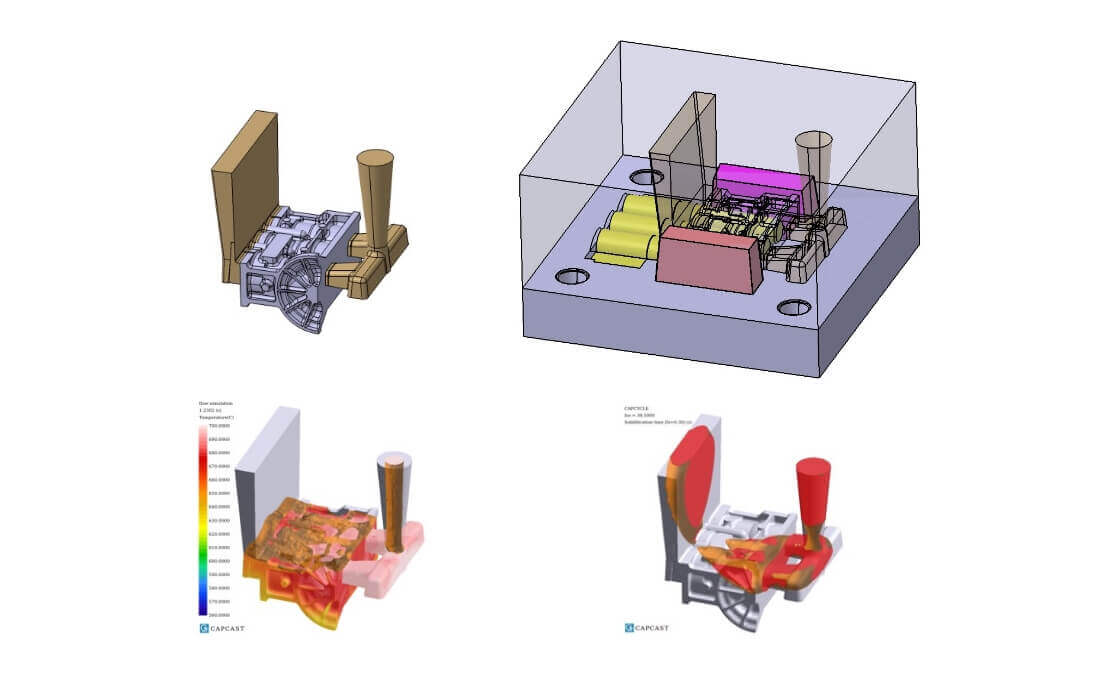
STEP2
Creating Processing Data
Create an NC machining program from a 3D model.
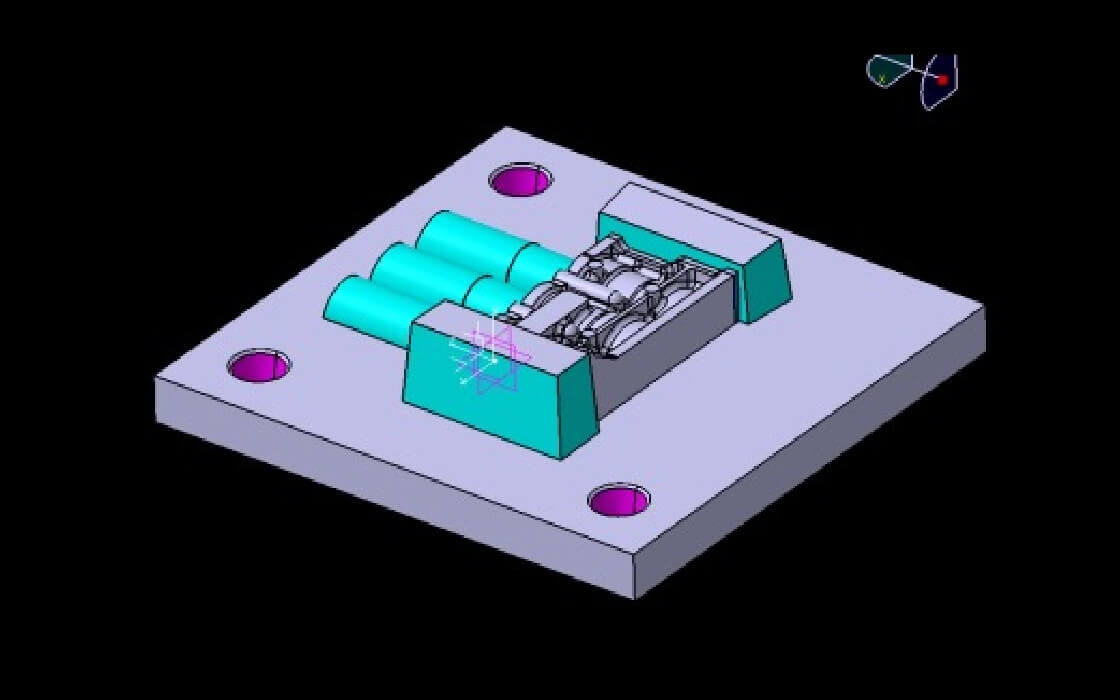
STEP3
Machining
Process with an NC machine.
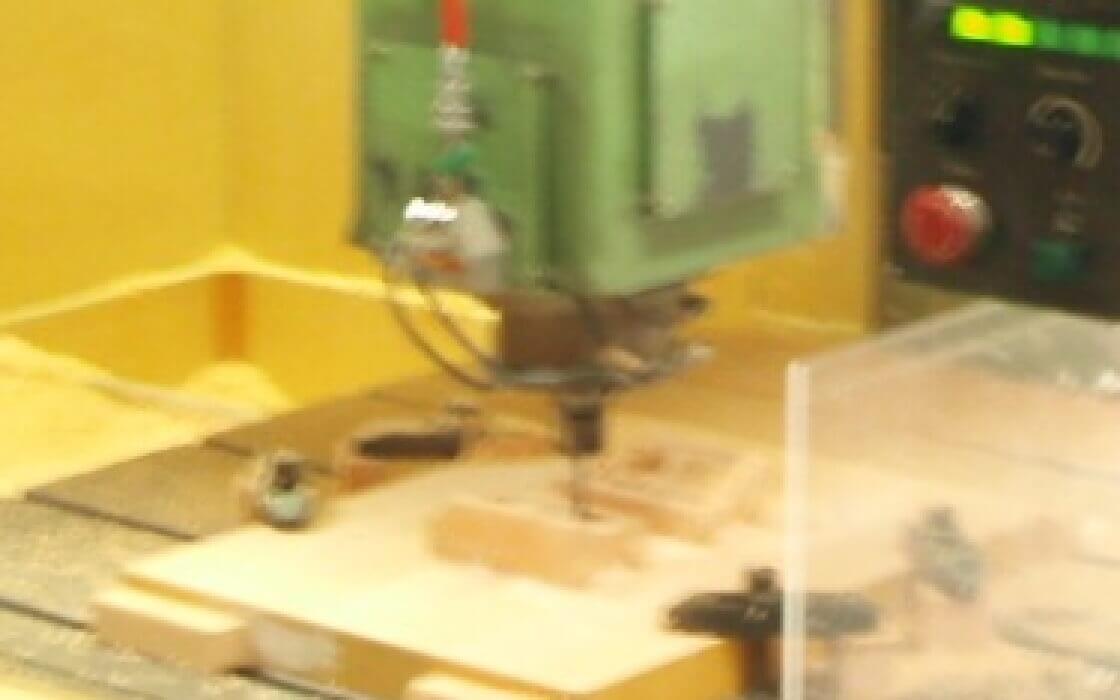
STEP4
Finishing and Assembling
Add a frame, runners, risers etc.
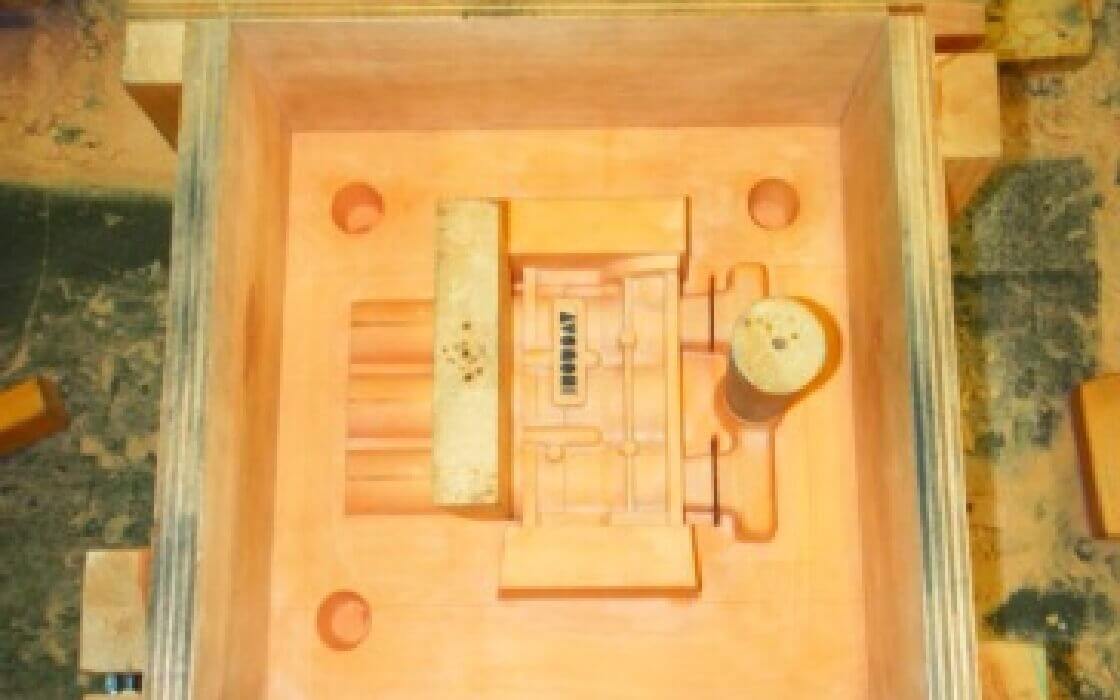
STEP5
Inspection
Visualize and evaluate the difference between 3D CAD data and the wooden pattern using 3D scanning measuring devices.
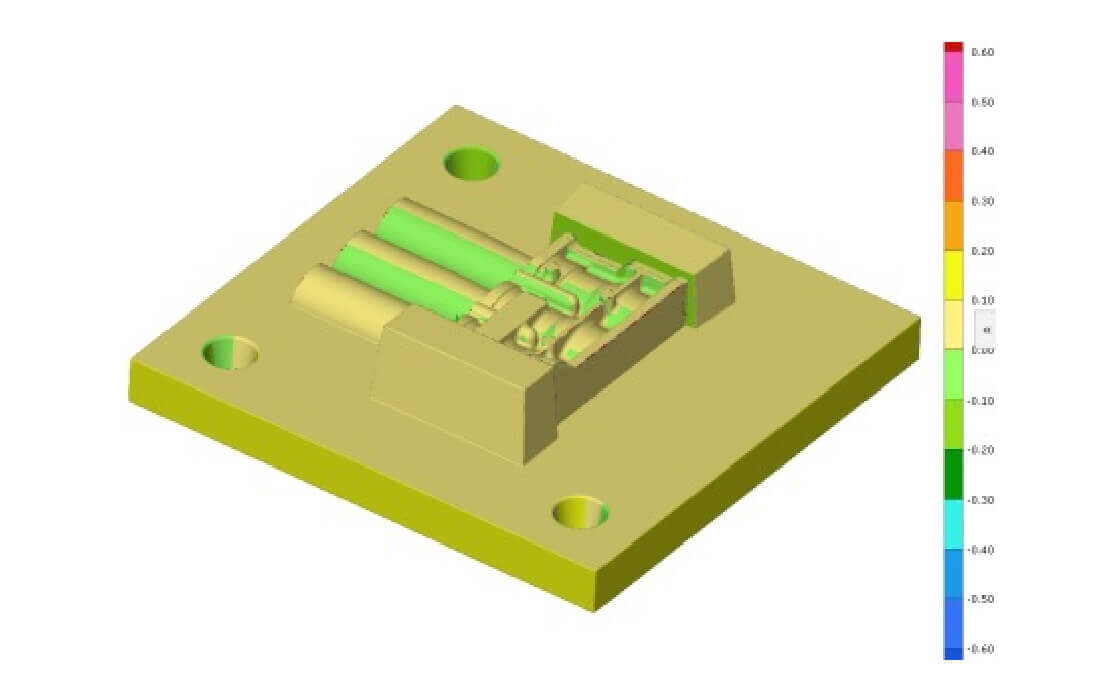
Metallic Patterns and Core Boxes
Our achievements: Metallic patterns for mass production of sand castings, Lost-wax patterns for gas turbines, Metallic patterns for low pressure die-casting, Metallic patterns for gravity die casting, etc.
We are able to make high quality metallic patterns in a short period of time by using 3D design and the latest 5-axis MC.
We have a non-contact 3D measuring machine (ATOS) and a contact type coordinate Measuring Machine to support and guarantee our inspection.
STEP1
Designing Patterns
We design 3D models by using 2D / 3D properly according to customer needs. If necessary, we also analyze the temperature distribution of the metallic pattern.
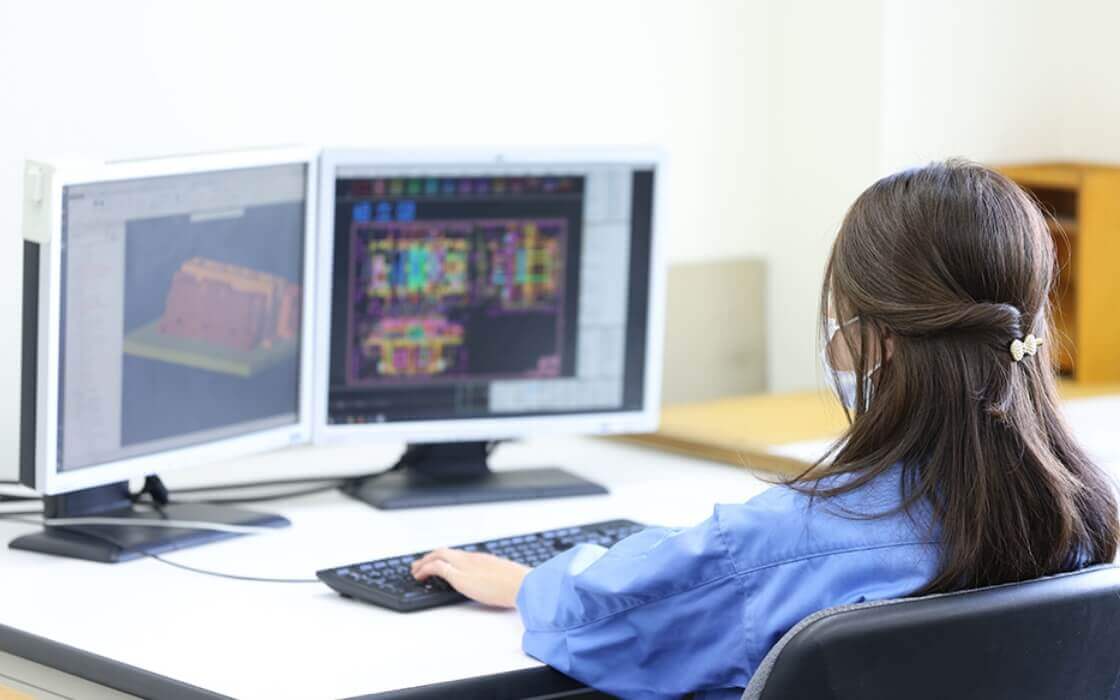
STEP2
Creating Processing Data
Create an NC machining program from a 3D model.
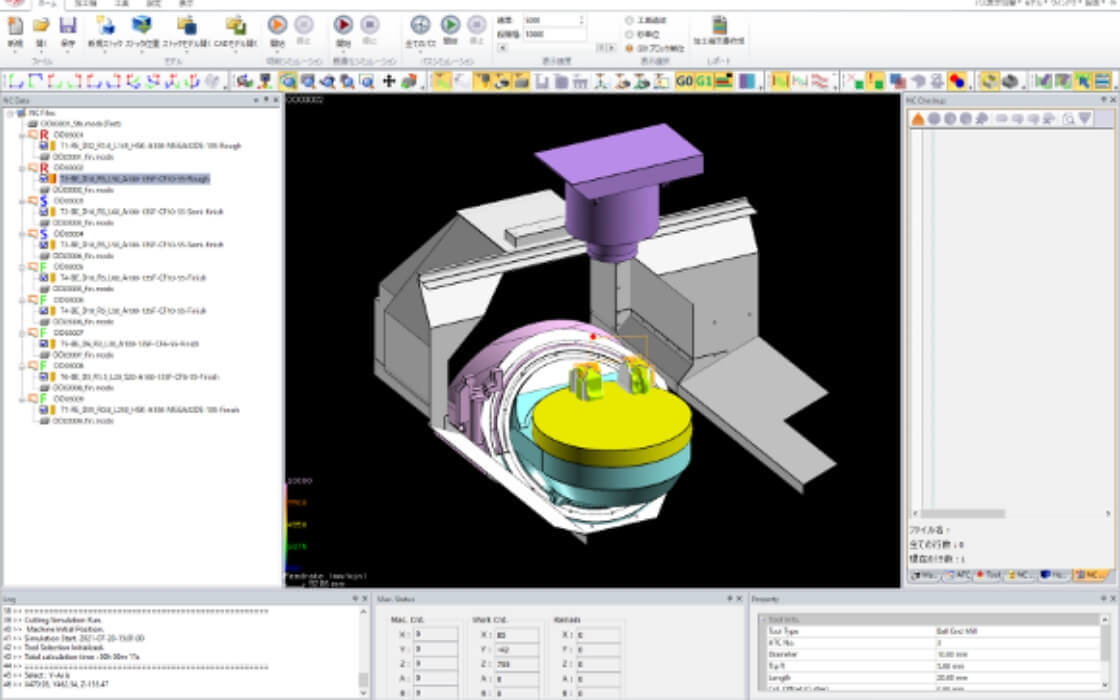
STEP3
Machining
Make full use of our processing machines to perform high-speed, high-precision processing.
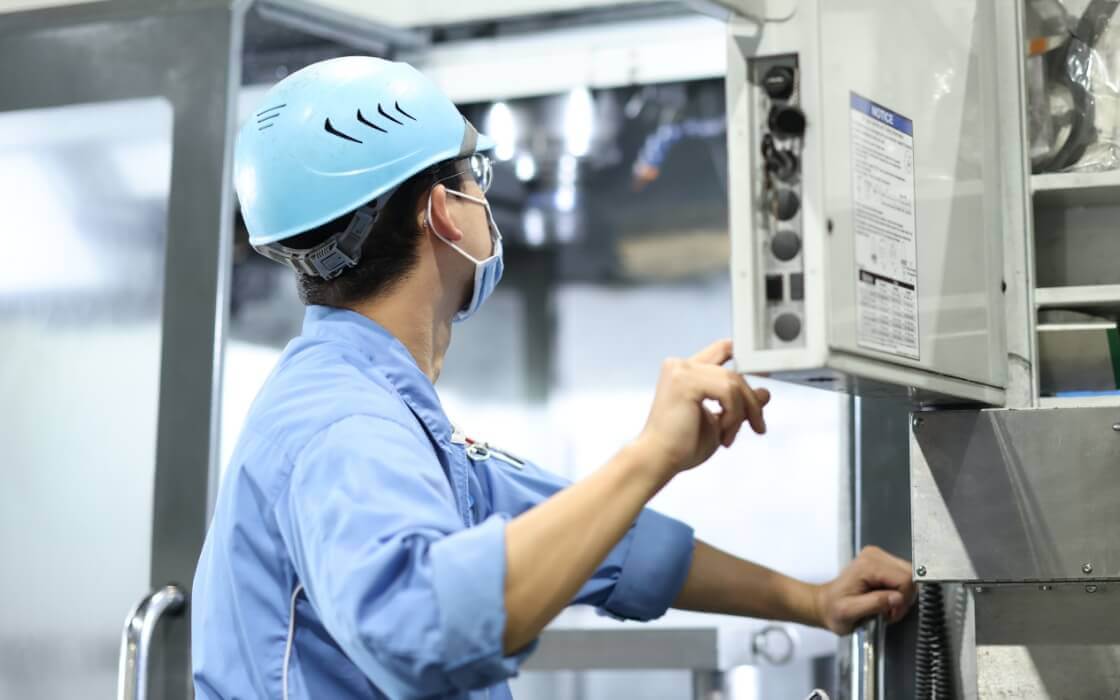
STEP4
Finishing and Assembling
Parts that have been processed and inspected are manually assembled into one metallic pattern.
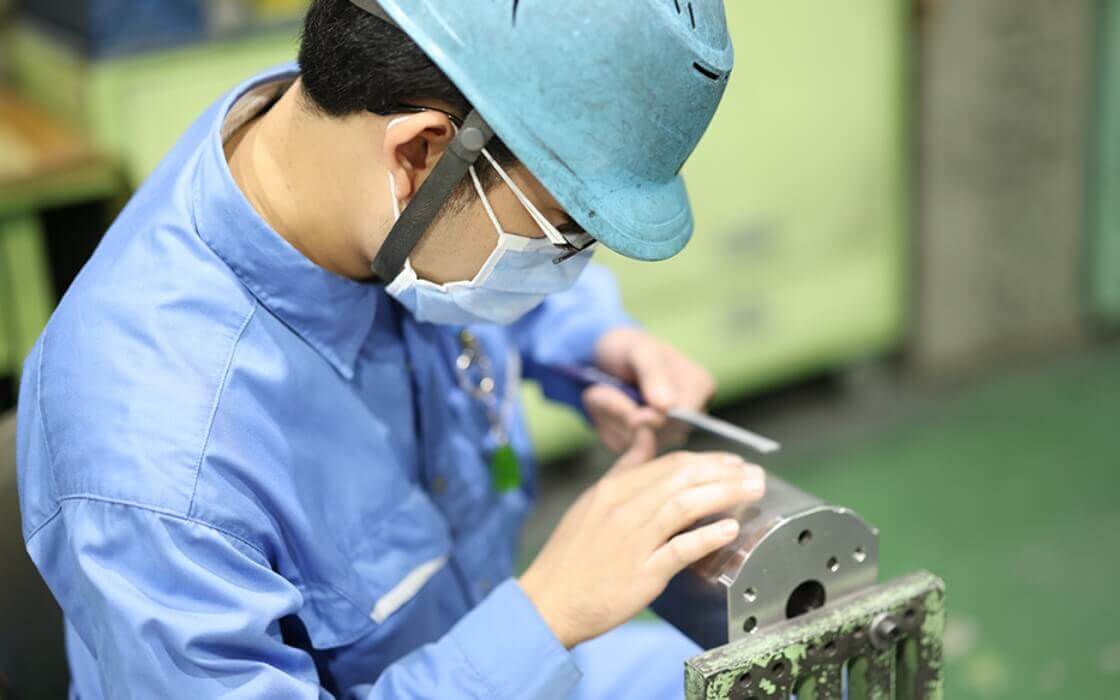
STEP5
Inspection
We guarantee high-precision dimensions by using contact-type and non-contact-type measuring machines properly.
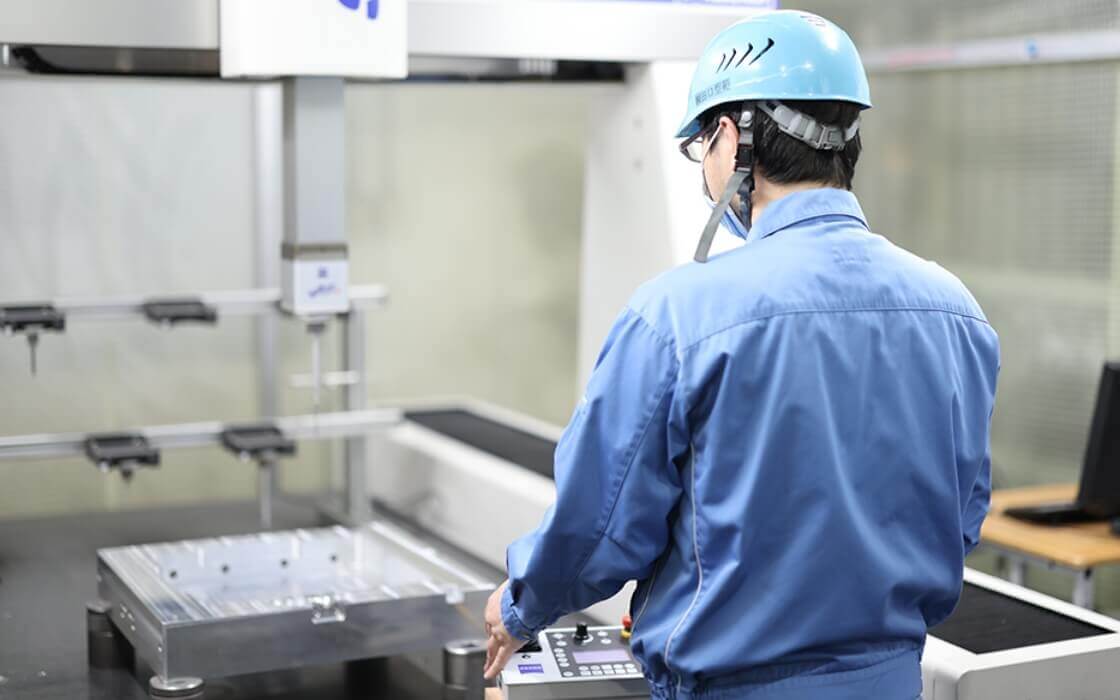
STEP6
Delivery
Deliver our products safely and reliably by our own truck service.
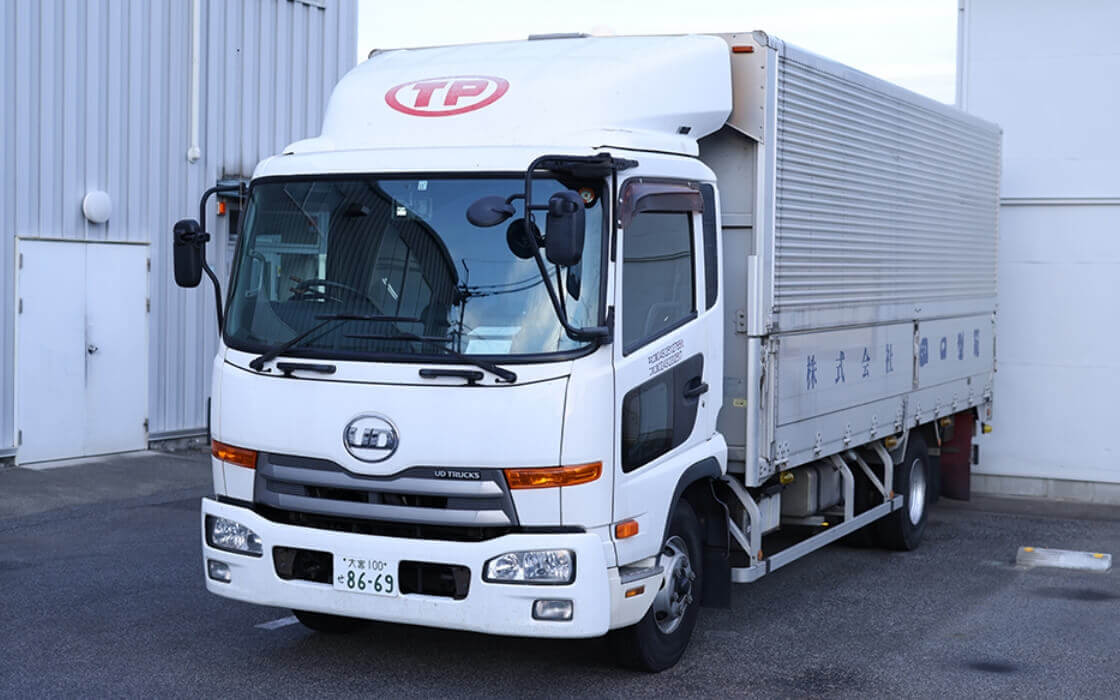
Prototype Castings
We run the whole following production process in our facilities. Designing / Molding / Casting (outsourcing) / Finishing / Machining / Inspection.
With the solidification analysis, casting defects can be eliminated and we provide our prototype castings in a short period of time. Furthermore, we own a sand 3D printer produced by ExOne thus we are able to produce castings with quick turnaround without wooden patterns.
STEP1
Designing Patterns
Create casting plan such as runners required for casting. Develop into a sand mold. Confirm that there is no problem in fluidity and solidification analysis(CAE).
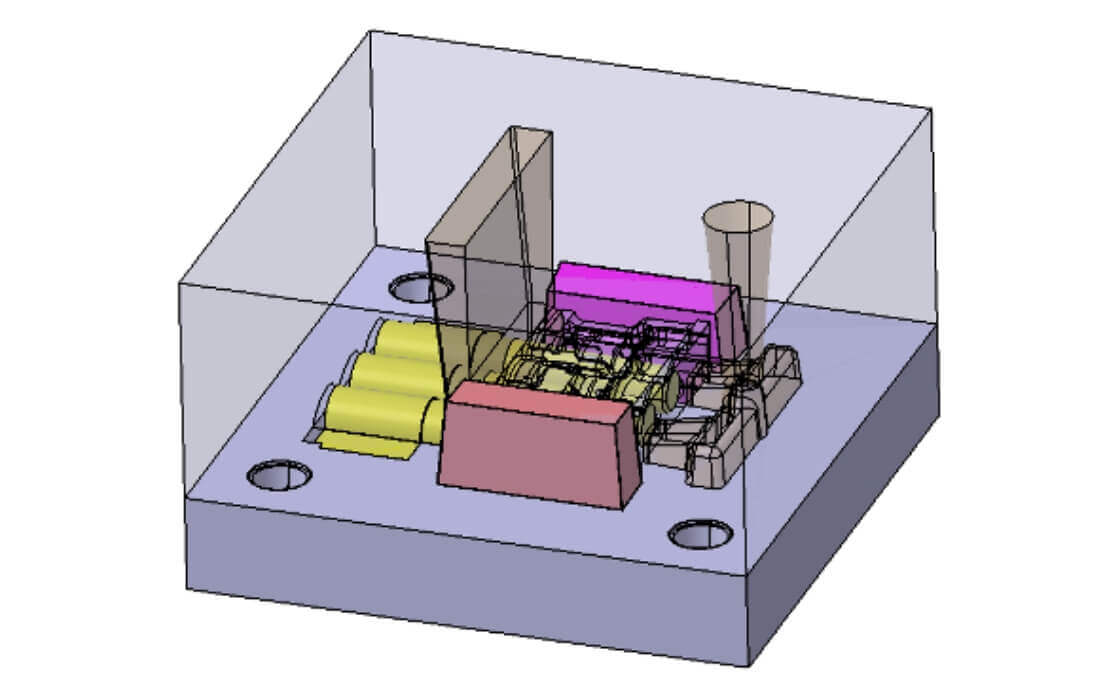
STEP2
Making Patterns
Make patterns for sand molds.
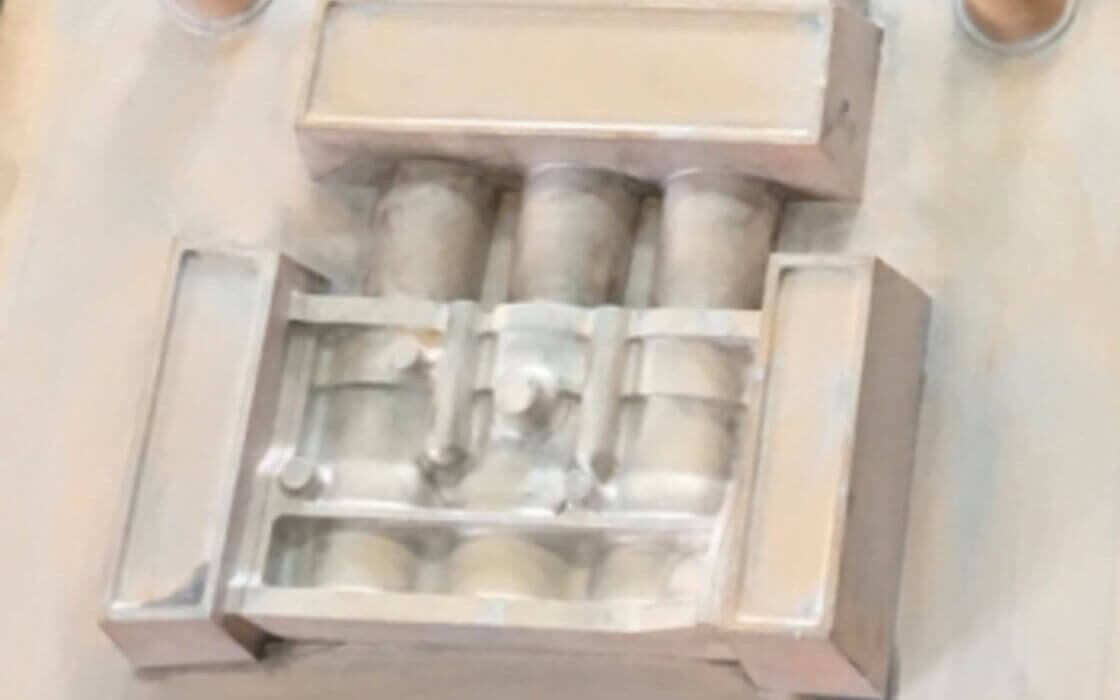
STEP3
Casting
Assemble the sand molds and pour the molten metal. When it gets cold, take it out from the sand mold and remove the excessive portions.
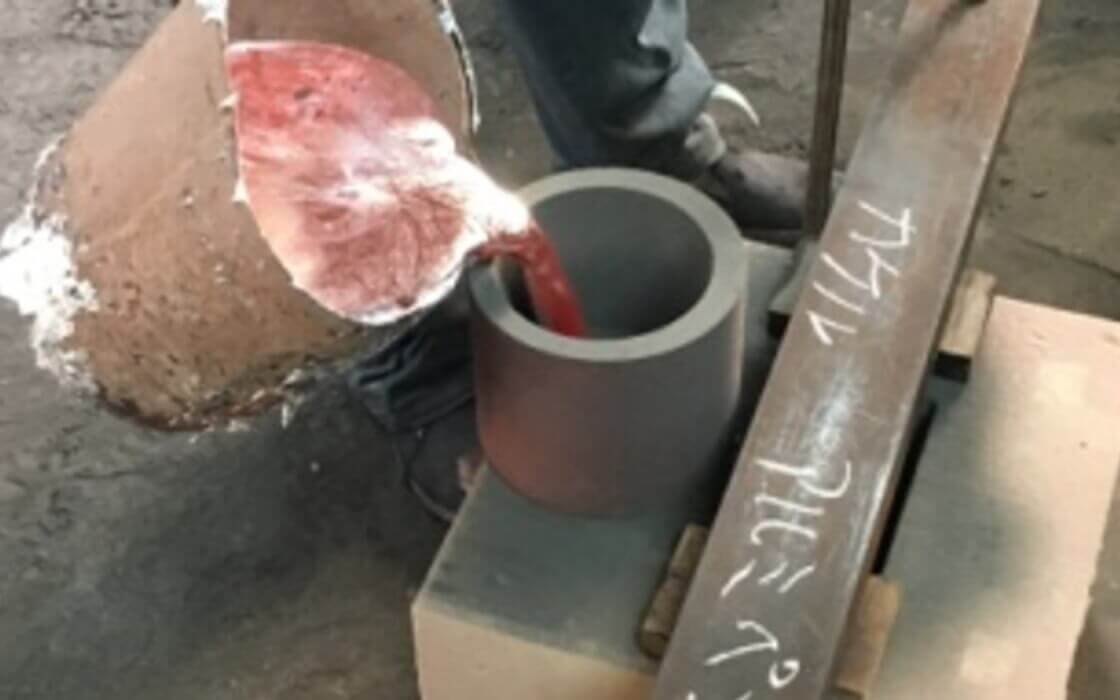
STEP4
Inspection
Visualize and evaluate the difference between the 3D CAD data and the casting by using 3D scanning.
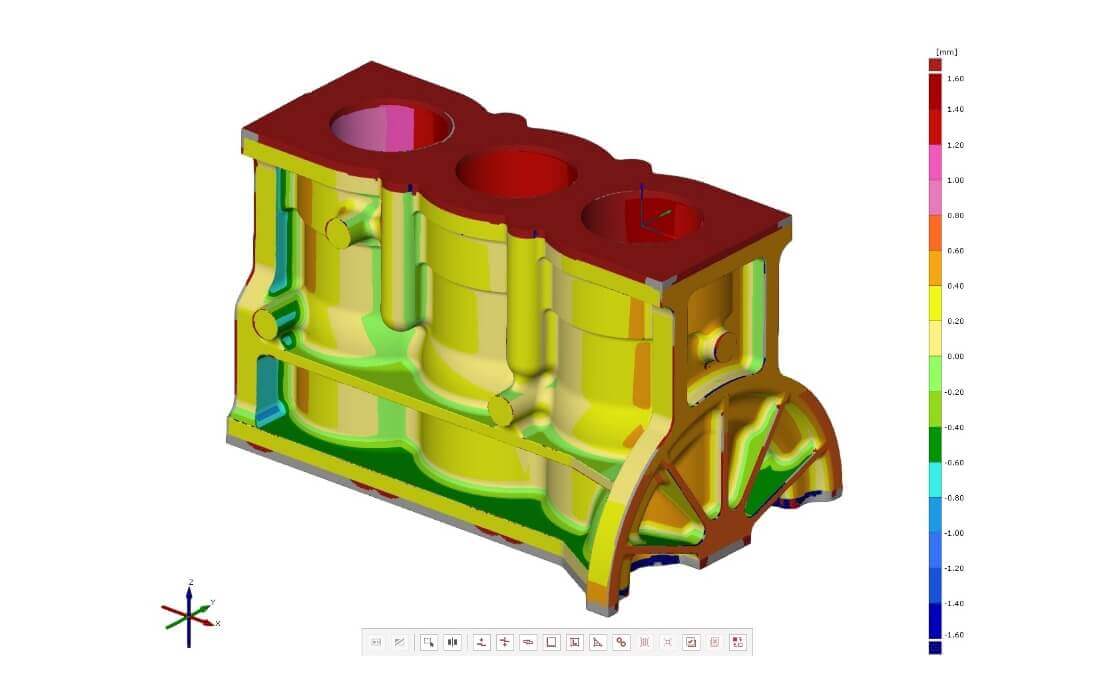
STEP5
Processing
Machining according to the design dimension.
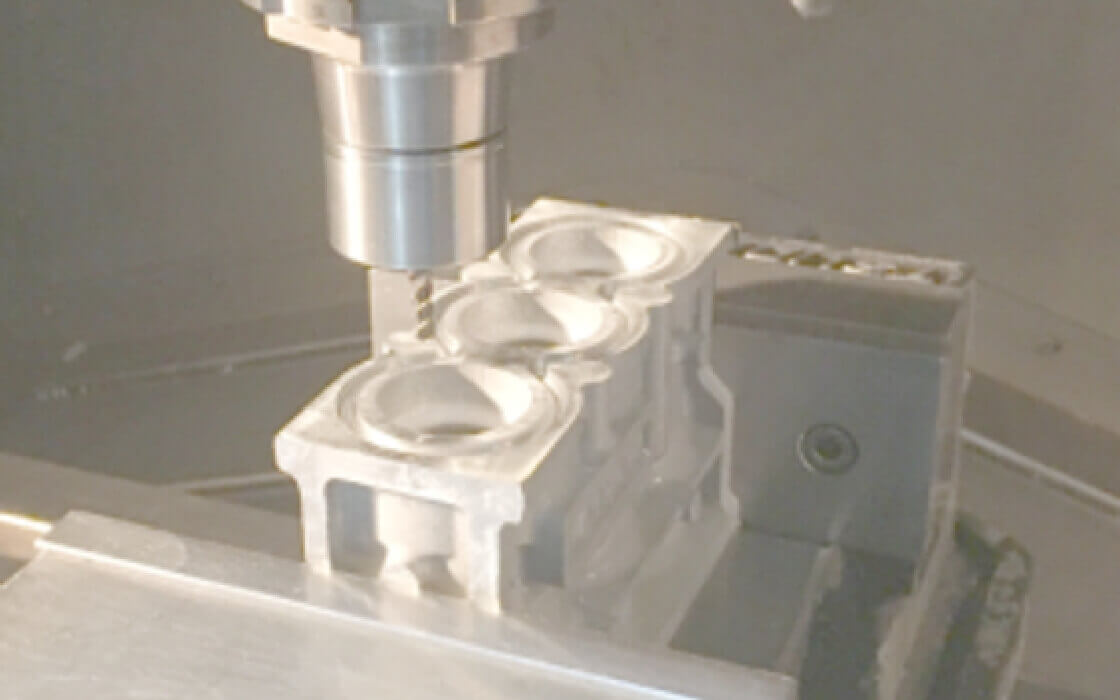
STEP6
Inspection
Inspect with a measuring machine whether the processing dimensions are within the tolerance of the drawing, etc.
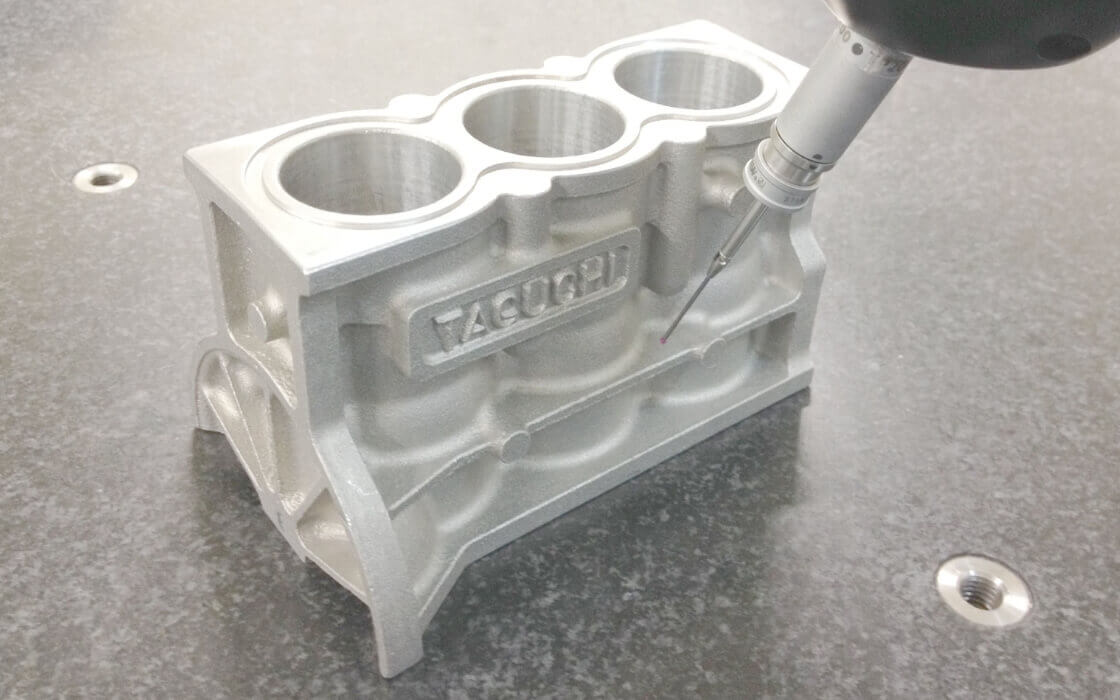
Impeller
Making full use of a simultaneous 5-axis MC introduced in the 1980s, we deal with a wide range of products from prototype model to mass product of aluminum, titanium, magnesium, nickel alloys, etc. We provide the high accuracy 3D measuring and the dynamic balance measurment.
Also, we are proud of our original blended machinable wax for lost wax precision casting that can be used for turbine wheel.
STEP1
Modeling / Creating machining programs
We create modeling data for impeller and machining program for blades from the coordinates provided by the customer.
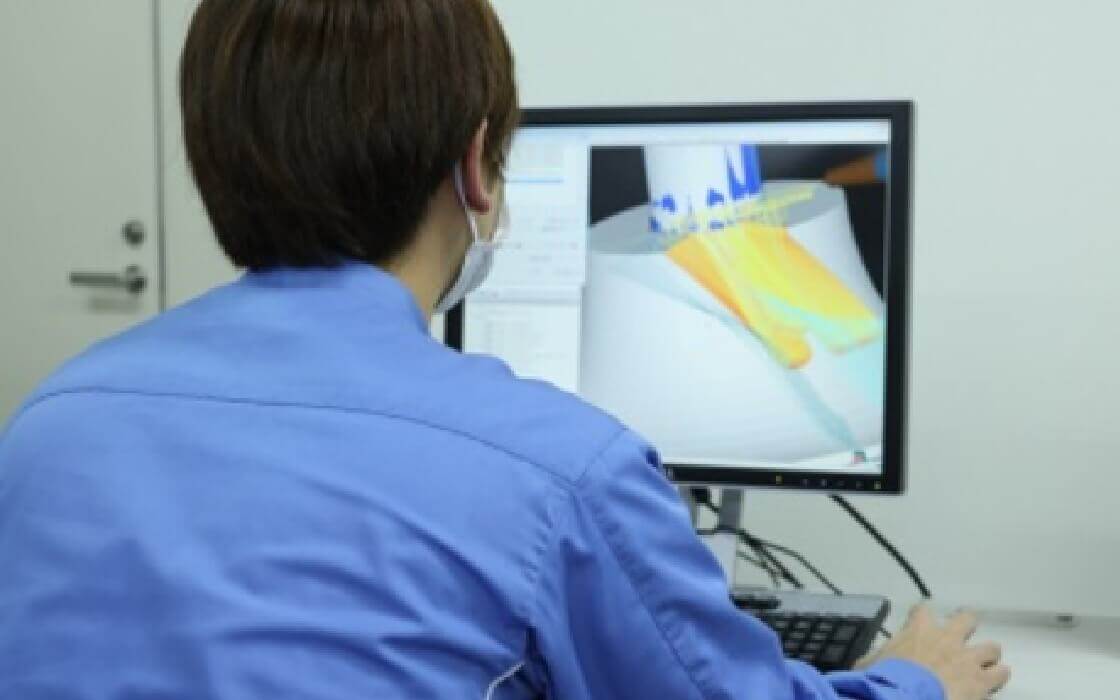
STEP2
NC Lathe Processing
Process Lathes
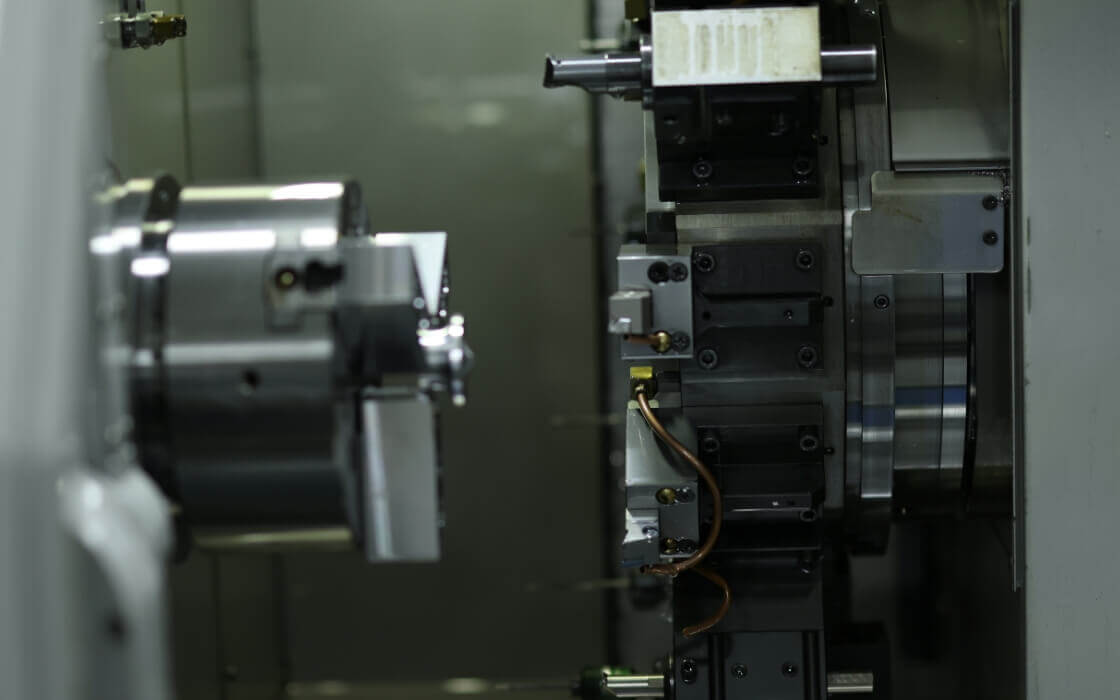
STEP3
Five-axis machining
Process Blades
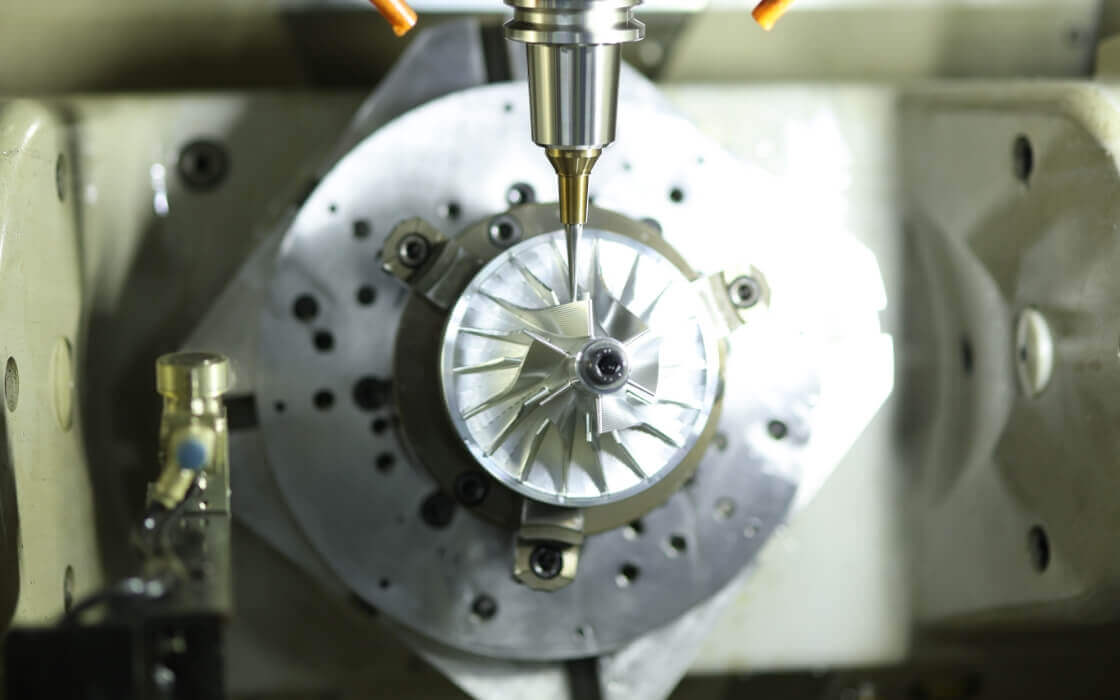
STEP4
3D measurement (contact type)
Inspect the products
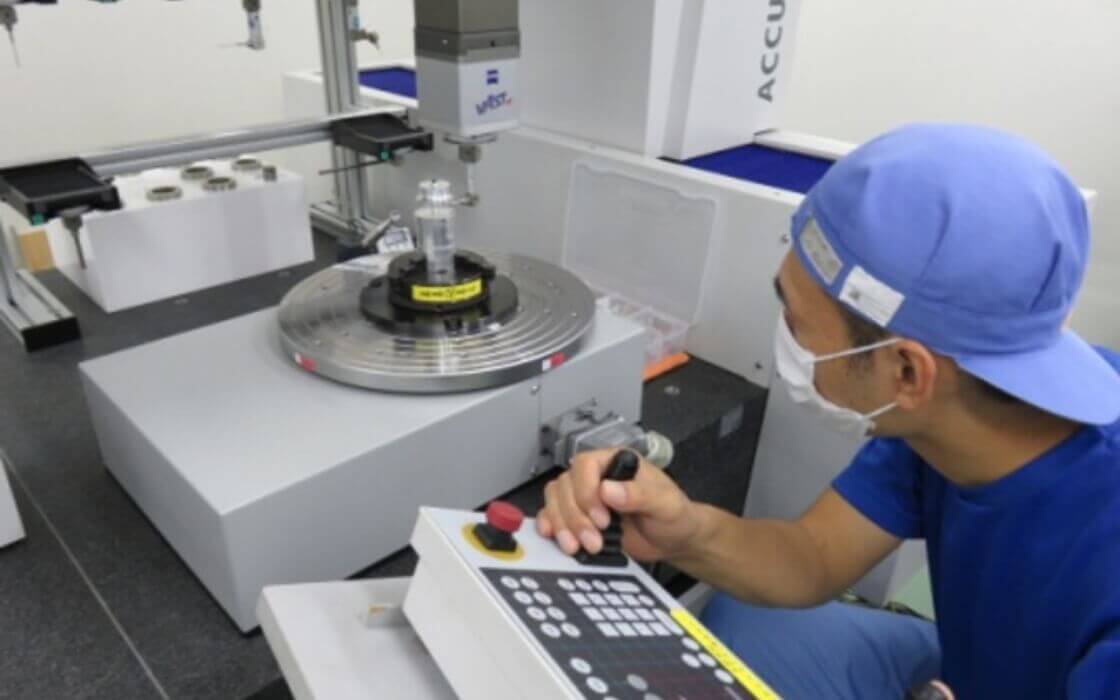
STEP5
Balancing Measurement and Modification
Modify the balance.
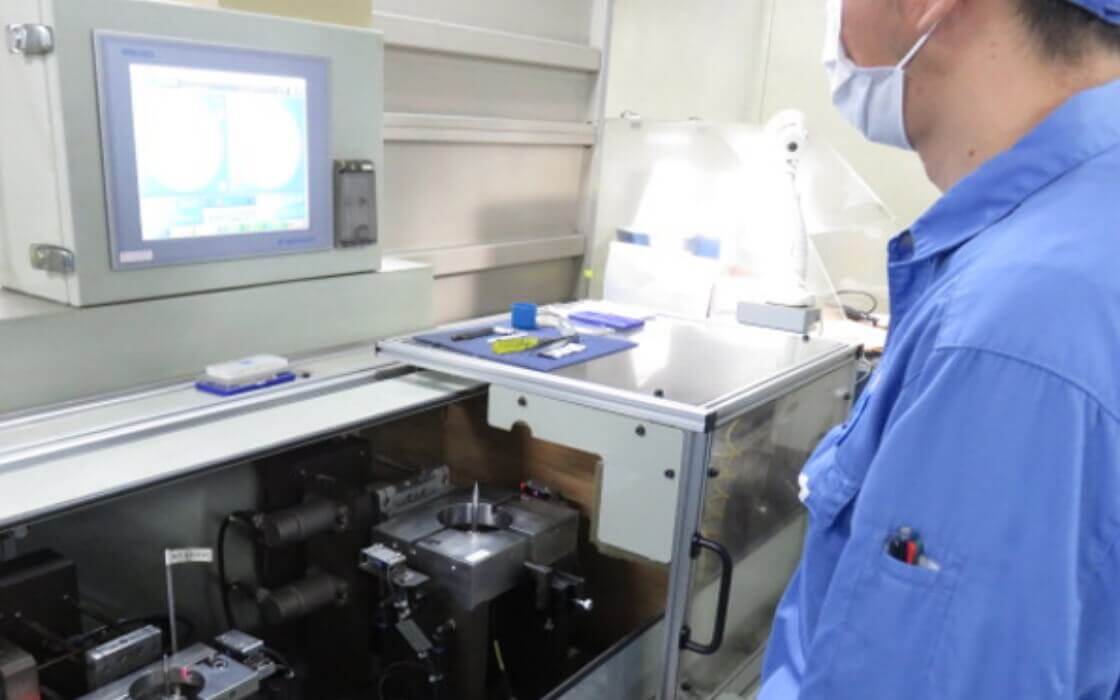