Our Expertise
- Wooden Patterns and Core Boxes
- Metallic Patterns and Core Boxes
- Impellers
- Prototype Castings
- Processed Products
Wooden Patterns and Core Boxes
Wooden Joinery – Technology to prevent dimensional changes in wood
A resin pattern can be manufactured with less than half the weight by using wood. However, dimensional changes may occur. We solve the problem by how we put wooden parts together.
- ・Wood does not shrink in the direction in which the fiber grows, but shrinks in the direction in which the fiber cross at right angles.
Wooden joinery is a technique that considers the direction of the fibers and position wooden parts so as to resist the shrinkage of the wood in order to prevent dimensional changes. - ・In case that the pattern is likely to break, such as an elongated shape, wooden parts should be arranged in the direction in which the fiber can give strength.
- ・In order to improve the useful life and to prevent splinters due to aging, wooden parts are placed considering the angle of the fibers with respect to the shape.
After making the material of the wooden frame, the wooden pattern is made by machining.
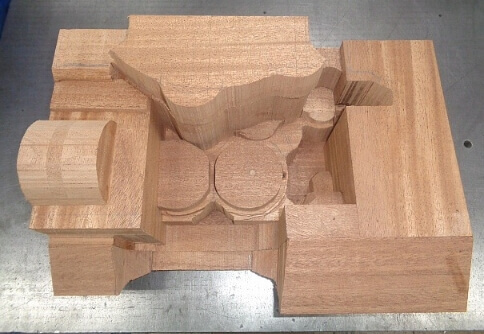
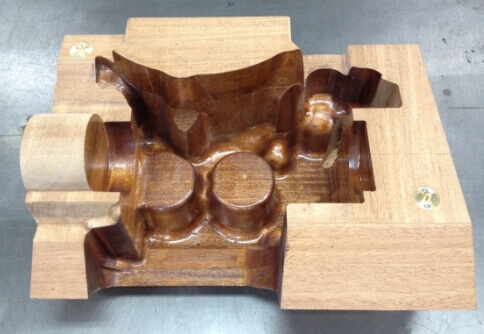
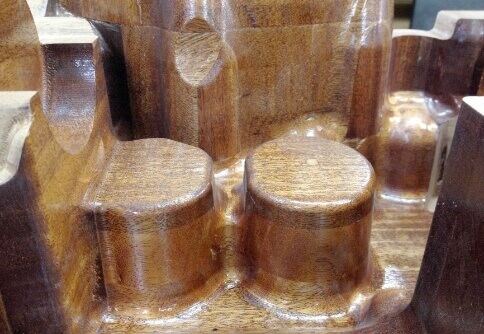
Metallic Patterns and Core Boxes
Reverse Modeling (Reverse Engineering)
We measure a pattern without any drawings or data with a non-contact measuring machine (ATOS) and we make it possible for you to have a surface and/or solid model with the measured data.
As long as the shape of the pattern can be measured with a non-contact measuring machine (ATOS), it can be converted into CAD data.
Achievements:
- ・Remanufacturing metallic patterns and/or parts without CAD data.
- ・Digitalizing hand-made prototype into CAD data.
- ・Digitalizing forms that you added molding allowance into CAD data.
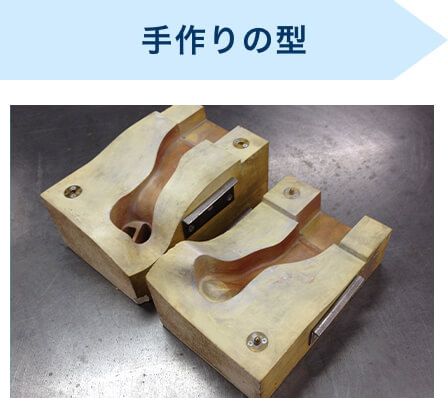
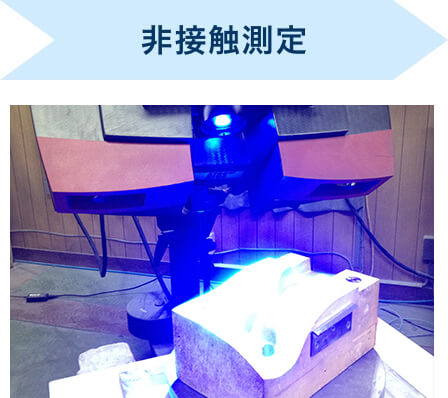
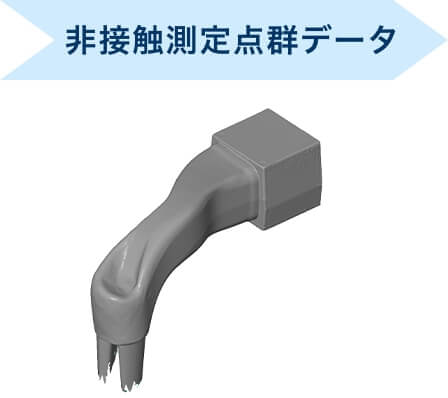
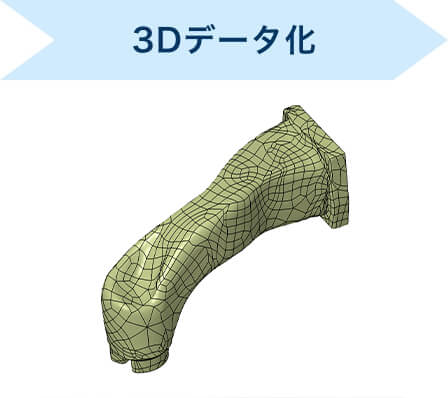
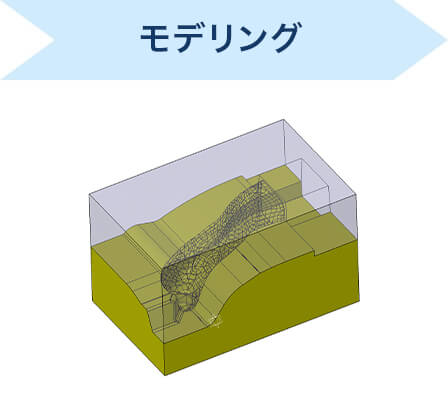
Simultaneous 5-axis Machining
- ・Compared to the work with 3-axis, we are able to process a deeper shape with an excellent machined surface.
- ・Multi-face machining and High-precision processing are available with one setup.
- ・We handle large shapes as Φ1000.
- ・We manage to perform 5-axis machining and turning at the same time so we are able to shorten the machining time thus the delivery time is shortened as well.
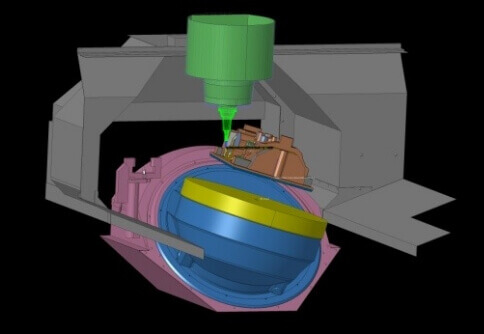
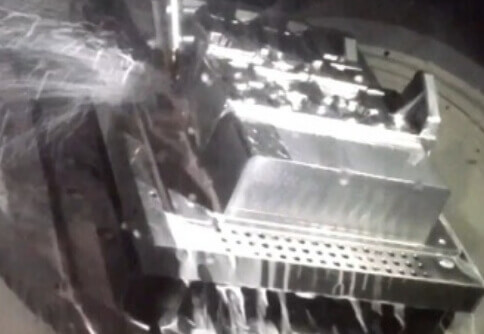
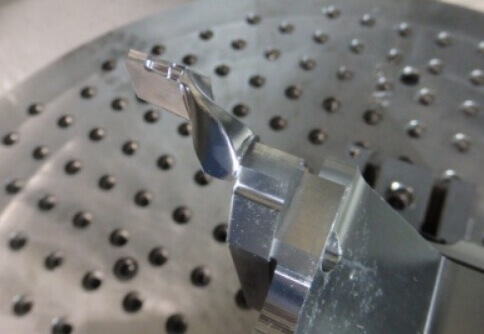
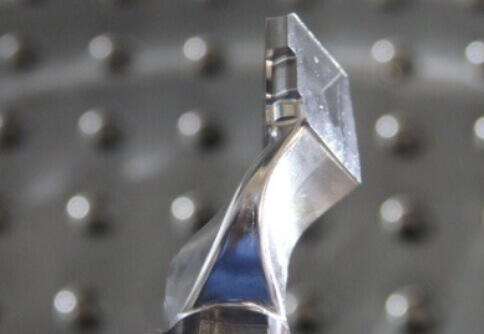
3D Designing
- ・We digitalize our expertise into 3D then design products.
- ・Multiple engineers design products simultaneously.
- ・We make good use of 3D-CAD to design products accurately and quickly.
- ・We use 3D design for simulation and analysis before making a metallic pattern.
- ・We perform shape inspection and assembly inspection using a non-contact 3D measuring machine (ATOS).
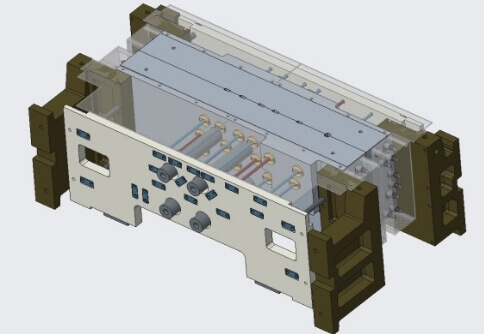
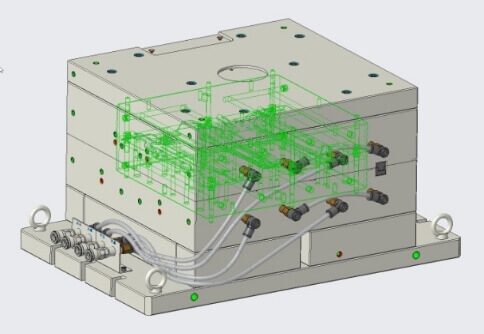
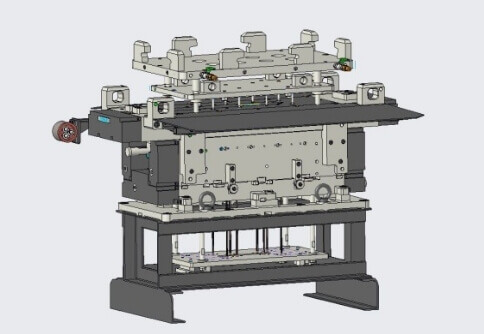
Metallic Patterns Temperature Distribution Analysis
In order to eliminate uneven burning of the core and deformation of the metallic pattern, we verify the appropriate heater arrangement at the time of design. We set the actual molding conditions and perform analysis.
Molding conditions:
- ・Preset temperature
- ・Cycle time -sand blowing, burning, taking out, air blow, etc.
We make a pass/fail judgement by looking at the changes in the colormap as time proceeds. When the design is properly done, the color in the colormap tend to be unified.

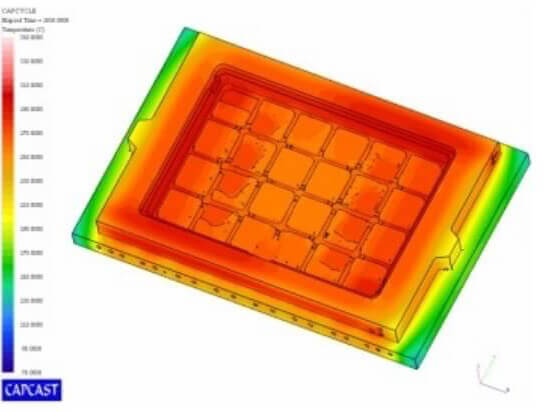
Core Deformation Analysis
Based on the chucking seat of the core, we predict spots where get stressed at the time of removal from the molding machine or of transportation and we comprehend the problems on strength in advance. Based on the result, we enhance strength of the core and also propose the shell thickness.
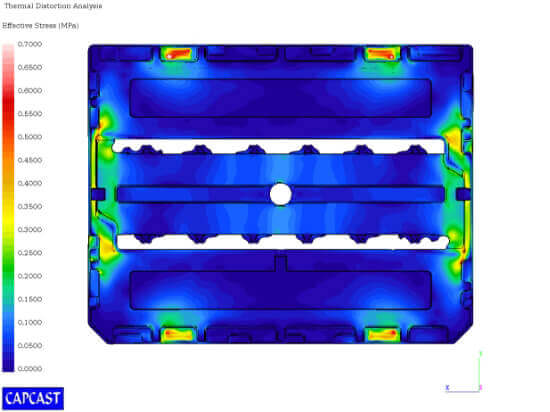
Impellers
Balancing Measurement and Correction of Impeller
We provide sophisticated balancing. We consistently measure and correct the balance at any point of the process.
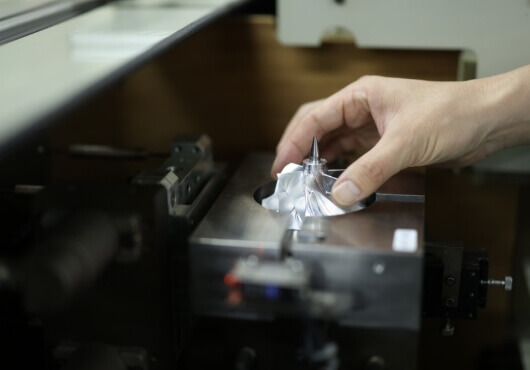
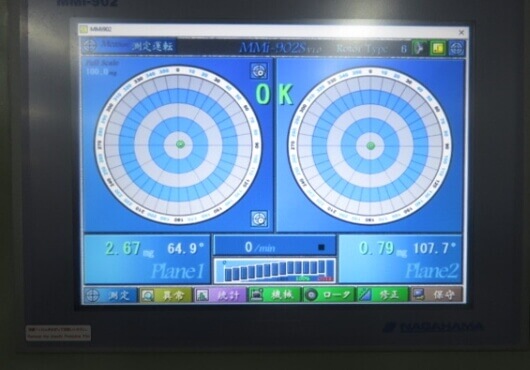
3D Measurement
With the 3D measurement machine, the accuracy of the measurement is higher compare to the result with a non-contact type measurement machine.
We comply with any requests from our customers and guarantee quality.
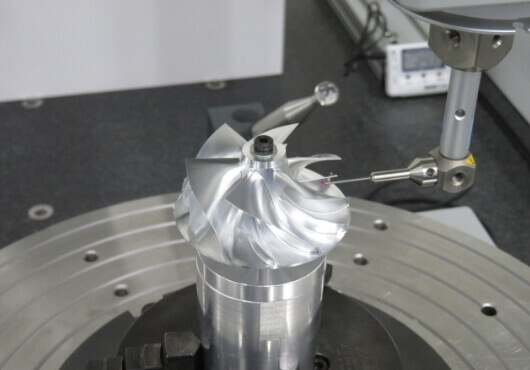
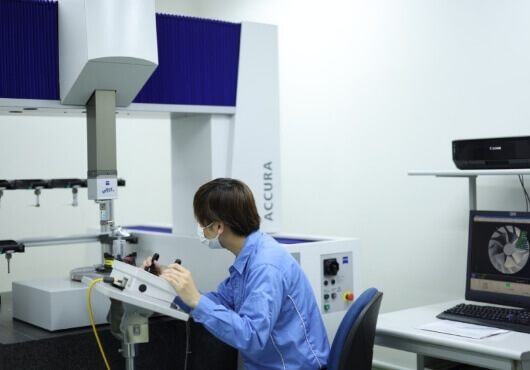
Machinable Wax
- ・We uniquely blend machinable wax which is suitable for casting, has excellent workability and does not easily get deformed even after processing.
- ・The material is molded in our own melting furnace.
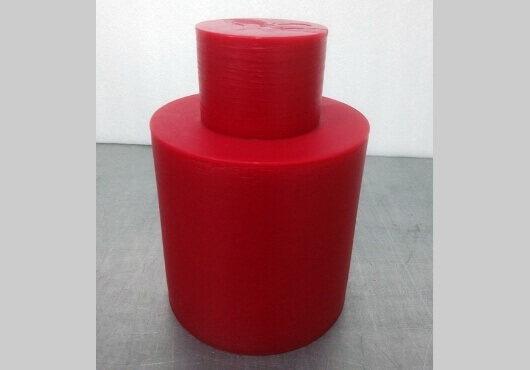
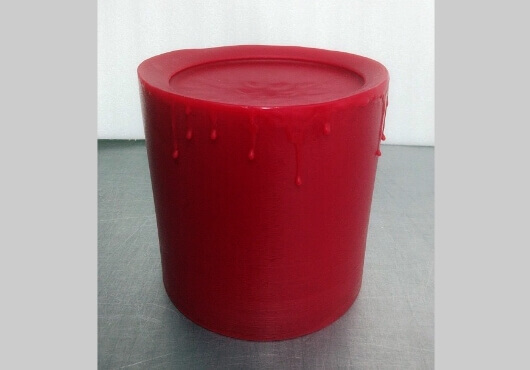
Processing Machinable Wax
We process original blended machinable wax for lost wax precision casting by 5-axis machining.
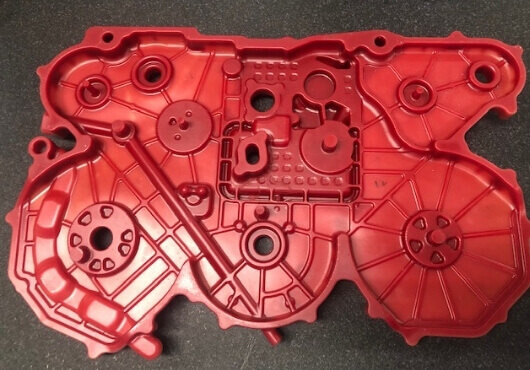
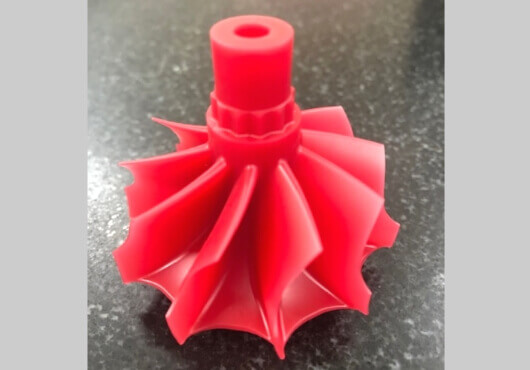
Prototype Castings
Cylinder Head Made of Nodular Graphite Cast Iron
We receive a request for cylinder head made of nodular graphite cast iron. Unfortunately, after the product shape is confirmed it is difficult to make it.Then how should it be solved?
Actually, it depends on the product shape.
It is necessary to add a lot of cylindrical risers in order to make shrinkage generated during FCD casting out of the product. We aim for directional solidification that the final solidification becomes a riser. When the product has a flat shape to which a riser can be attached, it is highly possible to be manufactured.
We analyze and simulate the layout of the riser until we get satisfied with the result then cast it.
Because we were able to model the water jacket and the shape of the riser connection freely, we actualized the directional solidification and suppressed the occurrence of shrinkage inside of the product.
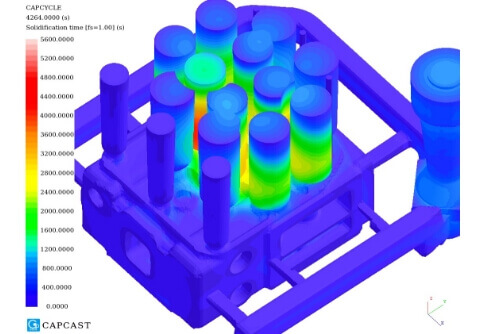
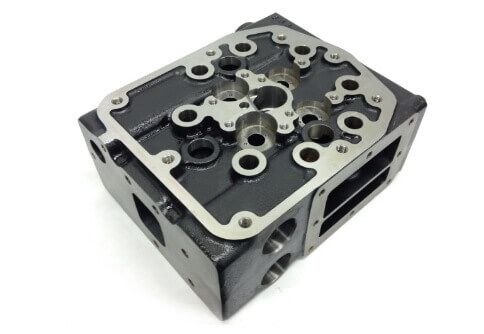
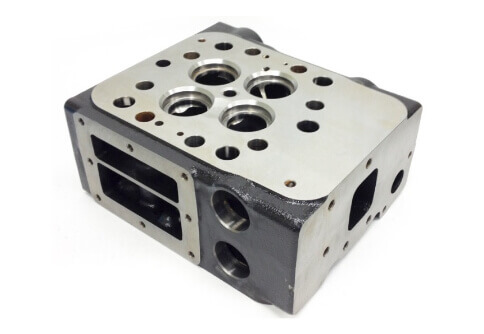
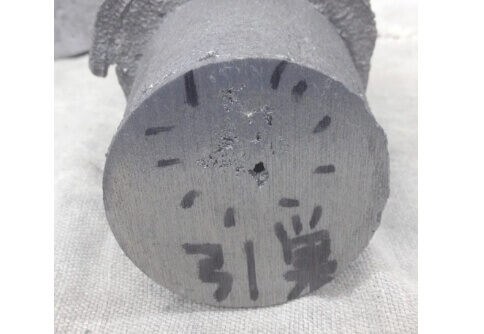
Quick Delivery of Casting by using 3D sand printer
We manufacture castings with short delivery times by using a sand-type laminated 3D printer. (The shortest delivery time: 7 days)
The process can be shortened without “the pattern for sand casting” so that it enables quick delivery. Since you do not have to think about punching with a pattern, you can make castings in any shape.
You can also expect the cost reduction. In most cases, it will be cheaper to make one or two items which do not require any correction with the 3D printer than making a pattern.
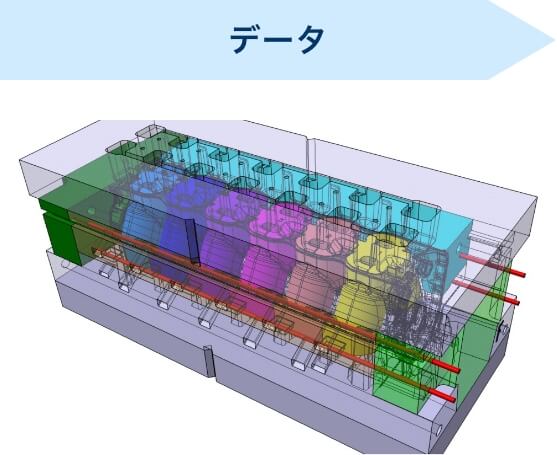
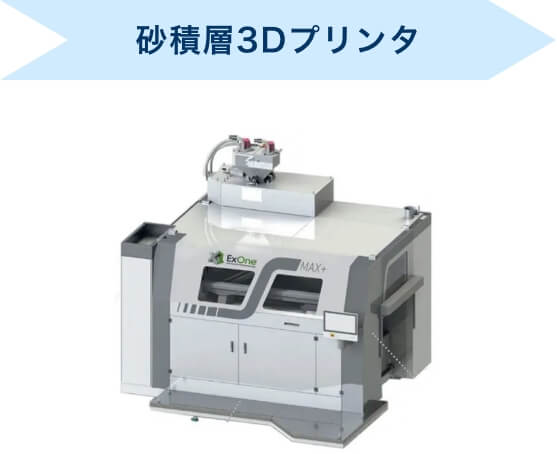
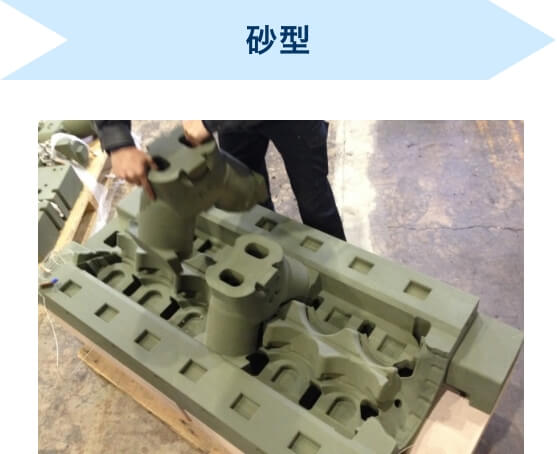
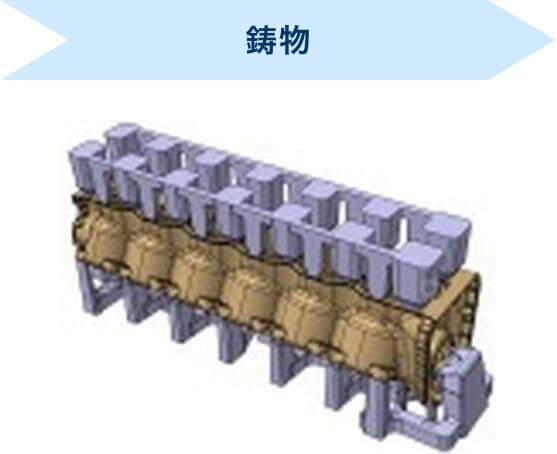
Runner Design – special filter(SEDEX), runner, thickness of weir
When the shape of the product is thin-walled but complex (cylinder head, etc.), we propose a runner design that makes the initial flow velocity of the weir as slow as possible within the target casting time.
On the other hand, when the shape of the product is thick and simple (bracket, etc.), we propose a runner design that makes the flow velocity as fast as possible within the target casting time.
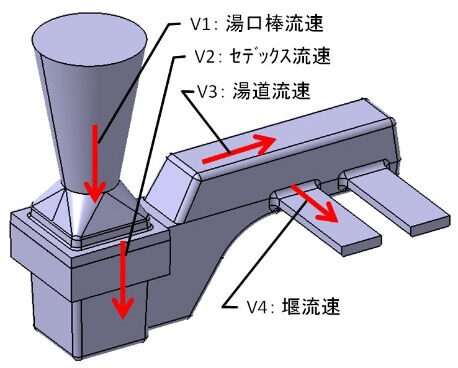
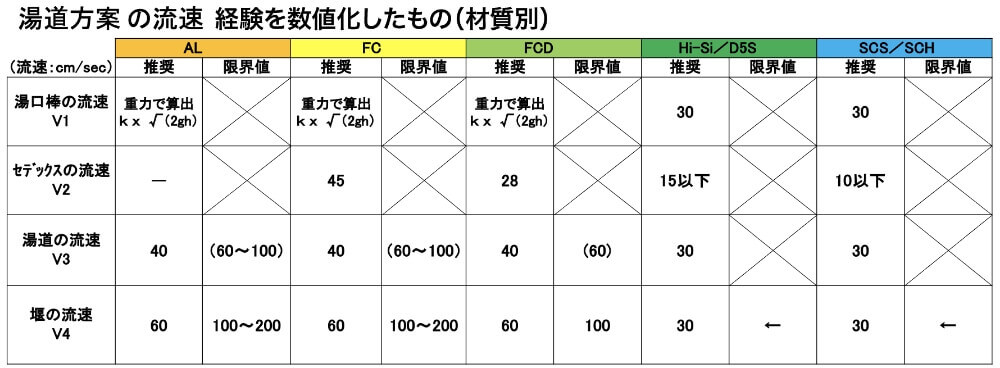
Complex Core Assembly Plan
The following is what we consider when we design the complex core assembly plan.
- ・Position stability when setting the passage core
- ・Retaining of the core grid and the formability
- ・Blow moldability of the form of the core
- ・Taking sand molds out of the pattern
- ・Changing the product shape
We take all the above into consideration then propose to add core prints and/or the division position of the core. Our proposal gives you some ideas of cost reduc
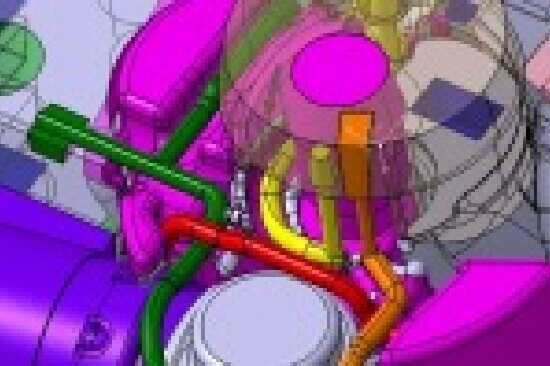
Estimate casting residual stresses in Nastran format.
Casting residual stress analysis values can be estimated in Nastran format. It opens the way for use in the design analysis software that your company uses. Excess thickness of the draft angle, parting edge, dam marks, etc. are analyzed with the accurate casting shape. (If Taguchi Pattern Works made the pattern.)
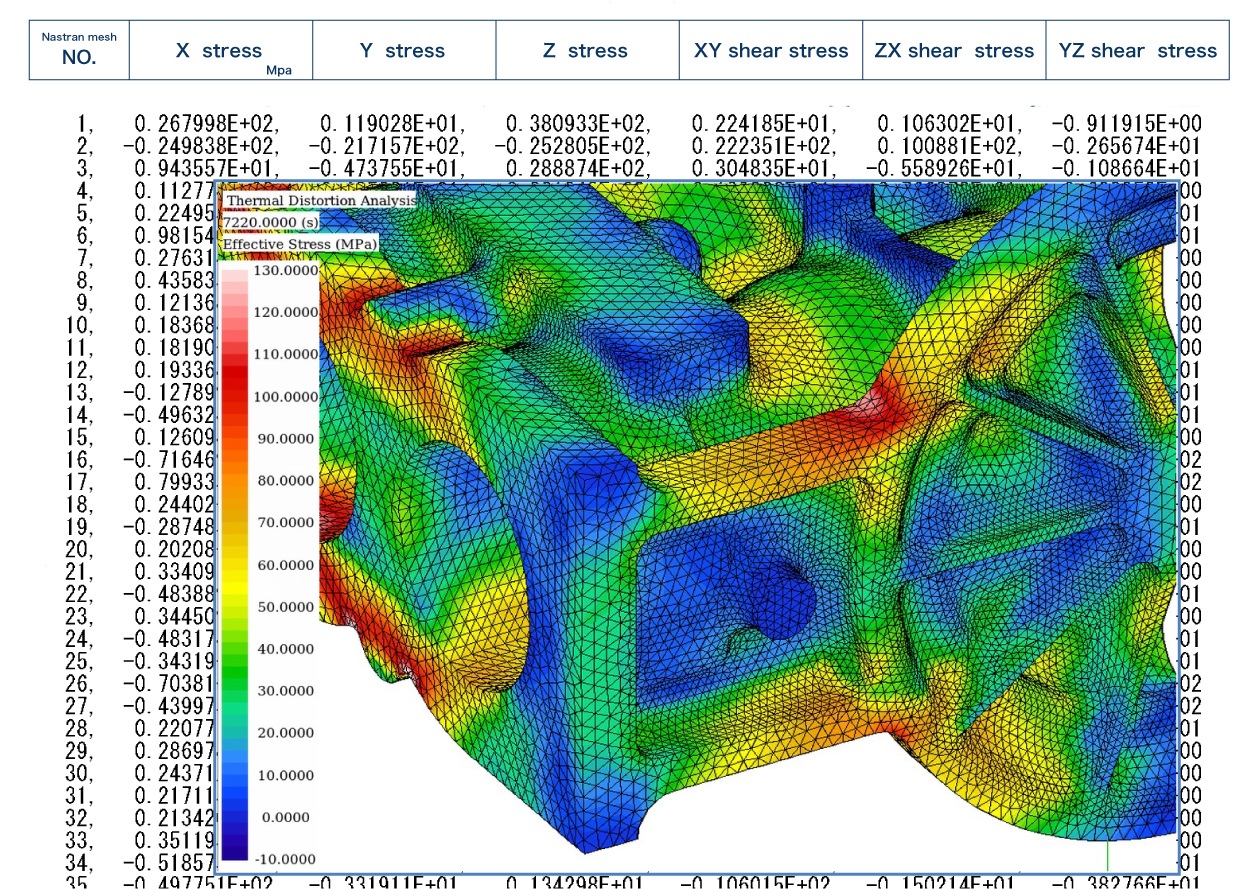
Predict residual stress during quenching after solution treatment.
In the heat treatment of aluminum, excessive residual stress may be generated to the product during quenching after solution treatment. It is simply because the material is rapidly cooled with water from a temperature of 500°C or higher.
This may cause cracks so changes in the design shape is required.
We predict a crack risk in advance and it lead to reduce the number of prototypes.
When there is a large difference in wall thickness, excessive residual stress tends to occur.
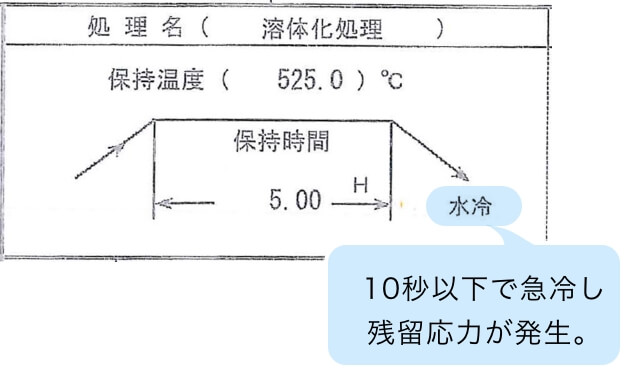
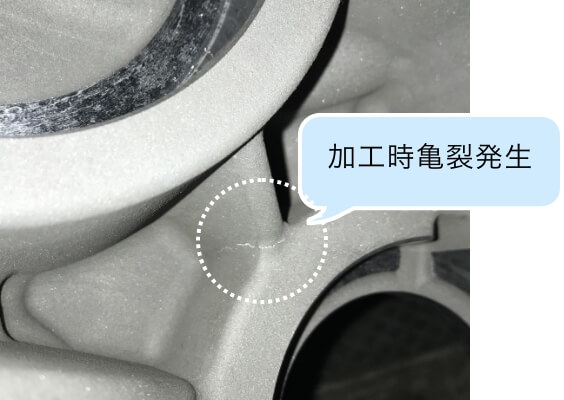
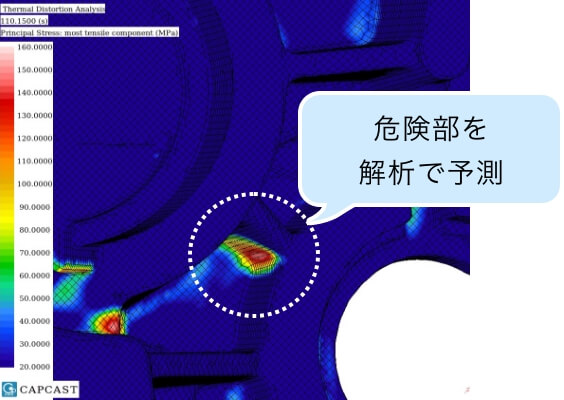
Can you handle the core?
You can check whether the core has enough strength to handle. This prevents troubles that cannot be cast, such as being damaged when lifted. Contributes to reducing the number of prototypes.
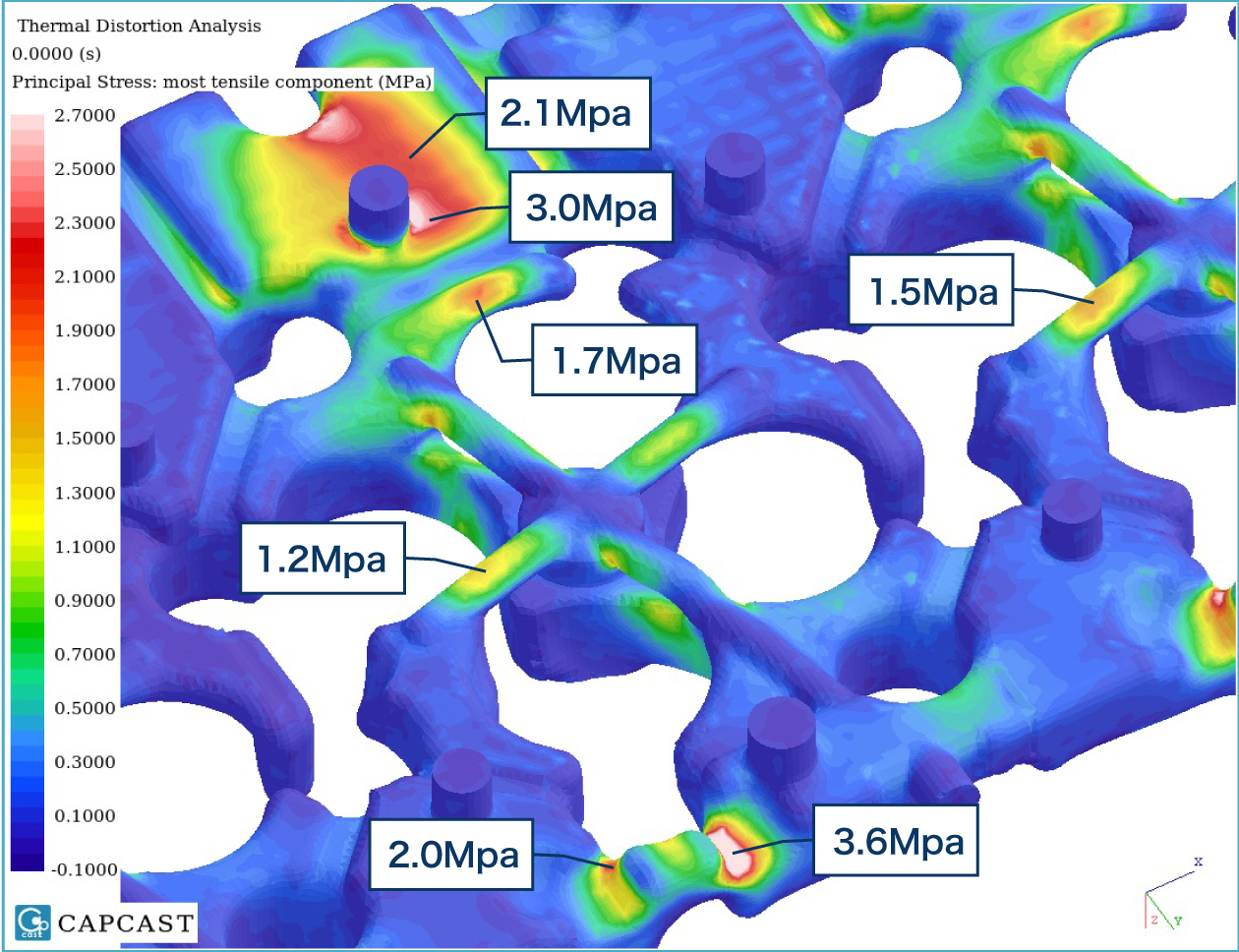
Predict the occurrence of Veining
Because water jacket cores are located inside of the products, once veining occurs, it leads to casting defects.(Water jacket flow channel may get closed.)
To prevent these events, design need to be changed.
We perform thermal expansion stress analysis to predict where the veining occurs. This leads to decreasing the number of prototypes.
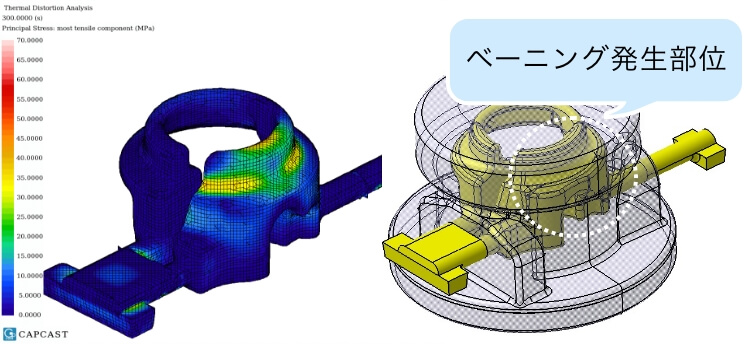
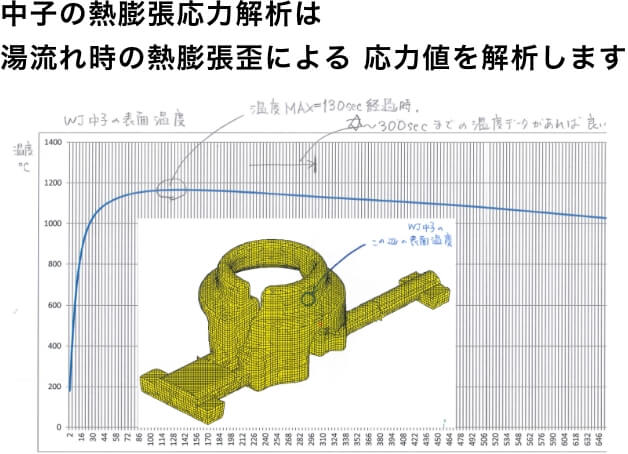
Prototyping learns from failure.
No matter how well you think and prepare, you can still fail. However, failures can lead to limitations of phenomena and new findings.
This is especially true for unprecedented prototypes. Accumulation of considering and recovering from past failures creates the current quality. That’s why we value our failure case database. The figure is an easy-to-understand failure.
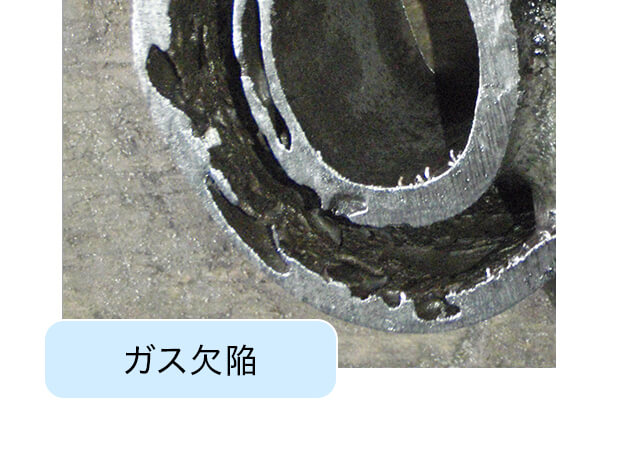
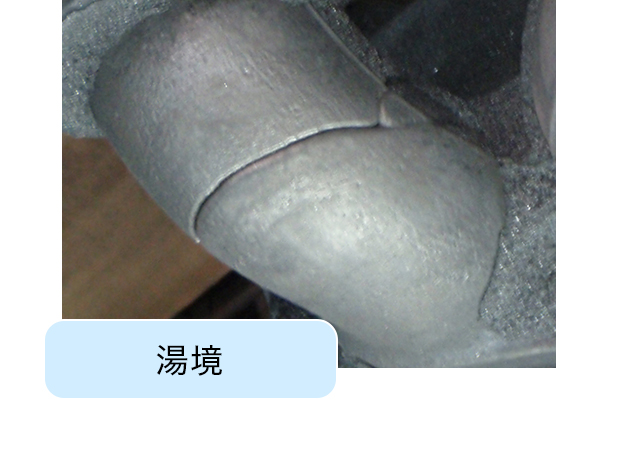
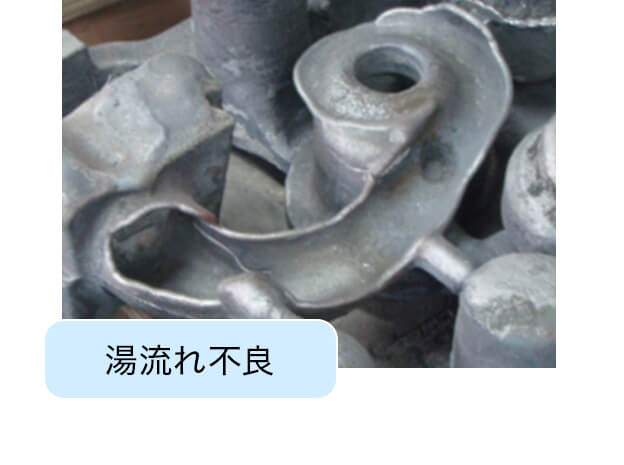
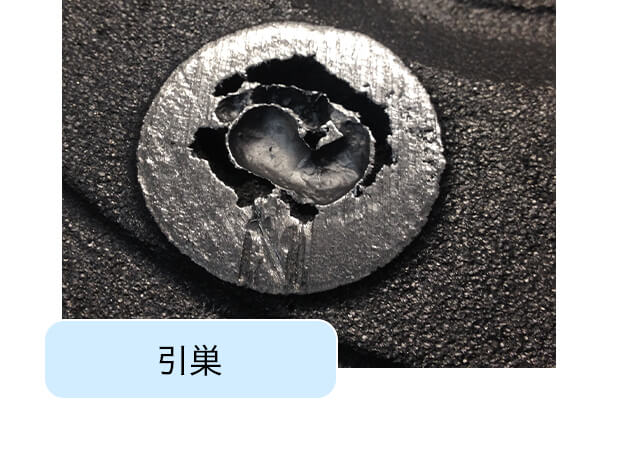
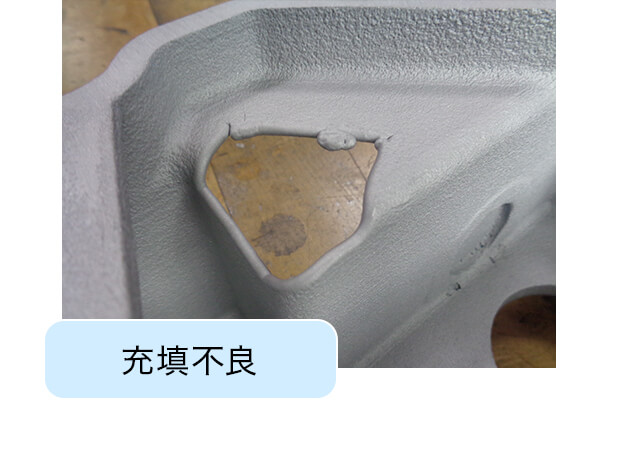
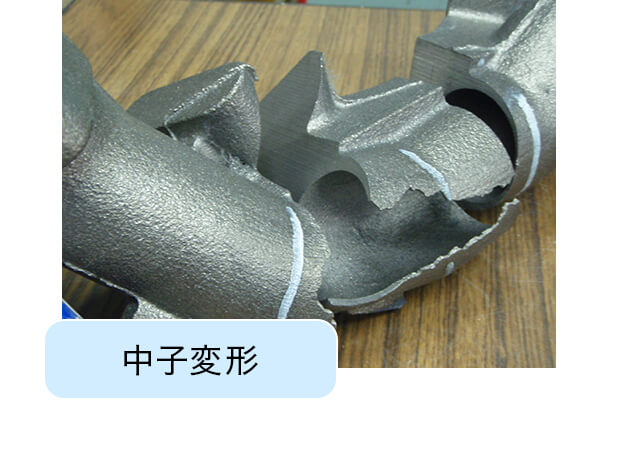
Processed Products
Automatic Deburring Machine
Burr is inevitable during machining. It used to be removed manually in the past but the quantity of work became large, so it is done by robots to reduce cost currently.
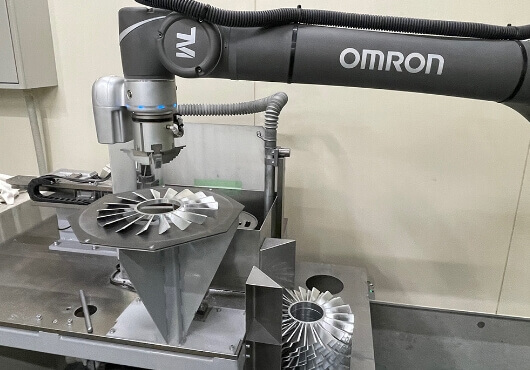
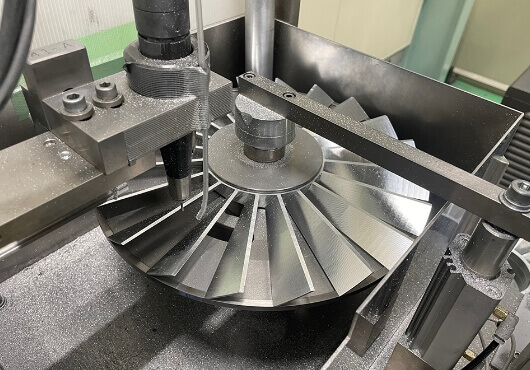
Achievements
Click on the fields you are interested in to find examples of our work.
Examples of
cases we put
efforts into
Automotive
related fields
Agricultural machinery
& Construction machinery
Industrial
machinery
Examples of cases we put efforts into
Heat sink
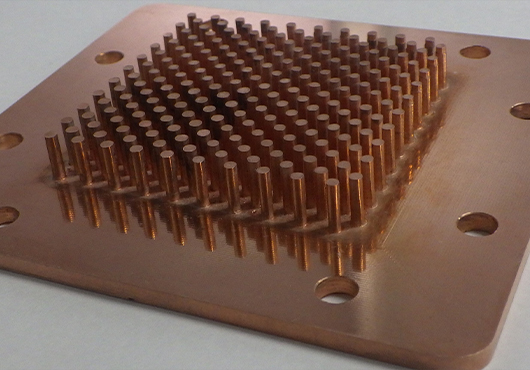
Outline of Heat sink
-
1.
The penetration of electric vehicles will increase in the future, thus a necessity of the thermal management of automotive products will be enhanced.
-
2.
For heat management in limited spaces, heat sink with microfabrication that has better heat radiation is required.
-
3.
Taguchi owns numerous 5-axis machining centers capable of advanced micromachining and continuous unmanned operation, allowing us to provide high-quality heat sinks at competitive prices.
ヒートシンク製作に適した設備(抜粋)
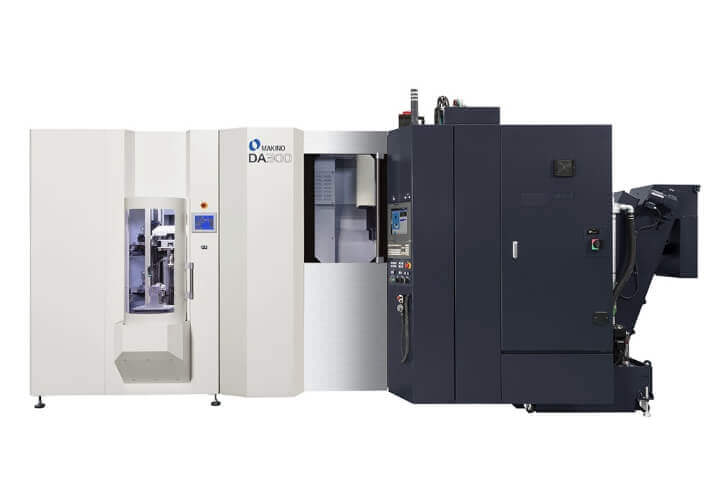
5-axis vertical machining center
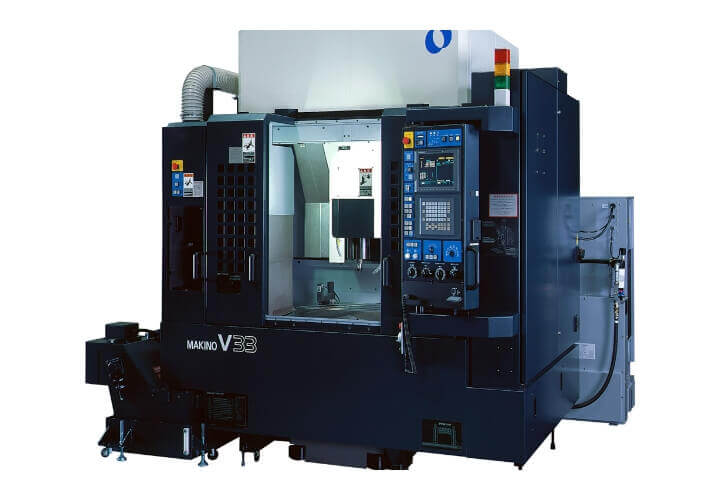
Vertical machining center
-
1.
Taguchi has many machining centers, which are the typical equipment required for heat sink manufacturing.
-
2.
The 5-axis vertical machining center (DA300) can operate continuously day and night thanks to the automatic pallet changer for 19 pallets, allowing us to offer competitive prices.
-
3.
The know-how we have accumulated in the manufacture of impellers for automobile engines can be applied to the manufacture of heat sinks, allowing us to carry out the important processes of cleaning, deburring, and inspection at a high level.
Impeller
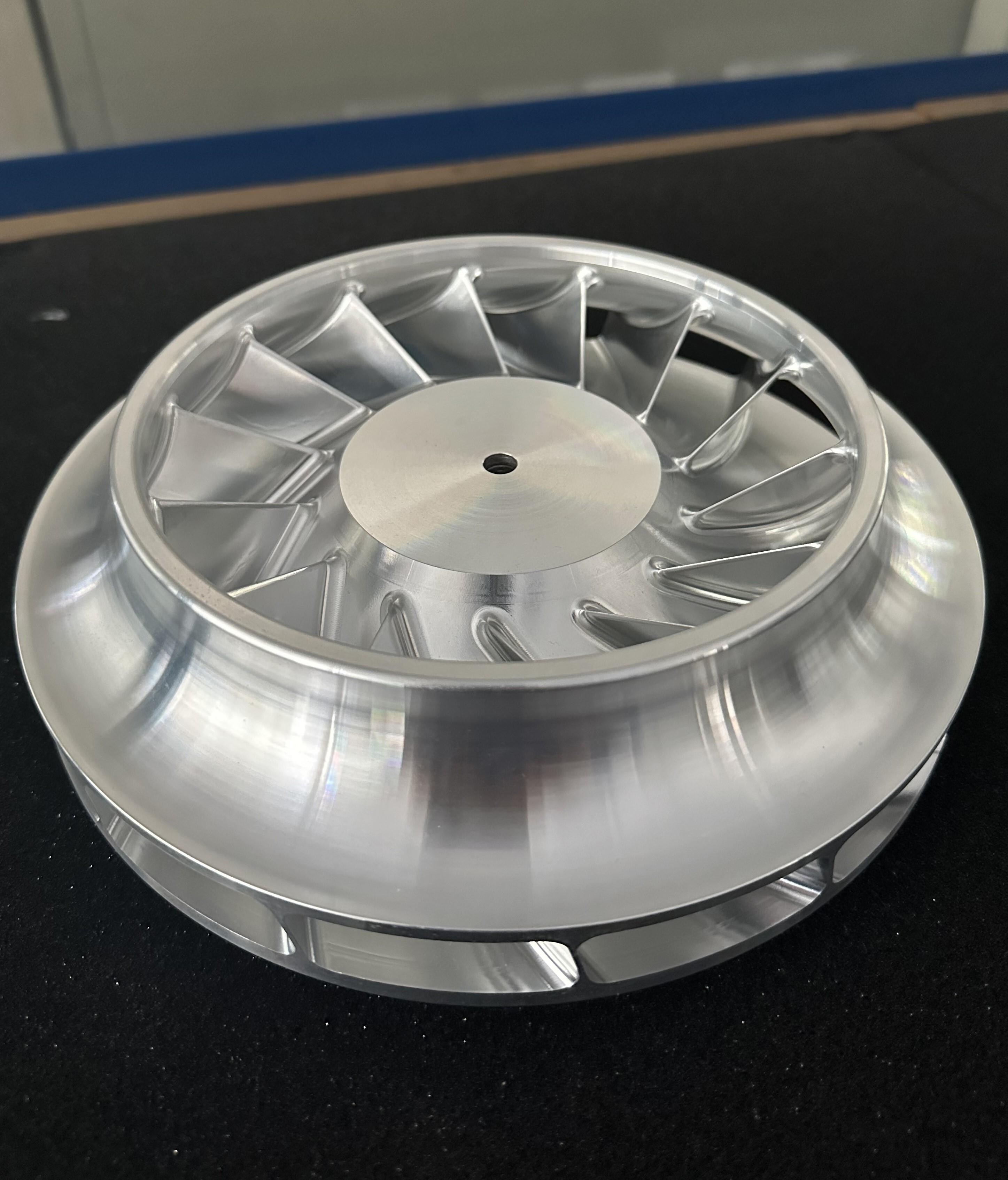
Outline of Impeller
-
1.
Impellers are used not only in intake compressor wheels for turbochargers, but also in superchargers, blowers for ships and motorcycles, and refrigerators.
-
2.
Closed impellers, in which the impeller body is covered by a side plate called a shroud, have the advantage of increasing the efficiency of the flow rate of the material, but they are difficult to manufacture, so the selection of cutting tools and the creation of CAM programs are important.
-
3.
Taguchi has a long history of producing impellers, and is skilled in selecting the right equipment for the impeller shape. Taguchi is also adept at using CAM for impeller processing, and is able to produce impellers with complex shapes efficiently and with high precision.
インペラ製作に適した設備(抜粋)
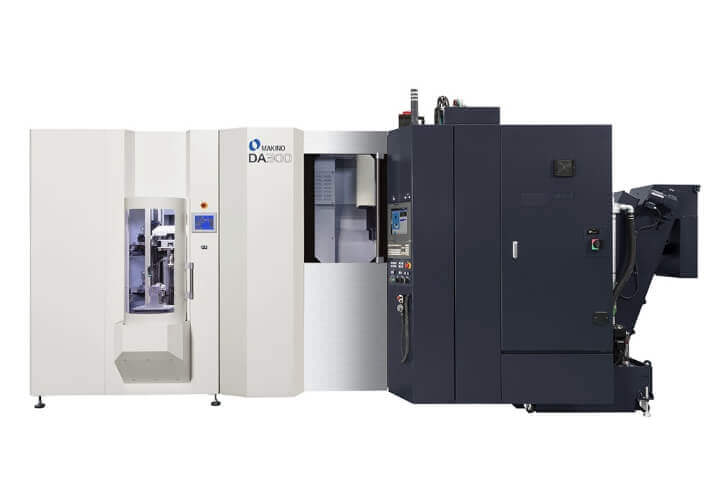
5-axis vertical machining center

Automatic Balance Correcting Systems
-
1.
Taguchi owns a total of 27 5-axis controlled machining centers, which are ideal for cutting impellers with complex shapes.
-
2.
In addition to high-precision cutting using a 5-axis machining center, we use balance measuring devices and automatic correction machines to provide impellers with the proper balance according to the design intent at a highly cost-competitive price.
-
3.
Inspection using a three-dimensional measuring machine is also possible, and we can also meet the high-precision dimensional guarantee required for shaft holes.
Large machining
Outline of Large machining
-
1.
We have a track record of machining many large machines, such as the main mold for V16 engines for generators, large crankcase cores set jigs, and fixed blades for large vacuum pumps.
-
2.
We also own facilities capable of manufacturing gas turbines for power generation facilities and jet engine parts for aircraft.
大型機械加工に適した設備(抜粋)
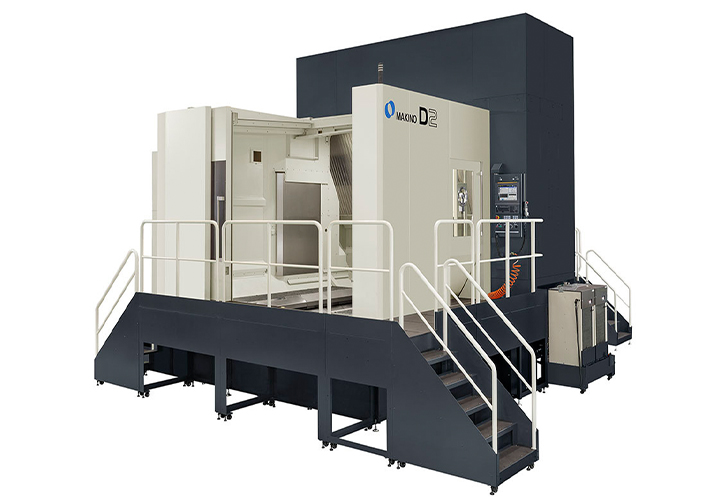
5-axis vertical machining center
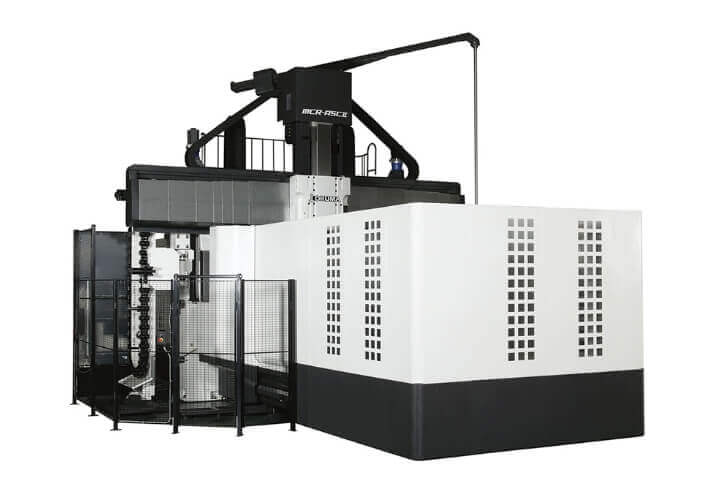
Double-Column Machining Centers (5-Face Machining)
-
1.
Taguchi owns a total of eight gantry machining centers suitable for large-scale machining, with the largest table work surface being X4000 x Y2000 x Z450, capable of heavy cutting of large workpieces over a meter in size.
-
2.
In addition, we also have a 5-axis controlled vertical machining center capable of turning, making us fully capable of machining large workpieces with complex shapes.
-
3.
We consider deformation caused by the load of large workpieces themselves and study optimal jig designs and processing methods.
Semiconductor manufacturing equipment parts
Outline of Semiconductor manufacturing
-
1.
The evolution of semiconductors, information processing technology, and information and communication technology shows no sign of stopping. As the amount of information processed continues to expand, the era in which the use of digital technology will be a source of competitiveness will continue (Excerpt from Semiconductor and Digital Industrial Strategy, June 2023 (Ministry of Economy, Trade and Industry, Bureau of Commerce and Information Policy))
-
2.
In fact, the semiconductor manufacturing equipment industrial production index is expected to grow to more than 200 in 2022 compared to the 2015 index.
-
3.
Although the market may continue to fluctuate due to the semiconductor cycle, this is an area where growth is expected in the medium term.
-
4.
As semiconductor processing becomes more advanced, the need for high-precision processing of semiconductor manufacturing equipment also increases.
Equipment suitable for manufacturing semiconductor manufacturing equipment parts
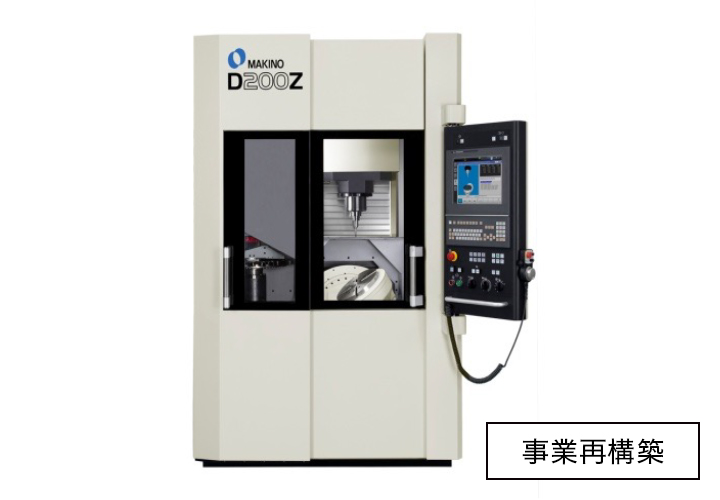
5-Axis Vertical Machining Center
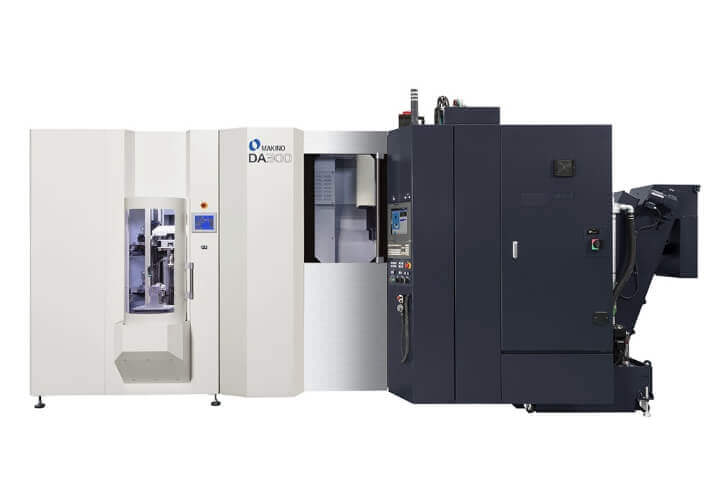
5-axis vertical machining center
-
1.
Taguchi owns various machining centers (vertical: 36 units, horizontal: 5 units) and has the know-how to utilize machine tools that has been honed over more than 75 years of business history. Not only do we rely on 5-axis machining centers capable of ultra-high-precision machining, but we also select the most suitable machine for each process, enabling us to optimize precision, efficiency, and cost.
-
2.
The aluminum material often used in semiconductor manufacturing equipment has a large thermal expansion coefficient, which means that its size is prone to change due to temperature, and its low elasticity makes it prone to distortion.
-
3.
Taguchi Katahan is also skilled in heat management and material handling to prevent such problems.
Reverse engineering of molds
The need for reverse engineering of molds
-
1.
Currently, many manufacturers have introduced CAD and often have product data in electronic form, but for products that were manufactured before CAD became widespread, it is not rare that not only electronic data but even mold drawings no longer remain.
-
2.
In addition, when mass production is outsourced, the dies are often left with the outsourcing company, and with the dramatic changes in the economic environment over the past three to four years since the beginning of 2020, there have been cases where the dies have been lost due to the outsourcing company going out of business, etc.
金型のリバースに適した設備(抜粋)
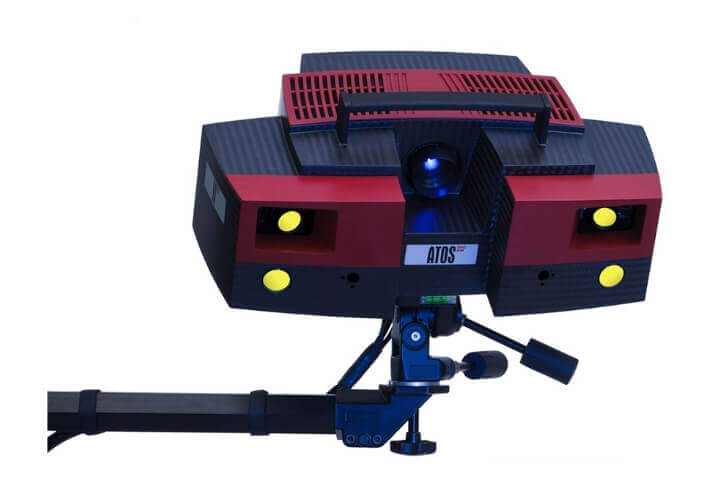
Contactless Optical Three Dimensions Digitizer
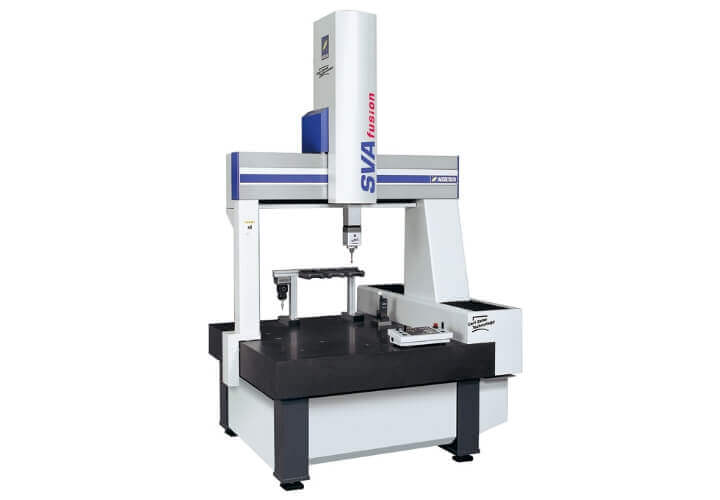
Three Dimensions Measuring Machine
-
1.
Our Kawaguchi and Nihonmatsu factories have a total of two non-contact optical 3D digitizers, which are ideal for reverse modeling, and we also have a total of five contact measuring machines at our Kawaguchi and Nihonmatsu factories.
-
2.
In addition to having equipment suitable for reverse modeling, we provide mold reverse modeling by engineers with the knowledge and experience to operate that equipment.
-
3.
Since mold manufacturing is Taguchi’s main business, we can also manufacture molds based on data reversed by Taguchi.
3D Printer
3D Printer Trends
-
1.
As 3D printers continue to evolve, they have moved beyond the stage of making prototypes to the stage where mass production is possible, and many products are literally “printed” by 3D printers.
-
2.
With state-of-the-art equipment and the technology and knowledge accumulated over 75 years of business history, Taguchi, who specializes in manufacturing sand casting molds, quickly recognized the future potential of 3D printers and was the first in the industry to introduce them.
-
3.
The strength of 3D printers is that they can produce complex, intricate, three-dimensional shapes, particularly those with complex internal shapes, in a short time, which is difficult to achieve using machined wooden or metal patterns.
3Dプリンターによる砂型製造に適した設備
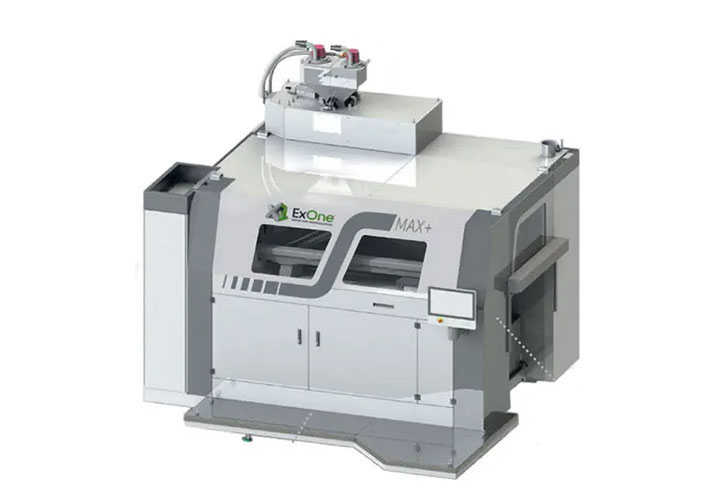
Sand layering device (3D printer)
-
1.
The ExOne 3D printer creates custom finished products from 3D CAD files using sand or ceramic materials.
-
2.
It can handle complex designs not possible with traditional manufacturing approaches, and design changes can be made in seconds on the 3D CAD file and re-printed without complex and costly modifications. With fast printing speeds and infinite part geometries, the ExOne is the perfect choice for cost-effectively printing customized parts using industrial-grade materials.
※Please refer to ExOne’s website -
3.
Dimensions (capacity): X1800, Y1000, Z700; large sand molds can also be produced.
Blisks
Outlines of Blisks
-
1.
Thanks to advances in casting technology, blisks, which are used in aerospace, aircraft, gas turbines, etc., have become more precise than conventional rotor blades, and are increasingly being manufactured by machining.
-
2.
The actual material used for blisks is often a heat-resistant alloy such as titanium, which is used in aircraft engines, but the prototype blisks used for blisk demonstration are often aluminum prototypes.
ブリスク製作に適した設備(抜粋)
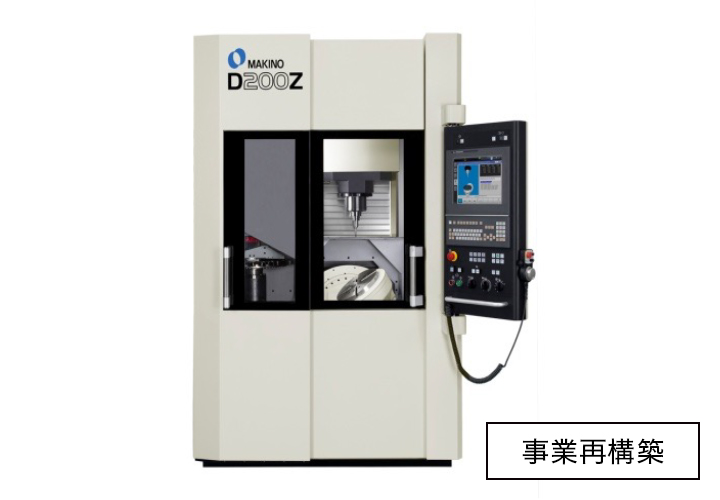
5-Axis Vertical Machining Center
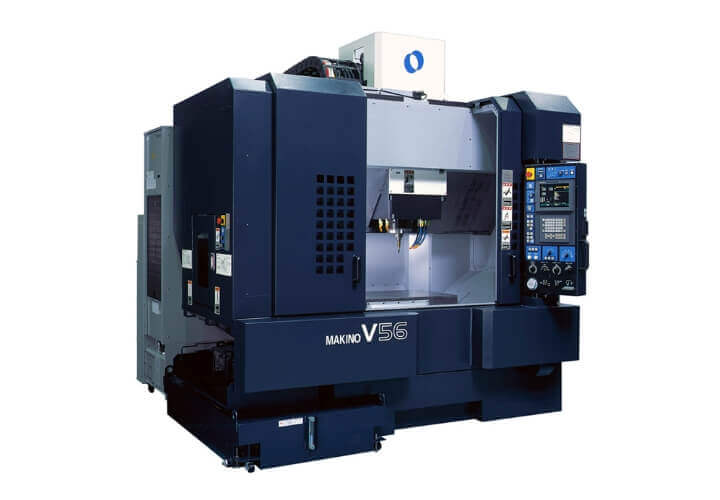
Vertical Type Machining Center
-
1.
Taguchi, which is skilled in impeller manufacturing, is able to utilize a total of 27 five-axis machining centers for blisk manufacturing.
-
2.
Rather than using a 5-axis controlled machining center from the initial process, we can propose to select an appropriate machine from our many (19) machining centers to perform rough machining, and then use a 5-axis controlled machining center for the post-processing, thereby reducing production time and costs.
-
3.
In addition, we also have CAM suitable for blisk manufacturing, and our engineers who are skilled in CAM operations can efficiently provide blisks, which are difficult to process, with high precision.
Aerospace
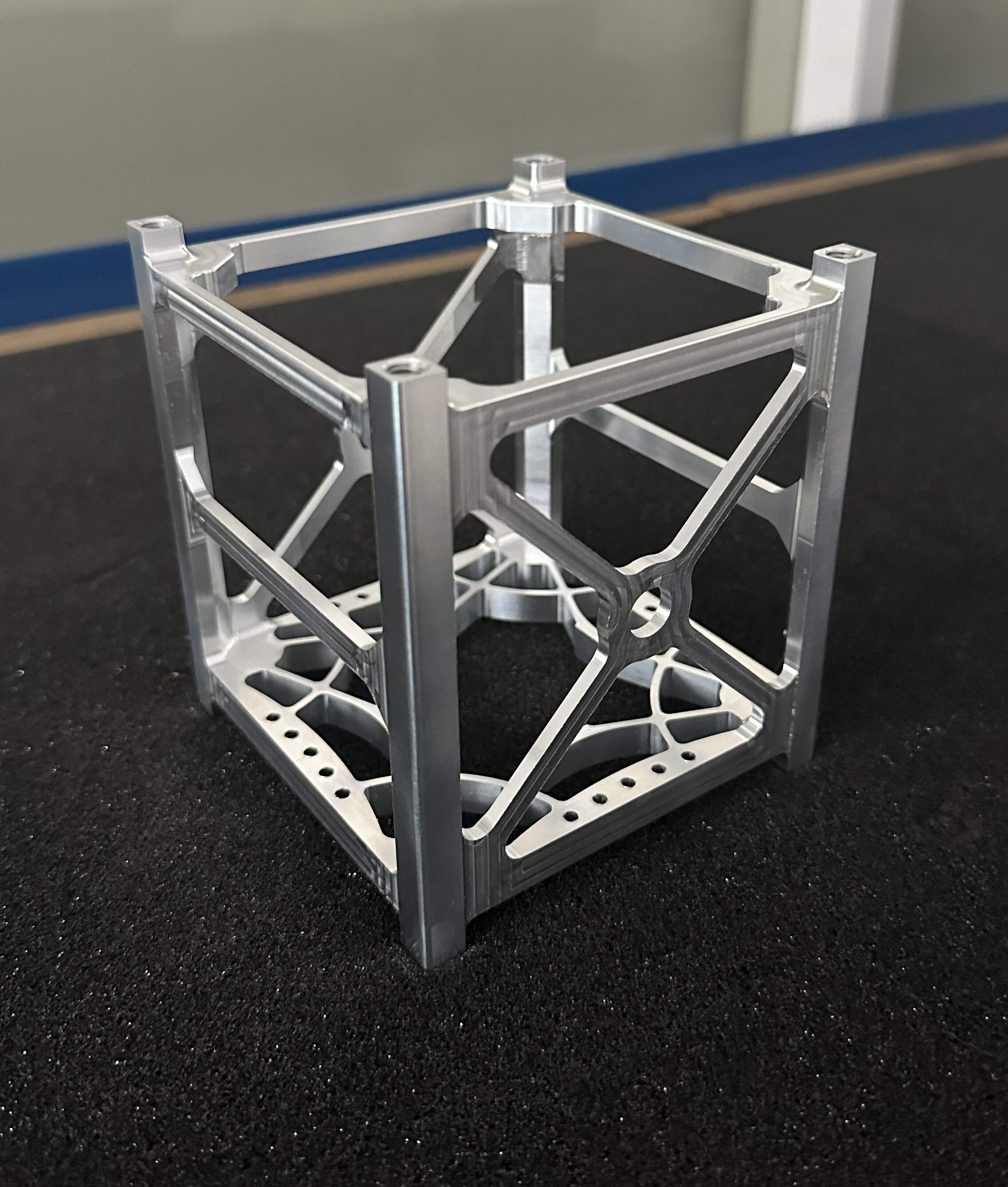
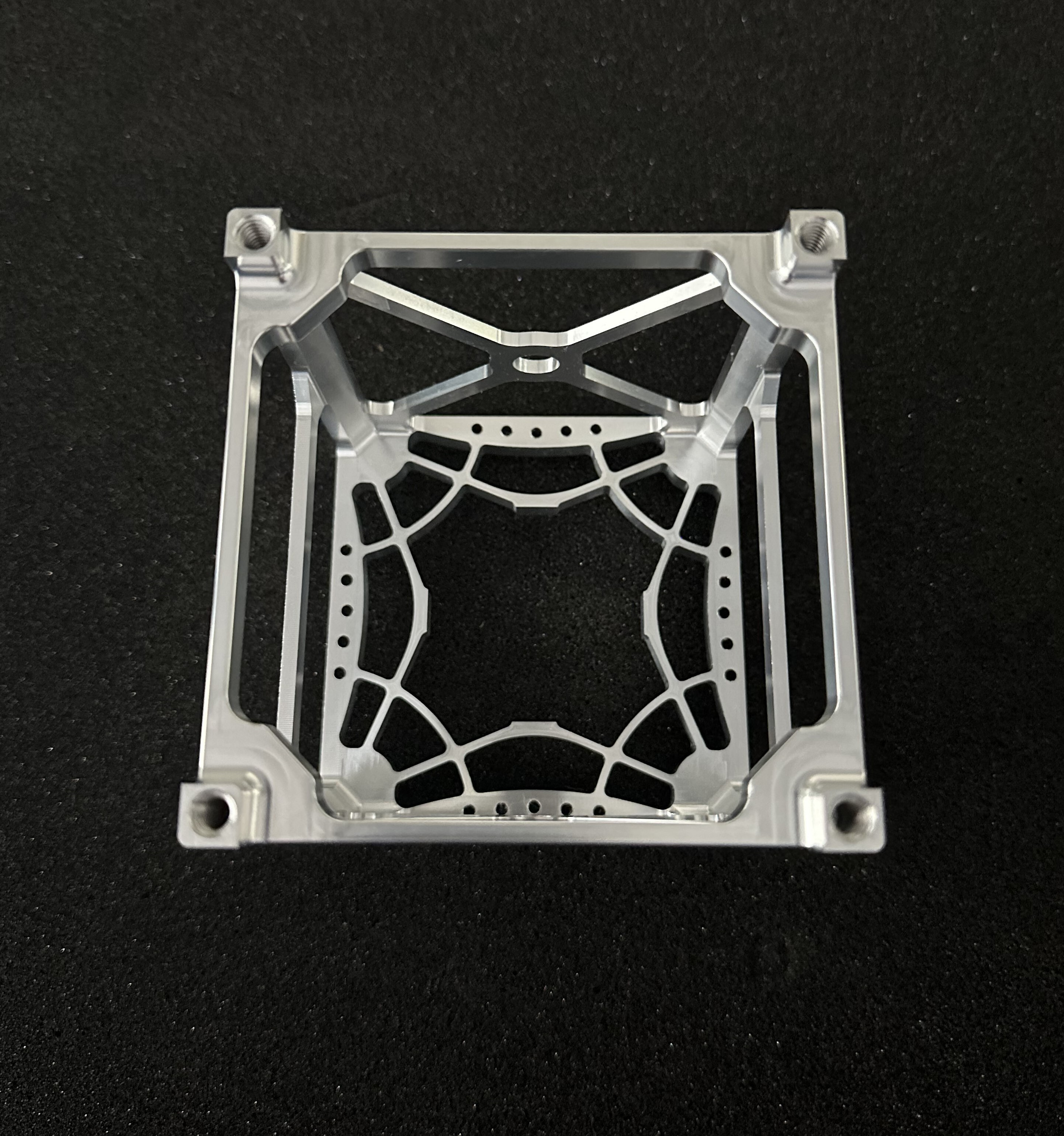
Outline of Aerospace Parts
-
1.
For example, inducers used in liquid rocket engines are often manufactured by casting or machining, and high quality is required, especially for surface roughness, to prevent cavitation.
-
2.
Furthermore, the frames of small 10 cm square cube-shaped satellites known as CubeSats, which are expected to become more common in the future for space exploration purposes, often require direct machining from ingots, without the need for welding or gluing, to ensure strength and reduce weight.
-
3.
Taguchi’s extensive equipment, metal processing know-how, and experience can be utilized in the production of inducers and CubeSats.
航空宇宙分野に適した設備
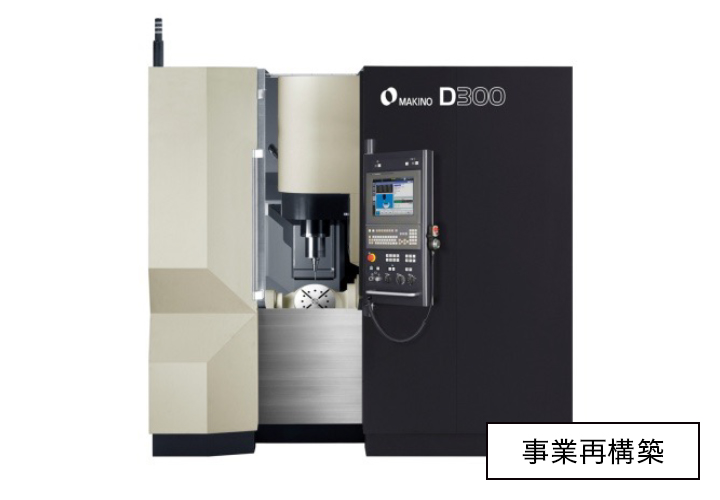
5-Axis Vertical Machining Center
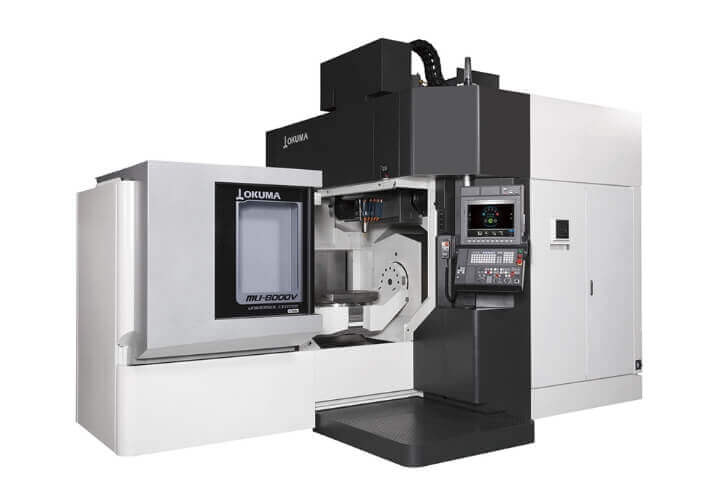
5-Axis Vertical Type Machining Center
-
1.
For example, it is desirable for the housing of a CubeSat to be a one-piece molded frame made by direct cutting using a 5-axis machining center or similar.
-
2.
In other words, aerospace products require space quality that satisfies all of the following criteria: precision, strength, and weight reduction.
-
3.
It is our hope to contribute to space research and exploration by making full use of the machining know-how we have accumulated over many years of business experience (temperature control around the workpiece throughout the factory, optimal equipment selection from our abundant 5-axis machining centers, effective use of CAM, etc.).
Automotive Related Fields
Automotive Powertrain
Cylinder Block Water Jacket (Metallic Pattern)
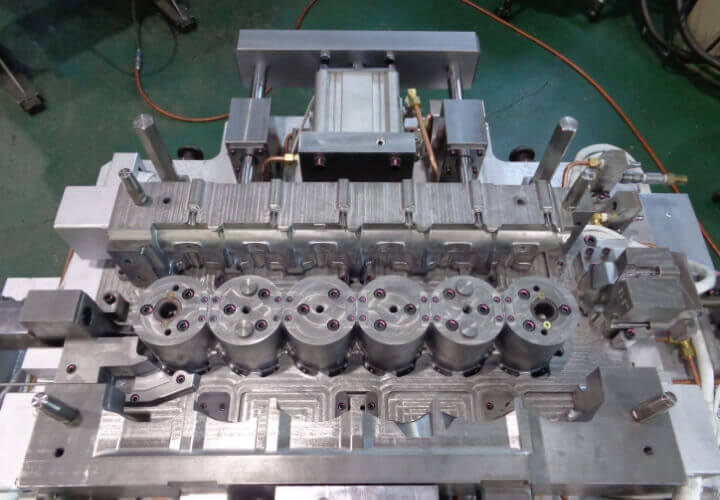
Cylinder Block
(Metallic Pattern with gas pins)
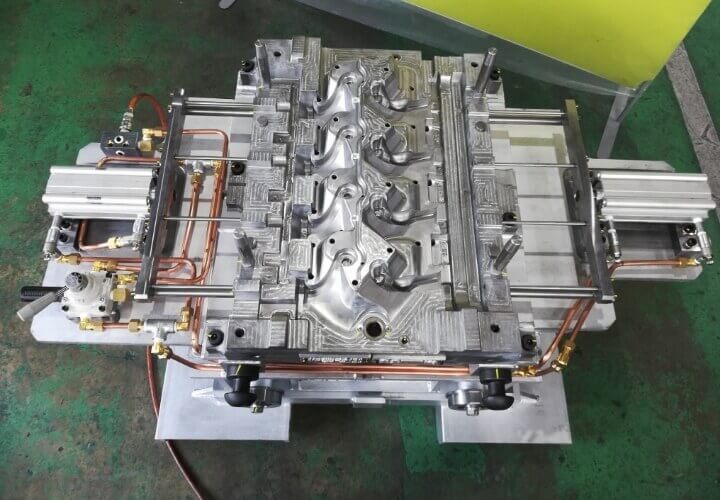
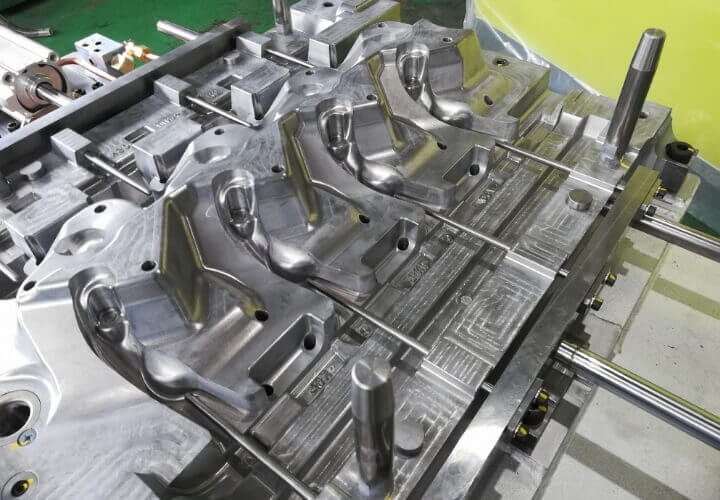
Cylinder Block (3 different cores can be made by only one pattern)
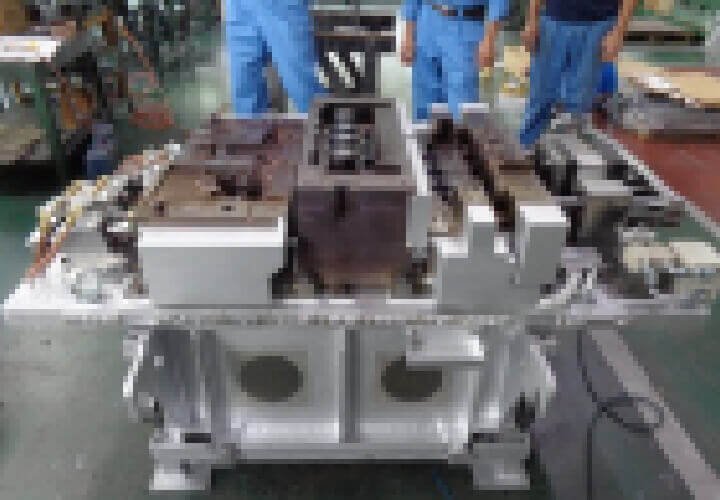
Exported to Malaysia Metallic Base Pattern for Casting
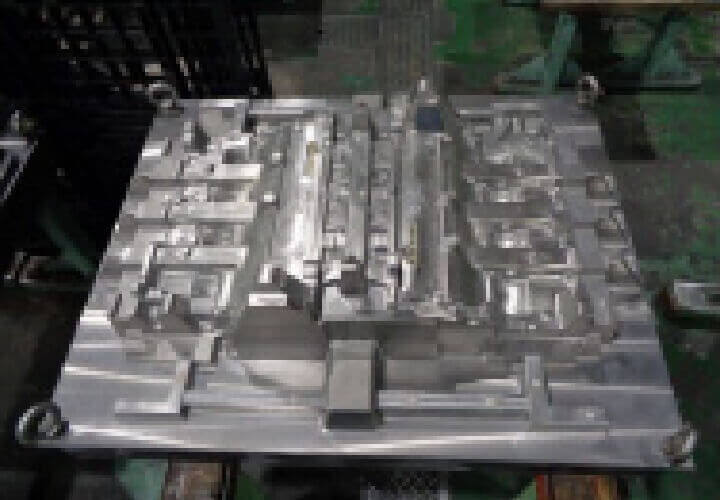
Exported to Malaysia Crank Case and Base Pattern for Automobiles
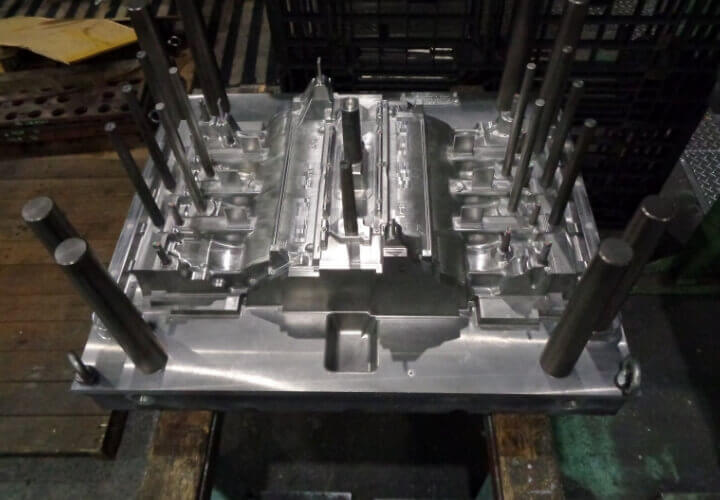
Exported to Malaysia Single Cylinder Head for Motorcycle Low Pressure Die Casting
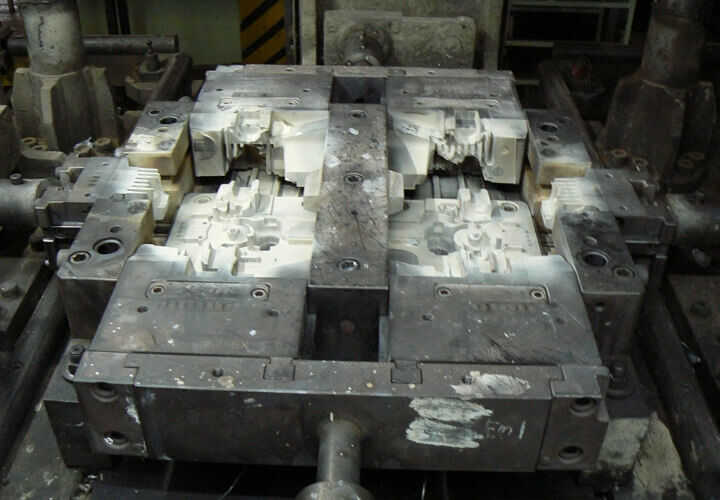
Large Cylinder Block Crank Case Core Boxes
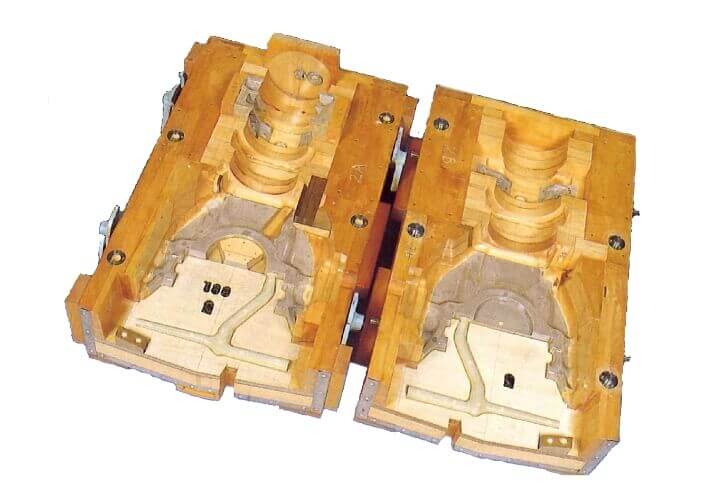
Large Cylinder Block Base Patterns
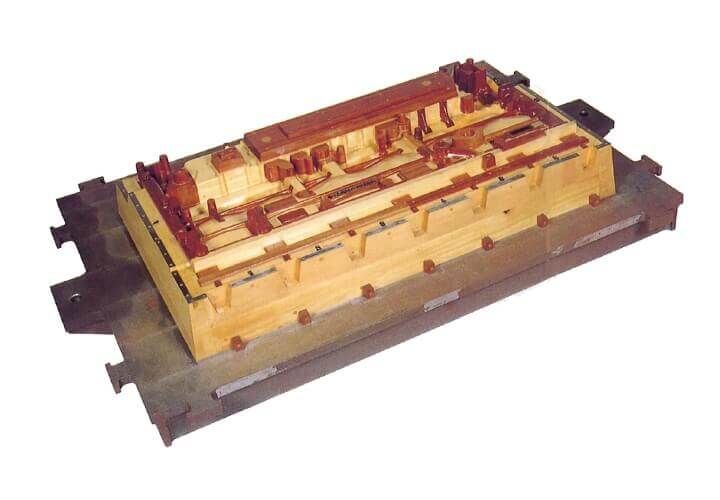
Automobile Suspension Parts
Exported to Thailand Metallic Patterns for Automotive Suspension Parts
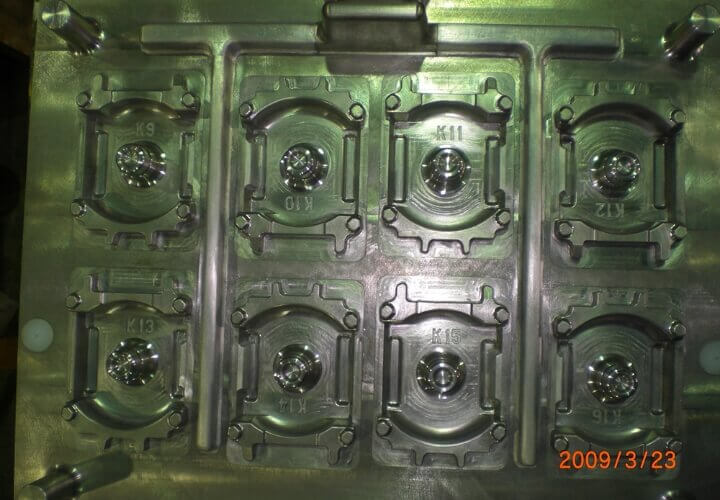
DIFF1
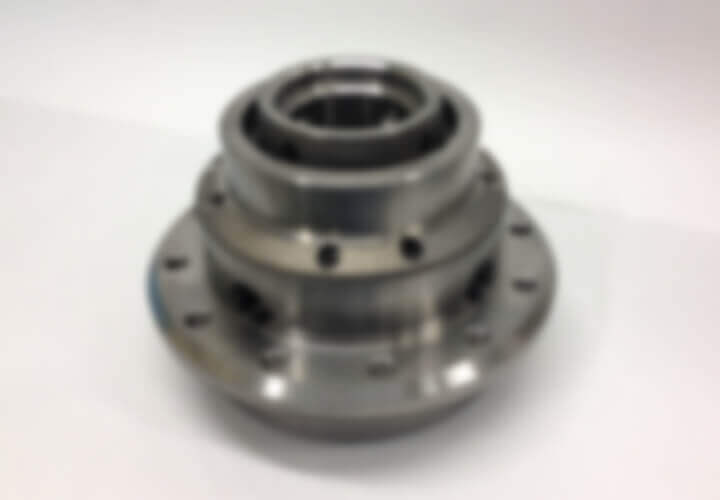
DIFF2
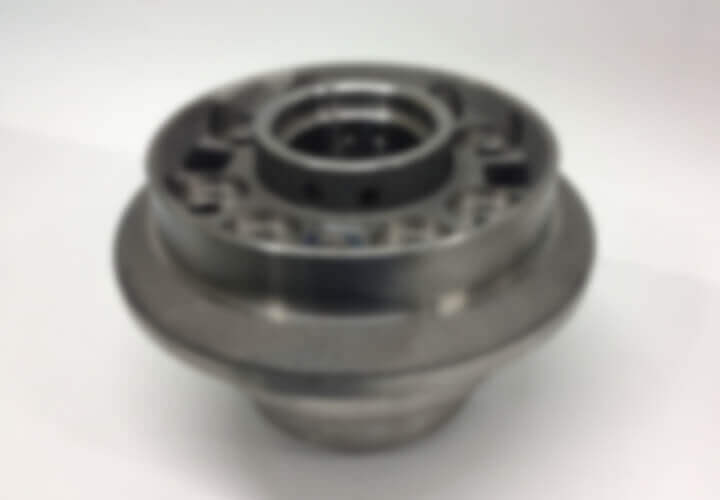
FW_HSG1
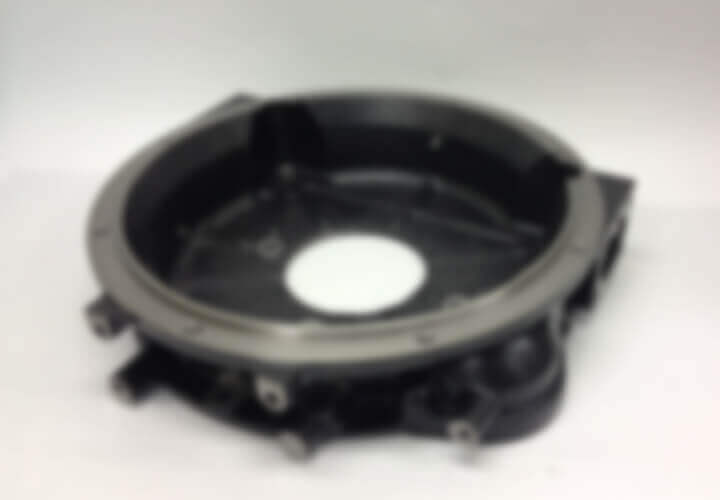
HUB1
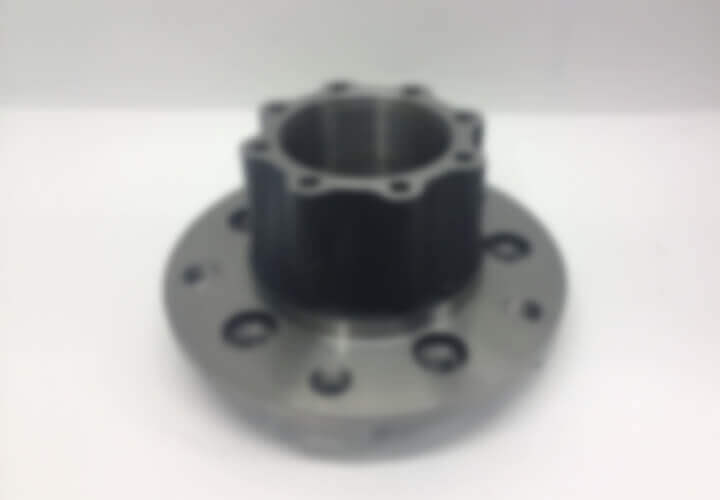
HUB2
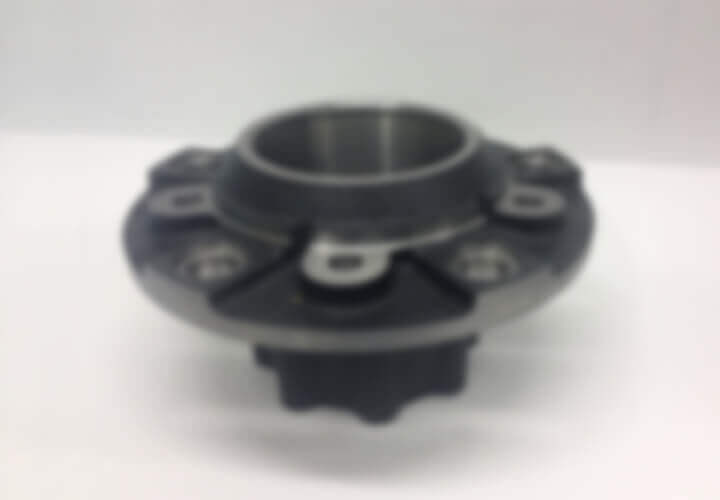
THERMOSTAT HSG1

Others
EXHAUST MANIFOLD
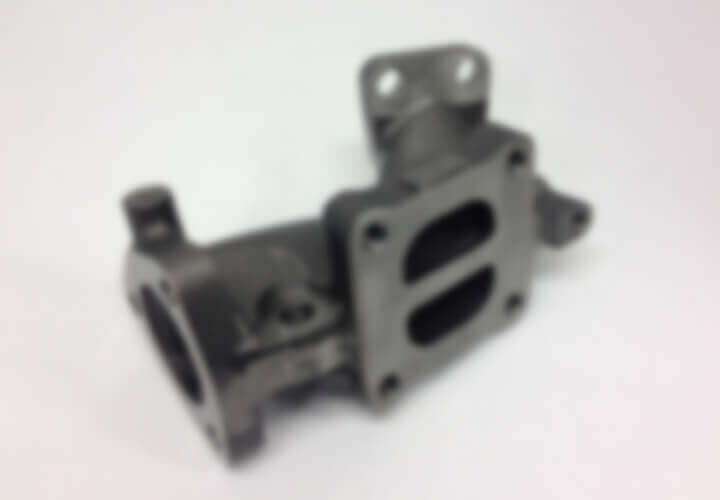
BRACKETS
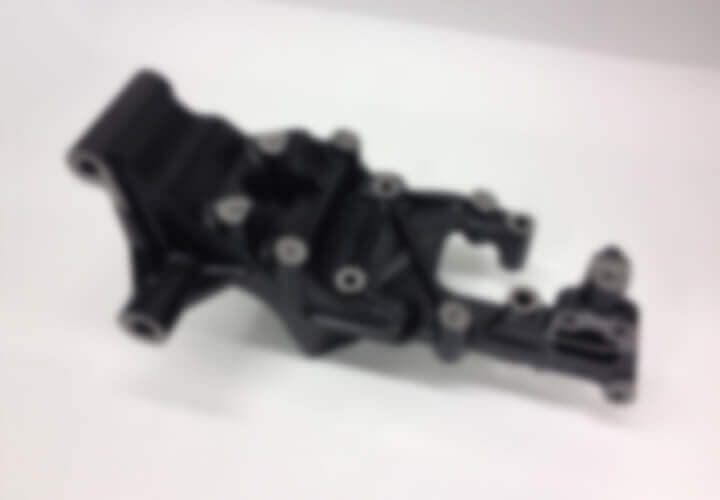
Agricultural Machinery and Construction Machinery Fields
Agricultural Machinery
Mold for agricultural machinery transmission case
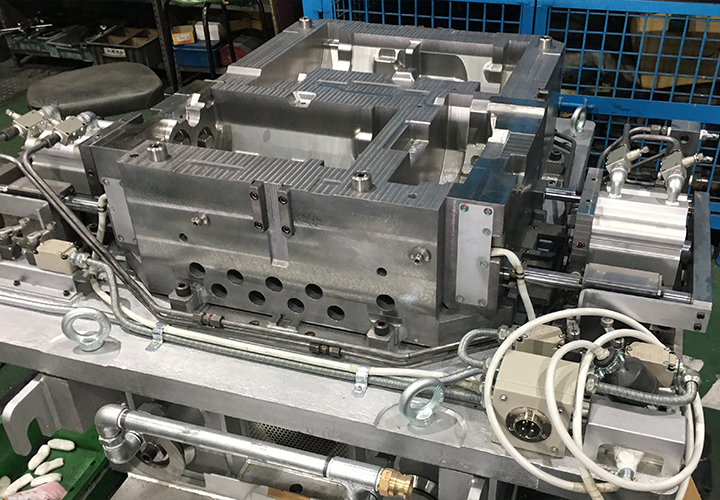
Cylinder head mold for agricultural machinery engines
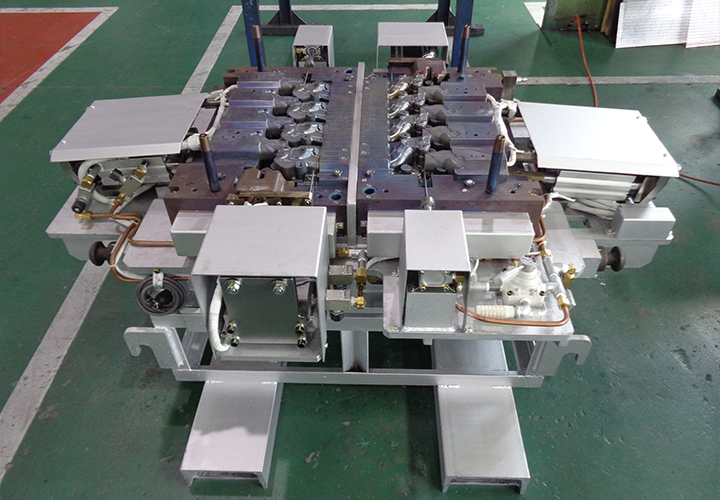
Construction Machinery
Carrier
写真の提示出来ません
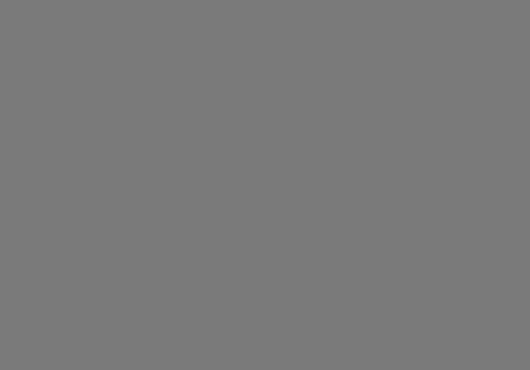
Flywheel housing
写真の提示出来ません
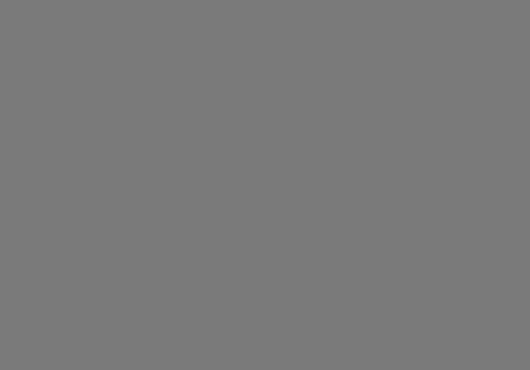
Oil cooler cover
写真の提示出来ません
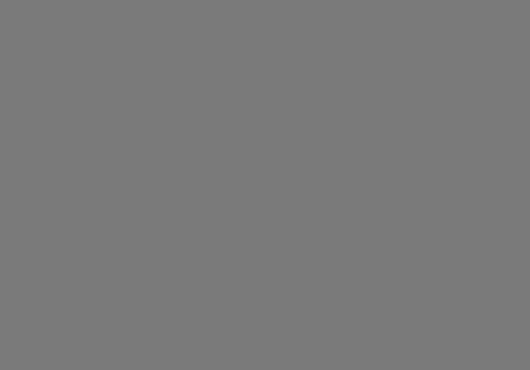
Industrial Machinery and Facilities Fields
Robots
Base
写真の提示出来ません
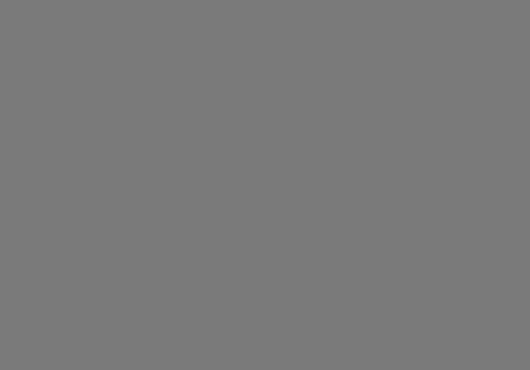
Arm
写真の提示出来ません
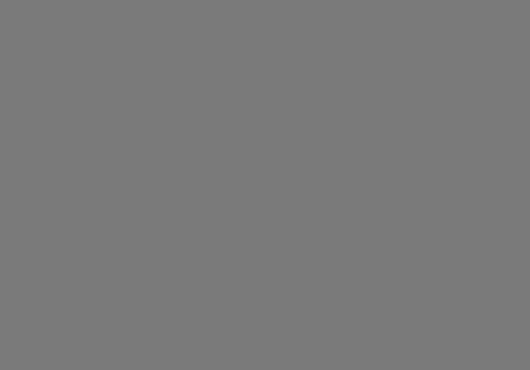
Impeller
Impeller Wax (Metallic Pattern)
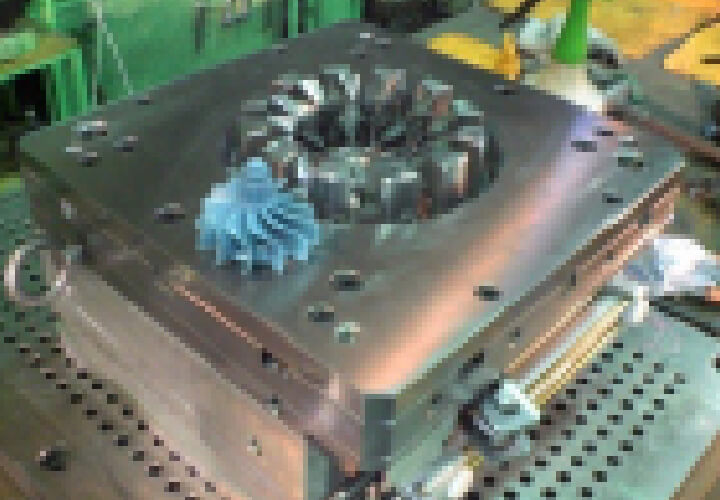
Multi Spreader Impellers
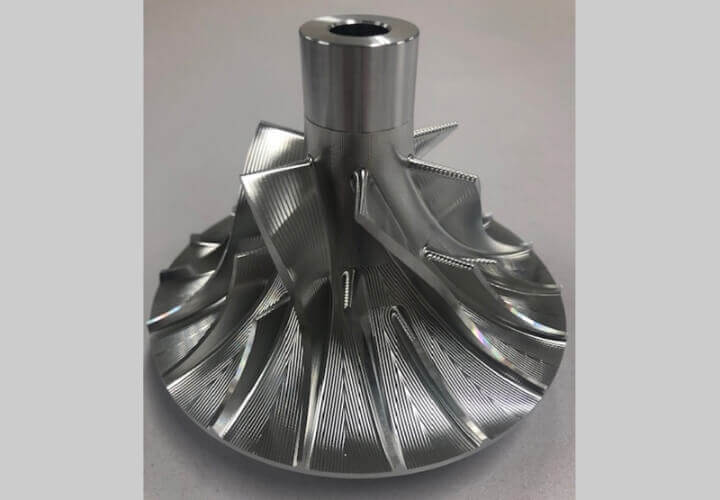
Shrouded Impellers
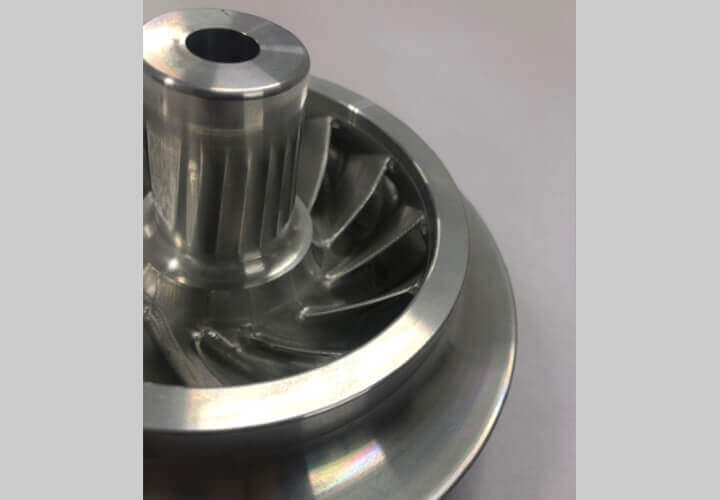
Impellers
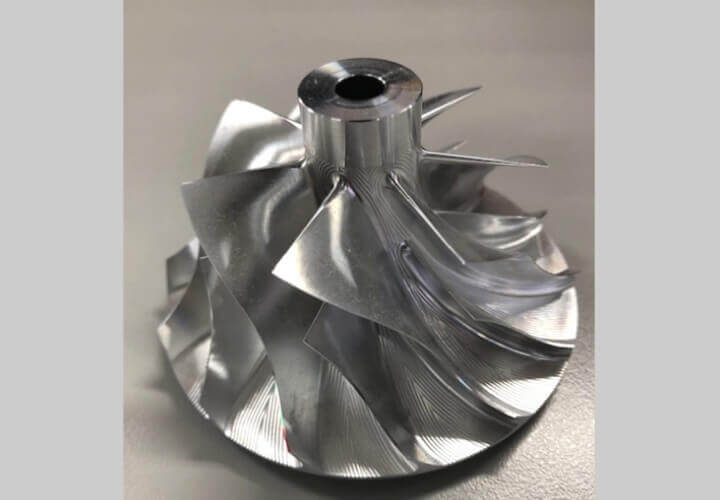
Small Impellers
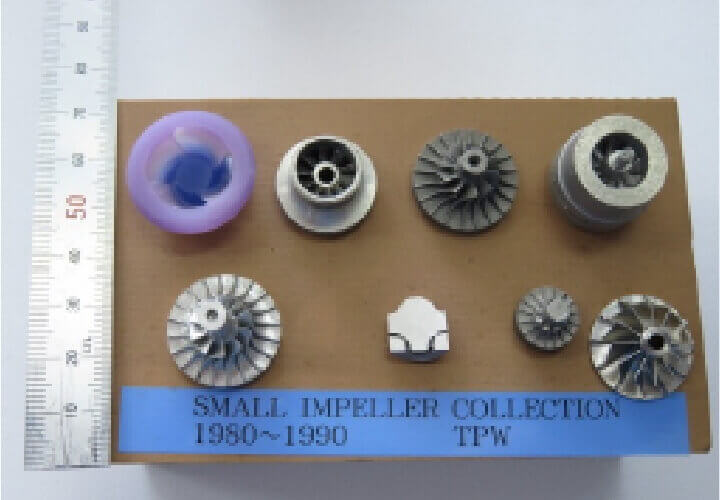
Turbine
Turbine Blade・Lost-Wax Pattern
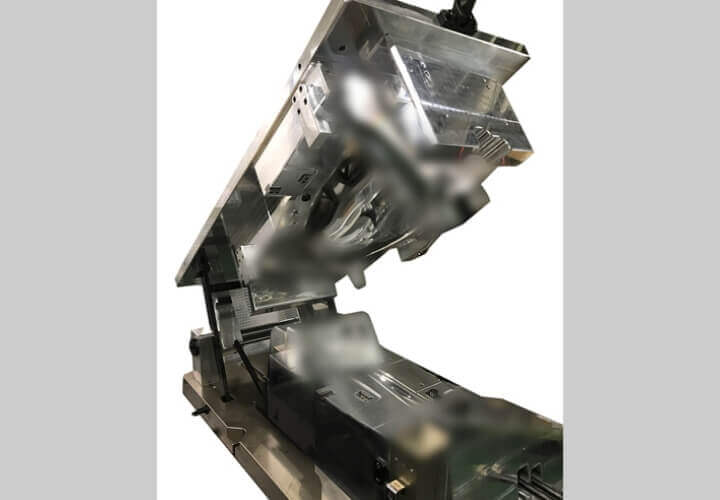
Turbine for Jet Engine
Blade・Lost-Wax Pattern
写真の提示出来ません
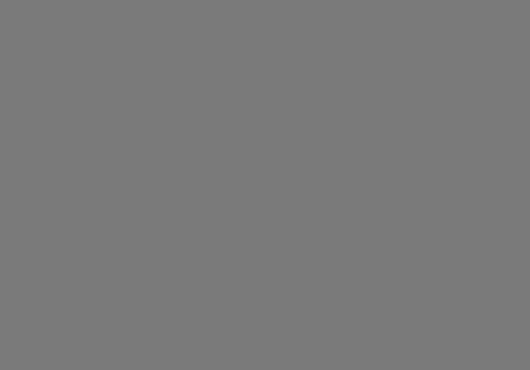
Others
Vacuum pump fixed blades
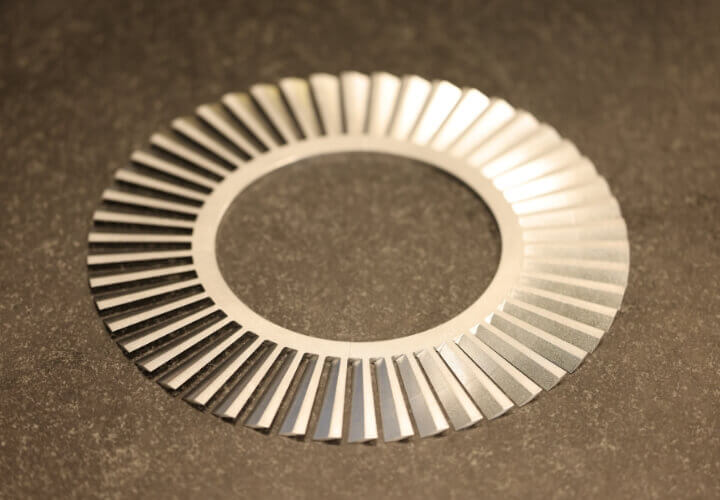
Exported to India Large Crank Case
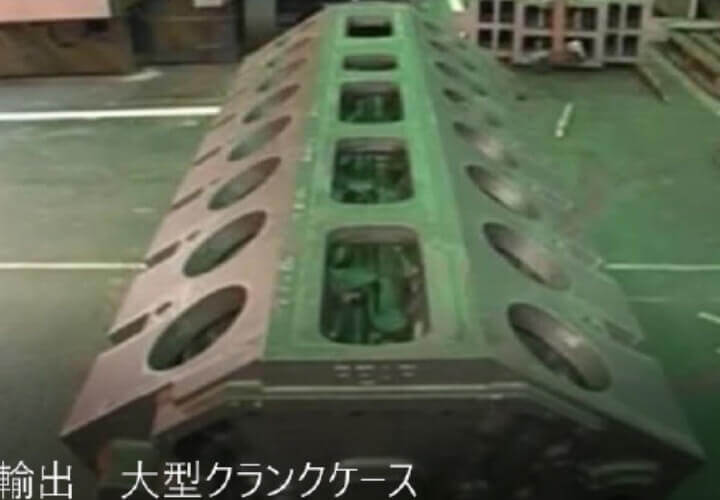
Exported to India Large Crank Case Metallic Core Boxes
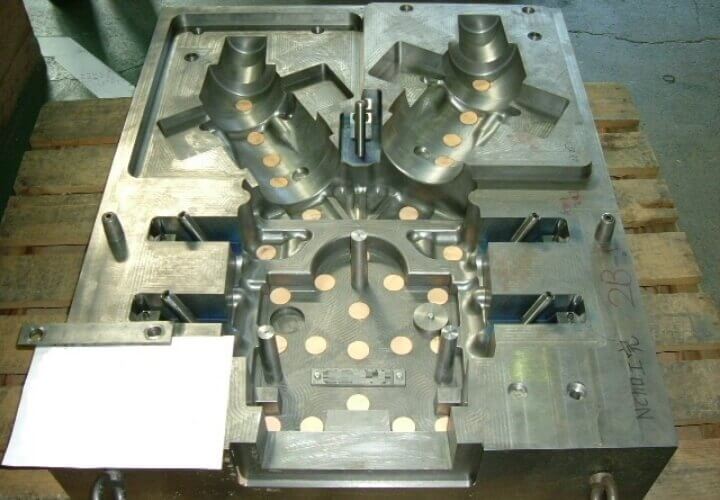
Exported to India Large Crank Case Setting Jig
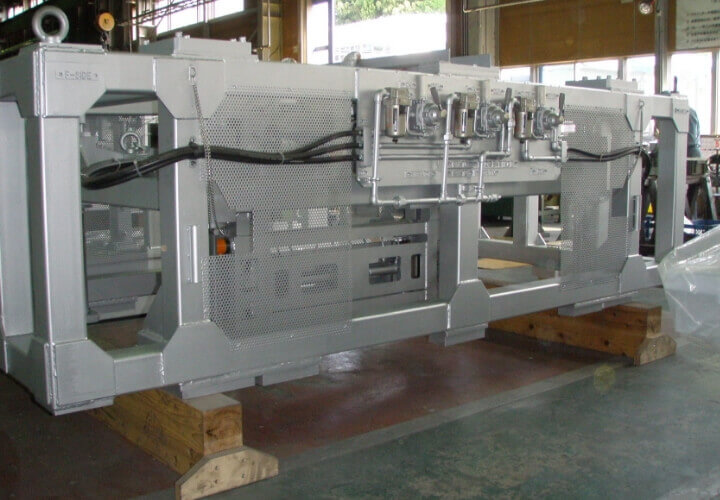
Exported to India Large Crank Case Machining Jig
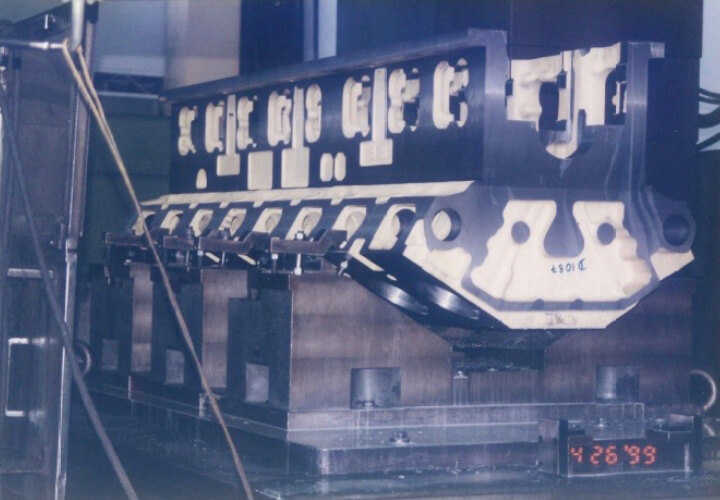
Exported to India V16 Cylinder Blocks for Generators Metallic Patterns
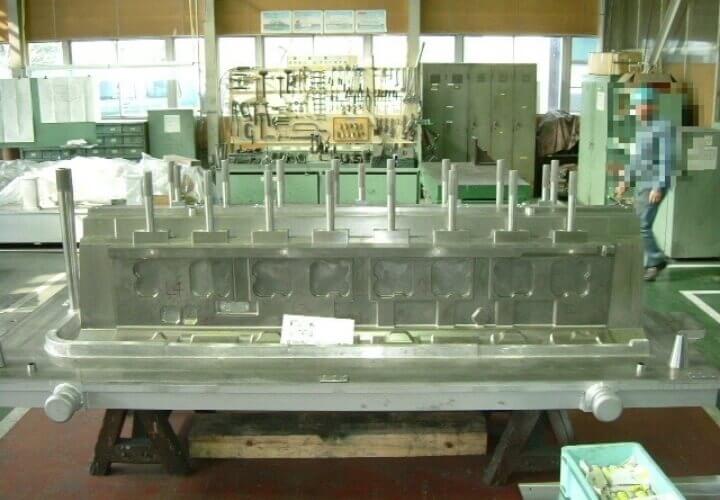
CYLINDER BLOCK
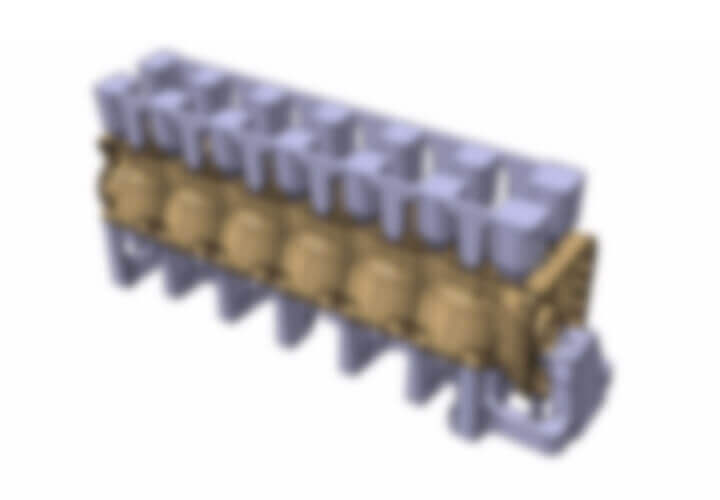
The example of Reverse Modeling
We create 3D data even when you only have the old drawings and sample products left.
- 1. Digitalize 3D data from an old drawing.
- 2. Measure the sample product with the contact-type measuring machine.
- 3. Compare the 3D data with the measurement result then verify the difference in shape.
- 4. Ask customers’ opinion about the part(s) they want to match with the sample product then perform reverse modeling accordingly.
- 5. Compare the 3D data from the reverse modeling with the sample product again to confirm the shape.
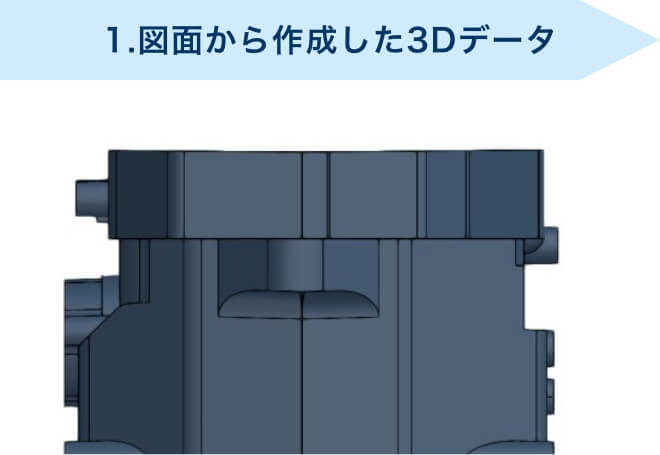
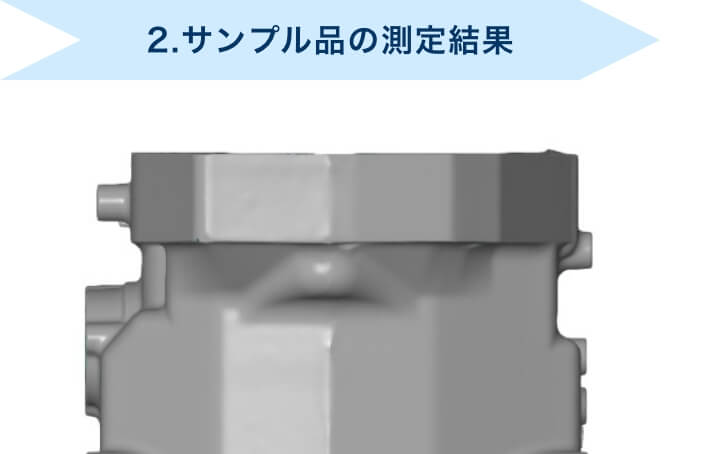
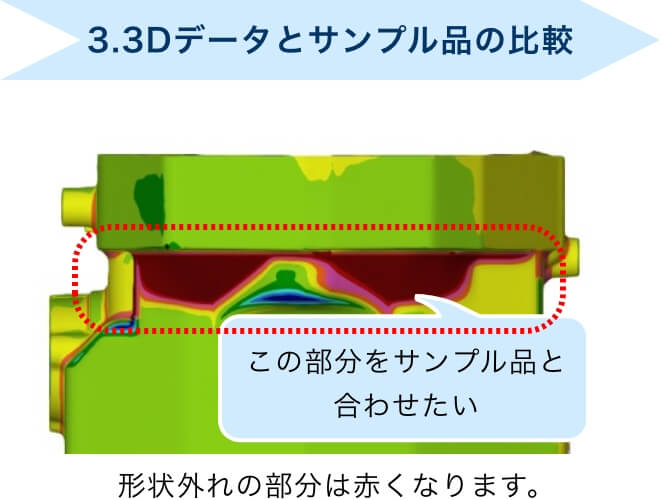
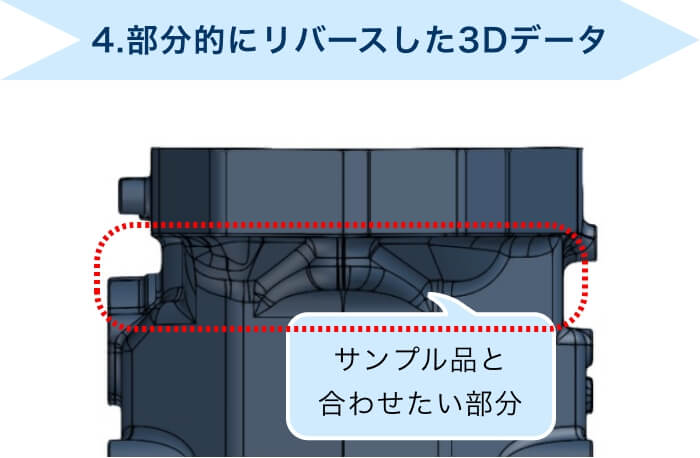
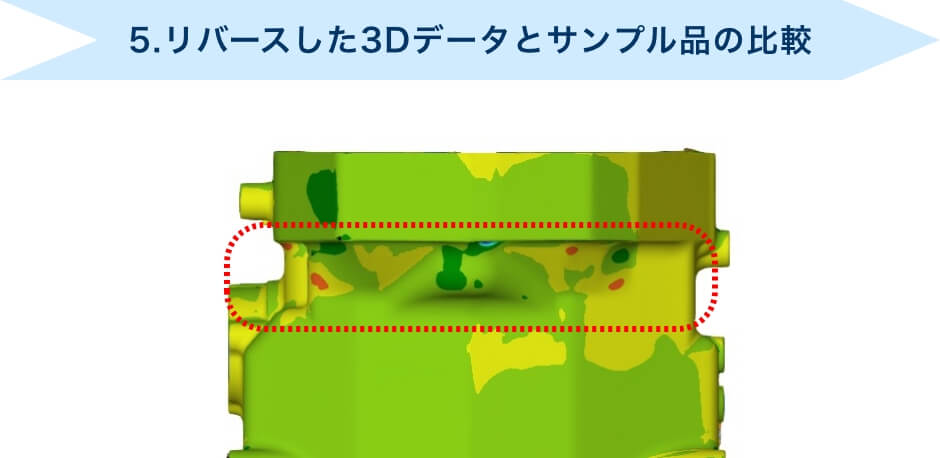